Introduction
Sodium aluminate is an important commercial inorganic chemical. It has been used as an effective source of aluminium hydroxide for many applications. Pure sodium aluminate (anhydrous) is a white crystalline solid having a formula variously given as NaAlO2, Na2O Al2O3, or Na2Al2O4.
The commercial importance of sodium aluminate is due to the versatility of its technological applications. In water treatment systems it is used as an adjunct to water softening systems, as a coagulant to remove suspended solids and some metals (Cr, Ba, Cu), and for removing dissolved silica. In construction technology, sodium aluminate is employed to accelerate the solidification of concrete, mainly when working during frosty periods [1-3]. It is also used in the paper industry, for refractory brick production and alumina production [4-5], etc. Furthermore, it is used as an intermediate in the production of zeolites for detergents, molecular sieves, adsorbents and catalysts [6-8].
Several methods for preparing solid sodium aluminate have been developed. In most methods, an aqueous sodium aluminate solution is prepared in a first step. Then, the sodium aluminate solution is dried in order to obtain the solid phase. A typical process for producing aqueous sodium aluminate is by dissolving aluminium hydroxides in a caustic soda solution [9]. In this case, a suspension of aluminum hydroxide with excess NaOH is prepared. Then, the suspension is passed through heated reaction tubes and the resulting sodium aluminate solution is spray dried. The product of this process is NaAlO2, NaAlO2∙1.5H2O or NaAlO2∙xH2O. In another process, sodium aluminate is prepared by solid state reaction of sodium hydroxide and subdivided aluminum hydrate, at a temperature above the melting point of the caustic soda but below 600°C [10]. It has been reported that sodium aluminate could be recovered from sodium dawsonite found in association with oil shales [11]. In this case, sodium aluminate was obtained by the reaction of homogeneously mixed sodium oxide and aluminum oxide, which were generated during thermal decomposition of sodium dawsonite.
In the present work, the preparation of sodium aluminate was investigated using basic aluminum sulfate (BAS) as a precursor. This latter compound was obtained by homogeneous precipitation of aluminum sulfate aqueous solution using ammonium bisulfite as a precipitant, as reported elsewhere [12]. In the next step of the process, the preparation of sodium dawsonite was investigated by treating BAS with sodium carbonate aqueous solution. Finally, this latter compound was heated at different temperatures to determine the formation temperature of sodium aluminate.
Experimental Procedure
The basic aluminum sulfate used in this work was obtained by precipitation in homogeneous solution by heating an aqueous solution of aluminum sulfate and ammonium bisulfite. This latter solution was obtained by passing sulfur dioxide through an ammonium hydroxide solution until a solution pH 4 was obtained. The 1 M sodium carbonate solution was prepared from reactive grade sodium carbonate from J. T. Baker.
The formation of sodium dawsonite was studied by adding 1.5 g of basic aluminum sulfate to each one of a series of 100 mL Erlenmeyer flasks. Then a different amount of 1 M Na2CO3 solution (1, 2, 3, 4,….17 mL) was added to each flask. Each solution was diluted to 25 mL with water. The flasks were left at room temperature for 72 hours. After this time, the pH of each solution was measured and the solution filtered at reduced pressure. Finally, the solids were dried at 80°C for 18 hours before analysis.
To determine the effect of temperature on the crystallization time of sodium dawsonite, a series of solutions was made up in 100 mL Erlenmeyer flasks. Then 1.5 g of BAS and 15 mL of 1 M Na2CO3 were added to each flask and diluted to 25 mL with water. Next, the flasks were heated at each temperature for various periods of time. After heating, the flasks were removed from the bath, cooled to ambient temperature, and the solutions filtered. The solids were washed with hot water and dried at 84°C for 18 hours prior to analysis.
To determine the thermal decomposition process and the crystallization temperature of sodium aluminate, several one gram samples of sodium dawsonite were heated at different temperatures in the range of 500-1100°C, for 30 minutes. After heating, the solids were characterized by X-ray diffractometry (XRD) and Fourier transform infrared (FTIR).
The pH of the solutions was measured by potentiometry (Model 420A, Orion, Beverly, MA, USA). XRD (Model D-500, Siemens, Germany) was carried out using Ni-filtered CuKα radiation. Infrared analysis was performed using KBr pellets and the samples were run on a FTIR spectrometer (Model 1600 series FTIR, Perkin Elmer, Norwalk, Connecticut, USA). Differential thermal analysis (DTA) and thermal gravimetric analysis (TGA) of the samples were obtained by heating 20 mg of sample up to 1300°C, at a rate of 10°C/min, in air (Model SDT 2960, TA instruments, New Castle, Delaware). The morphology of the particles was determined by scanning electron microscopy (SEM) (Model jsm-35C Jeol, Tokyo, Japan).
Results and Discussion
Structural evolution of BAS as a function of sodium carbonate concentration
The FTIR spectrum of BAS is shown in Figure 1. It shows the broad O-H stretching band in the 3000 to 3700 cm-1 range and the absorption band which peaks at 1655 cm-1 [13], indicating that the solid is a hydrate. The strong and broad band centered at 1135 cm-1 and the small shoulder at 998 cm-1 could be assigned to sulfate absorptions (ν3) and (ν1) respectively [14]. The strong and broad absorption band centered at 613 cm-1 probably resulted from the combined absorptions of sulfate (ν4), the Al-O stretching vibrations and the Al-OH wagging vibrational mode of molecular water. Therefore, this compound corresponded to a hydrated basic aluminum sulfate.
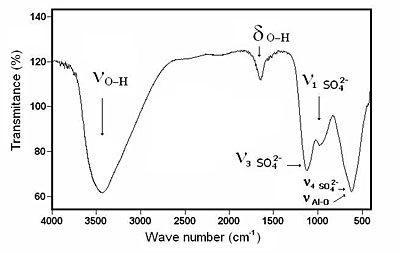
Figure 1. FTIR spectrum corresponding to basic aluminum sulfate.
The chemical transformation of BAS into sodium dawsonite at room temperature (28°C) can be seen in Figure 2. The FTIR spectra of the solids obtained by treating BAS with sodium carbonate solution show that the solids gradually lost sulfate and it became amorphous basic aluminum carbonate in the pH interval 4.3-10.1. As can be seen from spectra in Figure 2, the absorption peak corresponding to sulfate at 1135 cm-1 gradually decreased in intensity and, at the same time, the peaks corresponding to the splitting of carbonate absorption band ν3 at 1521 cm-1 and 1413 cm-1 [15], increased in size. Finally, at pH 10.1 the FTIR spectrum of the solid shows mainly the absorption bands corresponding to O-H at 3000 to 3700 cm-1 and 1655 cm-1, and to carbonate at 1521 cm-1 and 1413 cm-1. The broad absorption peaks exhibited by this solid indicates that the formation of an amorphous hydrated basic aluminum carbonate at pH 10.1 has occurred.
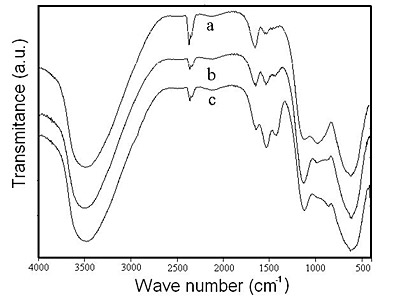
Figure 2. FTIR spectra of the solids obtained by treating BAS with sodium carbonate solution at: (a) pH 8.8; (b) pH 9.7; and (c) pH 10.1.
The first trace of crystalline sodium dawsonite in the solid was observed at pH 10.3 by FTIR, and the intensity of the absorptions peaks increase significantly in the pH range 10.3-10-6, as shown in Figure 3. The intensity of the absorption peaks corresponding to sodium dawsonite, as reported by Frueh and Golightly [16], remains constant at higher concentration of sodium carbonate, indicating that the maximum amount of dawsonite has crystallized at pH 10.6.
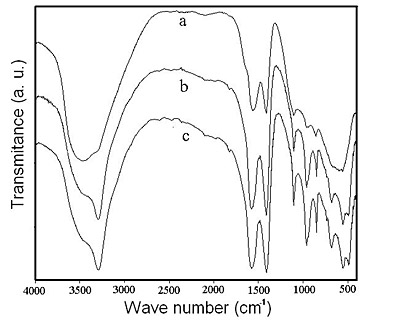
Figure 3. FTIR spectra of the solids obtained by treating BAS with sodium carbonate solution at: (a) pH 10.3; (b) pH 10.5; and (c) pH 10.6.
The amorphous structure of the solids obtained in the pH 4-10.1 range was confirmed by XRD. The diffractogram corresponding to these samples indicates that the solids are amorphous, as shown in Figure 4. On the other hand, the XRD analysis of the solid obtained at pH 10.6 shows the diffraction peaks corresponding to sodium dawsonite NaAl(OH)2CO3 [17]. Therefore, the formation of sodium dawsonite occurred at pH 10.6 by treating BAS with sodium carbonate. This result agrees with that reported by Zhang et al. for hydrothermally synthesized sodium dawsonite [18].
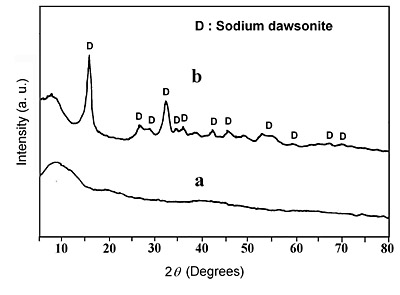
Figure 4. X-ray diffraction patterns of the solids obtained at: (a) pH 4-10.1 and (b) pH 10.6.
Chemical composition of solids as a function of sodium carbonate concentration
The solids were studied by thermogravimetric analysis. In Figure 5, the TG curves corresponding to BAS and to the solids obtained at pH 10.1 and pH 10.6 are shown. The curves of these two latter solids correspond to expectations for amorphous basic aluminum carbonate and sodium dawsonite respectively, as determined by FTIR.
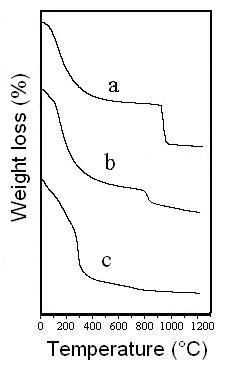
Figure 5. TG curves corresponding to: (a) BAS; (b) solid obtained at pH 10.1; and (c) solid obtained at pH 10.6.
As shown in Figure 5a, the TG curve of BAS exhibits two weight losses in the temperature ranges of 25-671°C and 671-1100°C. These weight losses can be attributed to water elimination (38.6 %) and sulfur trioxide (18.0 %) respectively. According to the TG data corresponding to BAS, the aluminum oxide content can be calculated as 43.4 wt.% and the empirical formula of BAS can be expressed as 1.9 Al2O3 ∙ SO3 ∙ 9.5 H2O.
The solid obtained at pH 10.1 presents two weight losses at temperature ranges of 25-600°C and 700-900°C. The first weight loss corresponds to the elimination of water and carbon dioxide whereas the second one is due to sulfur trioxide liberation. It is important to note that the sulfate content in this sample has diminished to 6.7%. This result agrees with the results obtained by FTIR for this sample (Figure 2c), because its FTIR spectrum shows weak sulfate absorption peaks.
The sample obtained at pH 10.6 shows only one weight loss at temperature range 25-400°C. The FTIR spectrum and XRD data indicated that the solid was sodium dawsonite, so this weight loss could be assigned to the elimination of water and carbon dioxide from the solid, according to the reaction:

However, it should be noticed that the sample heated at 400°C still contains a small quantity of carbon dioxide, as carbonate, and that this compound is eliminated after heating the solid at 800°C.
As a comparison, in Table 1 the thermal analysis data obtained for the solid prepared at pH 10.6 and sodium dawsonite with theoretical composition are shown. As can be seen from the data in Table 1, there is a small difference between the weight losses of these compounds, and this can be attributed to the presence of a very small quantity of some amorphous aluminum hydroxide in the solid obtained at pH 10.6. Therefore, it can be concluded that sodium dawsonite is the main constituent of the solid obtained at pH 10.6.
Table 1. Comparison of the thermal analysis data corresponding to sodium dawsonite with theoretical composition and sodium dawsonite obtained at pH 10.6.
|
Sodium dawsonite
|
Endothermic
|
43.1 (H2O and CO2 elimination)
|
56.9
|
Solid obtained at pH 10.6
|
Endothermic
|
41.7 (H2O and CO2 elimination)
|
58.5
|
Particle Size and morphology of sodium dawsonite
The particle size and morphology of BAS and sodium dawsonite were determined by SEM and the micrographs are shown in Figure 6. As can be seen from Figure 6a, the BAS is formed by agglomerates of more or less spherical particles, whose size is approximately 1 μm. On the other hand, the sodium dawsonite obtained at pH 10.6 is formed by agglomerates of small acicular particles less than 0.2 μm in size. It has been reported [19] that the particle morphology of natural sodium dawsonite is acicular, so the small acicular particles observed in the sample obtained at pH 10.6 very probably correspond to sodium dawsonite crystals.
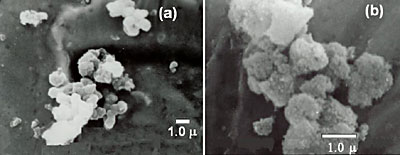
Figure 6. SEM micrographs corresponding to: (a) BAS and (b) sodium dawsonite obtained at pH 10.6.
Effect of temperature on crystallization time of sodium dawsonite
Once the required amount of sodium carbonate for sodium dawsonite crystallization was established, the effect of temperature and reaction time on crystallization time of dawsonite was determined. In order to accomplish this objective, 15 mL of 1 M sodium carbonate aqueous solution were added to several one-gram samples of BAS. Then, the samples were heated at different temperatures and times as shown in Table 2.
Table 2. Temperatures and reaction time for determination of crystallization time of sodium dawsonite.
|
94
|
1, 2
|
80
|
1, 2
|
70
|
1, 2, 4
|
60
|
2, 4, 6
|
50
|
4, 6, 8
|
The higher the heating temperature, the lower the crystallization time of sodium dawsonite. The evolution of the chemical structure of the solids heated at 50°C is presented in Figure 7, as determined by FTIR. The peaks corresponding to sodium dawsonite attained their maximum intensities after eight hours, indicating that the crystallization process of sodium dawsonite had finished at this time. As the temperature is raised at 60°C, 70°C and 80°C, the crystallization time of dawsonite diminished to 4 hours, 2 hours and 1 hour respectively.
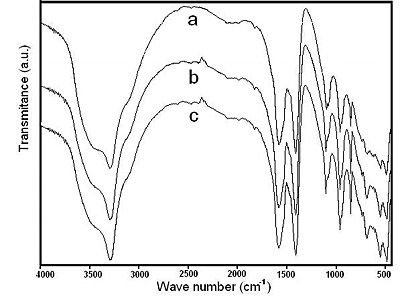
Figure 7. FTIR spectra corresponding to the solids obtained at 50°C after heating for: (a) 4 hours, (b) 6 hours and (c) 8 hours.
It should be noted that at high reaction temperatures such as 80°C and 94°C, the solid readily evolves to a mixture of sodium dawsonite and pseudoboehmite. The absorption peaks of dawsonite are lower in intensity whereas the absorption peak of psedoboehmite at 3079.8 cm-1 is higher in intensity as the reaction time increases, as shown in Figure 8, for the samples heated at 94°C. On the other hand, XRD analysis of the sample heated at 94°C for 2 hours indicates that the solid contains some amorphous aluminum hydroxide, pseudoboehmite and sodium dawsonite, as shown in Figure 9. Since pseudoboehmite is formed at temperatures higher than 70°C and the reaction time is larger at temperatures lower than 60°C, then 60°C and 4 hours of reaction time could be considered as the best experimental conditions for preparing sodium dawsonite by this method.
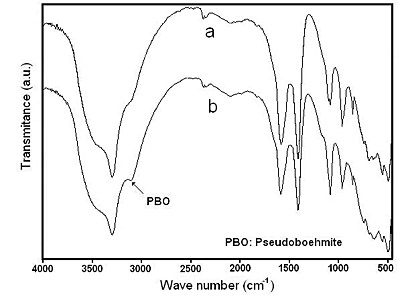
Figure 8. FTIR spectra corresponding to the solids obtained at 94°C after heating for: (a) 60 minutes and (b) 120 minutes.
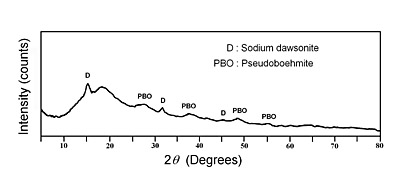
Figure 9. X-ray powder diffraction pattern corresponding to the solid obtained at 94°C after two hours of heating time.
Thermal decomposition of sodium dawsonite
The TG and DTA curves of sodium dawsonite obtained at 60°C are presented in Figure 10. According with thermal analysis curves (TG and DTA), a weight loss corresponding to 36.27% associated with an endothermic peak at 300°C was observed in the temperature range of 100-500°C. Furthermore, a small weight loss corresponding to 1.35% occurred in the temperature range of 500-800°C. The total weight loss amounted 37.62% and could be attributed to the elimination of carbon dioxide and water from the sample. On the other hand, the DTA trace showed a very small exothermic peak centered at 828°C, which could be assigned to sodium aluminate crystallization. Support for this hypothesis will be found in the XRD analysis of sodium dawsonite heated at different temperatures.
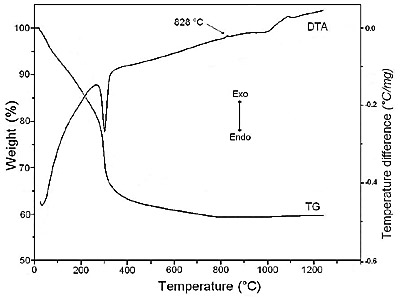
Figure 10. Thermal analysis of sodium dawsonite obtained at 60°C.
Harris et al. reported a small exothermic effect in the thermal analysis study of synthetic sodium dawsonite [20]. They observed the occurrence of a small exothermic peak centered at 650°C in the DTA curve of synthetic dawsonite, and detected the presence of sodium aluminate by XRD in the samples heated at 700°C and 800°C. The difference in the temperature of crystallization of sodium aluminate as observed in the sodium dawsonite studied by Harris et al. versus sodium dawsonite obtained here may be due to differences in crystallite size and crystallinity of the samples.
To determine the temperature at which sodium aluminate is formed, several samples of dawsonite were heated at 500°C, 600°C, 800°C, 900°C and 1000°C for 30 minutes and the resulting solids were analyzed by FTIR and XRD.
In Figure 11 are shown the FTIR spectra corresponding to the solid obtained after heating sodium dawsonite at 500°C and 700°C. In the temperature range of 500-700°C the spectra show two absorption bands at 1407 cm-1 and 1524 cm-1 corresponding to carbonate, which was probably absorbed by the solid from the air during the sample preparation. Furthermore, the spectra exhibit other two broad absorption bands in the 450-1000 cm-1 range, which are very similar to those exhibited by the gamma alumina phase [21]. Therefore, in this temperature range sodium dawsonite decomposes giving rise to a mixture of aluminum oxide and sodium oxide, as reported by M. Szczepanik and R. Rudnicki [22]. When the heated solids are exposed to air for a long time, the sodium oxide contained in the solid reacts with carbon dioxide from the air to form sodium carbonate, which is observed in the FTIR spectra.
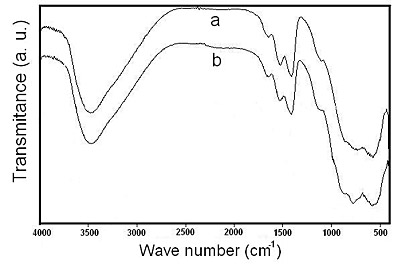
Figure 11. FTIR spectra corresponding to the solids obtained after heating sodium dawsonite at: (a) 500°C and (b) 700°C.
The FTIR spectra of the samples heated at 800°C, 900°C and 1100°C are shown in Figure 12. In this case, sharp absorption peaks at 559 cm-1, 711 cm-1 and 883 cm-1 and the absorption peak corresponding to carbonate stretching band at 1450 cm-1 appear. As the temperature raises, the intensity of the absorptions peaks at 559 cm-1, 711 cm-1 and 1100 cm-1 increase in intensity, indicating that crystalline sodium aluminate begins to form at 800°C. Its important to notice that the sample heated at 1100°C exhibits sharp absorption peaks at 456 cm-1, 594 cm-1 and 649 cm-1 corresponding to alpha alumina, which could be produced by thermal decomposition of sodium aluminate at high temperature as reported by Zvezdinskaya et al. [23].
The XRD patterns of sodium dawsonite heated at 600°C, 800°C, 900°C and 1000°C are presented in Figure 13. At 600 °C, the XRD pattern corresponds to transition alumina (gamma/eta). At higher temperatures such as 800 °C and 900 °C, the spacings corresponding to a more crystalline sodium aluminate can be identified. Finally, the spacings corresponding to alpha alumina can be observed in the spectrum of the sample heated at 1000°C. Therefore, the FTIR data together with the XRD patterns corresponding to the heated samples, allow the following scheme to be proposed for the decomposition of sodium dawsonite:
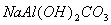
|

|

|

|

|
Sodium dawsonite
|
|
Transition alumina
|
|
Sodium aluminate
|
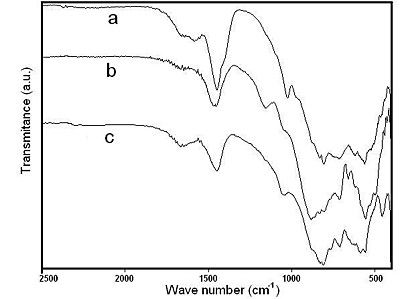
Figure 12. FTIR spectra of solids obtained after heating sodium dawsonite at: (a) 800°C, (b) 900°C and (c) 1100°C.
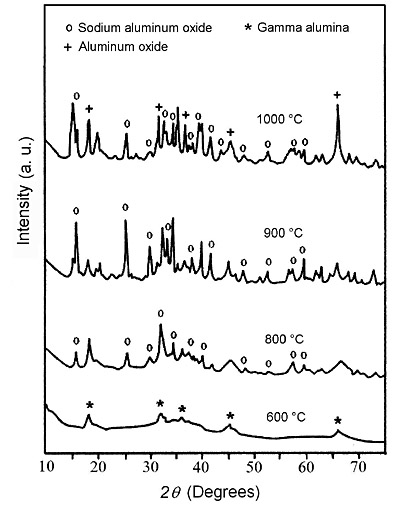
Figure 13. XRD spectra corresponding to sodium dawsonite heated at different temperatures for 30 minutes.
It should be mentioned that this scheme agrees with that previously reported by Hernández and Ulibarri for sodium dawsonite prepared by a hydrothermal process [24].
Conclusion
Sodium aluminate was prepared by using basic aluminum sulfate as a raw material. In the first step of the process, sodium dawsonite was obtained by treating basic aluminum sulfate with sodium carbonate aqueous solution at 60°C for 4 hours. Higher heating temperatures gave rise to the formation of pseudoboehmite as well as sodium dawsonite in the sample. The crystallization of sodium dawsonite in the solid occurred through the formation of an amorphous basic aluminum carbonate as an intermediate compound. The dawsonite powder was formed by highly agglomerated acicular particles, whose size ranged from 0.1-0.2μm. In order to obtain sodium aluminate, sodium dawsonite was heated at different temperatures for 30 minutes and the phase transformation sequence was determined. Based on the XRD patterns of the solids obtained after heating sodium dawsonite at different temperatures, the phase sequence could be determined as sodium dawsonite, amorphous, transition alumina (gamma/eta) and crystalline sodium aluminate. By this method, crystalline sodium aluminate could be obtained by heating sodium dawsonite at 900°C for 30 minutes.
Acknowledgements
The authors wish to express their gratitude to Juan José Guzmán A., Director of the Centro de Investigaciones en Química Inorgánica for his permission to publish this paper. Yolanda Gallaga, Diana Mendoza and Juan Balderas are acknowledged gratefully for the instrumental data interpretation and technical assistance.
References
1. H. Yong, “Highly-concentrated polyiron sulfate-type coagulant for water purification”, Chinese patent, No. 1473770 (02 November 2004).
2. I. Heihichi and G. S. Kyoku, “Adsorbents for gas-phase odor control or liquid-phase heavy metal removal”, Japanese patent, No. 47023383 (12 November 1972).
3. M. Wakasugi, H. Sakakibara, S. Ando and T. Kitora, “Method for wet-spray application of ultra rapid-hardening cement mortar and concrete”, Japanese patent, No. 2003080515 (19 March 2003).
4. T. Ploetz and L. Scheuring, “Application of sodium aluminate in papermaking. II. Influence on retention by aluminum sulfate and sodium aluminate addition, when the total Al2O3 is kept constant”, Papier (Bingen, Germany), 10 (1956) 183-189.
5. G. Jianfeng, X. Chunyan, W. Jianzhong, W. Jiufen and Z. Yuanyi, “Direct preparation of high-purity γ-alumina from sodium aluminate”, Huagong Xuebao (Chinese Edition), 54 [12] (2003) 1783-1786.
6. H. Shemin, “Method for preparing sodium metaaluminate solution for synthesis of zeolite with diasporite”, Chinese patent, No. 401577 (12 March 2003).
7. W. Yimeng, Z. Bin, S. Xingtian and H. Mingyuan, “Process for synthesizing molecular sieve (MCM-22) with special crystal structure”, Chinese patent, No. 1296913 (30 May 2001).
8. K. S. Wook, K. B. Ho and I. Heishichi, “Chemical utilization of dawsonite. II. Preparation of the catalysts nickel-alumina, cobalt-alumina, chromium-alumina, from synthetic dawsonite and their characteristic properties”, Kogyo Kagaku Zasshi, 74 [10] (1971) 1987-1992.
9. D. Helmut, H. Wolfgang and H. Dietmar, “Process and apparatus for the manufacture of sodium aluminate”, European patent, No. 387492 (19 September 1990).
10. R. L. Davies, “Sodium aluminate”, US Patent, No. 2159843 (23 May 1939).
11. Oil Shale Corp., “Recovery of sodium aluminate from dawsonite”, British patent, No. 1166785 (8 October 1969).
12. S. Sugita, C. A. Contreras, H. Juarez, A. Aguilera and J. Serrato, “Homogeneous precipitation and thermal phase transformation of mullite ceramic precursor”, International Journal of Inorganic Materials, 3 (2001) 625-632.
13. K. Nakamoto, “Infrared and Raman Spectra of Inorganic and Coordination Compounds”, ed. Wiley, New York, (1978) pp. 103-110.
14. C. J. Serna, J. L. White and S. L. Hem, “Anion-Aluminum Hydroxide Interactions”, Soil Sci. Soc. Am. J., 42 (1977) 1009-1013.
15. C. J. Serna, J. L. White and S. L. Hem, “Structural Survey of Carbonate Containing Antacids”, Journal of Pharmaceutical Sciences, 67 [3] (1978) 324-327.
16. J. Frueh and J. P.Golightly, “The Crystal Structure of Dawsonite”, The Canadian Mineralogist, August (1966) 51-56.
17. J. Serna, J. L. White and S. L. Hem, “Hydrolysis of Aluminum-Tri-(Sec-Butoxide) in Ionic and Nonionic Media”, Clays and Clay Minerals, 25 (1977) 384-391.
18. Z. Xiang, W. Zhaoyin, X. Xiaote and L. Zugiang, “Hydrothermal Synthesis and Thermodynamic analysis of Dawsonite type Compounds”, Journal of Solid State Chemistry, 177 (2004) 849-855.
19. E. S. Dana, “Dana’s Textbook of Mineralogy”, Fourth edition, ed. John Wiley & Sons, New York, (1976) p. 529.
20. L. A. Harris, W. Ernst and V. J. Tennery, “A High Temperature X-Ray and Thermal Analysis Study of Synthetic Dawsonite”, The American Mineralogist, 56, May-June (1971) 111-1114.
21. J. A. Gadsden, “Infrared Spectra of Minerals and Related Inorganic Compounds”, ed. Butterworths, England, (1975) p. 43.
22. M. Szczepanic and R. Rudnicki, “Thermal Decomposition of Synthetic Dawsonite”, Polish Journal of Chemistry, 55 (1981) 1483-1489.
23. L. V. Zvezdinskaya, V. A. Mitrokhin and I. S. Delitsin, “Thermal-x-ray diffraction study of dawsonite”, Izvestiya Akademii Nauk SSSR, Seriya Geologicheskaya, 10 (1986) 137-141.
24. M. J. Hernández and M. A. Ulibarri, “Thermal Stability of Aluminum Hydroxycarbonates with Monovalent Cations”, Thermochimica Acta, 94 (1985) 257-266.
Contact Details
César A. Contreras, Satoshi Sugita and Esthela Ramos
CIQI, Universidad de Guanajuato.
Noria Alta s/n, Col. Noria Alta
Guanajuato, Gto.,
Mexico. C.P. 36050
E-mail: [email protected]
|
|