Introduction Ni aluminides have a variety of exceptional mechanical properties which makes these materials good candidates for commercial applications [1, 2]. They have B2 and L12 lattice structure types and they can be useful materials for high temperature applications, particularly where corrosion and oxidation resistance are required [3]. They have low densities providing attractive resistance-weight relation. Their resistance to oxidation is well known and has been used in the coating of Ni alloys [4]. Such resistance is related with the formation of an alumina film. Normal casting techniques have been used in the past to produce different intermetallic compounds [5]. Furthermore, the addition of small amounts of different elements to the intermetallic alloys has been used in the past as a method to improve the mechanical properties of these materials at low temperatures [6-8]. Previous investigations [9, 10] have shown that Li reduces the brittle nature of AlCuFe and AlFe intermetallic alloys. The additions of Li have shown in the past, mechanical property improvements in different intermetallic alloys, therefore the main goal of the present work was to explore the effects of the additions of Li to produce intermetallic phases in the Ni-Al alloy system and evaluate the mechanical properties and structural characteristics. Experimental Intermetallic alloys with a composition of Ni72Al28 and additions of Li in amounts of 1, 3 and 5 at.% were obtained using an induction furnace (20 Kg capacity) by conventional casting techniques. High purity of (99.9%) raw material (Ni and Al) were melted in a SiC crucibles and poured into sand moulds whose cavities were already with the shapes of the tensile specimens following the ASTM E800b norm. Cylindrical specimens were obtained whose dimensions were 12.7 mm in diameter and 50.8 mm in length. Mechanical tests (tensile and hardness tests) were undertaken for all the alloys both as-cast and after the annealed process at 400°C for 144 hours. The microstructural characterization was carried out using X-ray diffraction patterns (XRD) with Cu radiation (λCu=0.15405 nm) in a D5000 Siemens instrument. Also, scanning electron microscopy (SEM) observations were carried out with a JEOL 6400 microscope. Hardness measurements (Wilson Durometer) were obtained in the Rockwell C scale. The tensile test was performed in a Wolpert testing machine (200 KN) at constant speed (10 mm/min) and room-temperature. Results and Discussion Figure 1a shows the stress-strain results for the Ni72Al28 as-cast specimens with different additions of Li (1, 3 and 5 at.%). This figure shows that best deformation values are obtained with the highest addition of Li (5 at.%). Similarly this alloy has the best yield strength (YS) values and also the best ultimate tensile stress (UTS) values, in comparison with other additions. These values were 848 and 501 MPa for the UTS and YS respectively. The summary of these mechanical property parameters are illustrated in Table 1. The results indicate an 8% of elongation which represents a 14.3% higher value that the value obtained in similar alloys without any element addition. On the other hand, Figure 1b shows the stress-strain results for the same alloys after the heat treatment. In this case, all the alloys improve their deformation percentaje in comparison with the values for the alloys without heat treatment. The alloys with 3 and 5 at.% Li additions cases have the best values of YS and UTS. The alloy with 1 at.% Li addition shows the best elongation values. The heat treated specimens show in general, the same characteristics of the alloys without heat treatments: the increment in the additions of Li improve the mechanical properties of the Ni3Al alloys. For the addition of 5 at.% Li, the deformation values were of the 8.7%. This result improves in 10% the values obtained from the same alloy without additions (7.9% deformation). The UTS and YS values were better in these specimens: 887 and 575 MPa respectively. Figure 2 shows the hardness behavior of the alloys with compositions of Ni72Al28 and Li additions (before and after the heat treatments). Left (dark) bars correspond to heat treated specimens, right (gray) bars correspond to as-casted specimens. Therefore, the heat treatment tends to slightly reduce the hardness of the intermetallics. The alloy structure observed in the SEM instrument shows two different phases with columnar grains morphologies. Figure 3a is a backscattered electron image (BEI) which corresponds to the heat treated specimen with 5 at.% of Li additions. In this micrograph, the contrast is generated by the atomic number therefore two different contrasts are observed which suggest two different phases. The light gray region corresponds to the Ni3Al intermetallic composition with L12 cubic structure while the dark region corresponds to NiAl phase with a B2 cubic structure. Figure 3b is a secondary electron image (SEI) from a 3 at.% Li alloy. A reversed contrast is observed in comparison with Figure 3a. In addition, an etching feature contrast is observed between the two phases since NiAl corroded faster than Ni3Al. Furthermore, NiAl shows a different image contrast appearence due to the presence of line profiles inside the grain, which could be associated with multiple twining. Table 1. Summary of the stress-strain parameter results of the intermetallic compound Ni3Al from specimens with and without heat treatments. | Ni3Al | 7 | 672 | 296 | 7.9 | 655 | 410 | Ni3Al + 1Li | 7.1 | 663 | 432 | 8.8 | 550 | 356 | Ni3Al + 3Li | 7.4 | 681 | 418 | 8.10 | 905 | 516 | Ni3Al + 5Li | 8 | 848 | 501 | 8.7 | 887 | 575 | 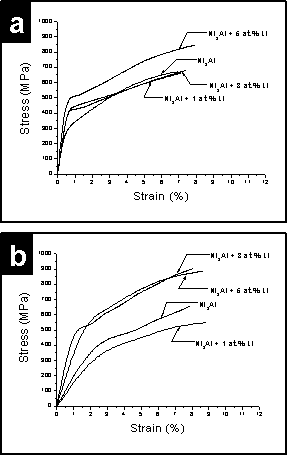 Figure 1. Stress-strain results for the specimens: Ni72Al28 with Li additions. a) Without heat treatment (WHT), b) Heat treated (HT). 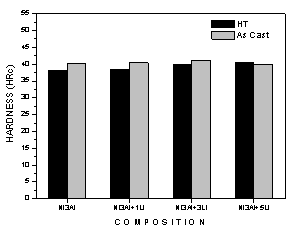 Figure 2. Hardness values (HRc) of the Ni3Al intermetallic compounds before and after the heat treatments. 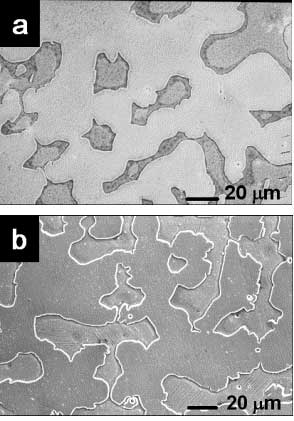 Figure 3. SEM images obtained from the as-cast and heat treated specimen. a) BEI of the heat treated alloy with 5 at% of Li addition and b) SEI of as-casted alloy with 3 at.% of Li addition. Figures 4 a-d show SEM micrographs (BEI) obtained from the different alloys. Figures 4a and 4b are micrographs from samples without heat treatment; Figure 4a shows the alloy with no additions and Figure 4b corresponds to the 5 at.% Li alloy. While Figures 4c and 4d show micrographs of the samples with heat treatment (without additions and 5 at.% Li, respectively). From these micrographs, small but clear microstructural changes can be observed. An increase in the volume fraction of the L12 phase as Li increases (Figures 4a and 4b) can be observed. In addition, an increase of the L12/B2 ratio was observed after the samples were heat treated (compare Figures 4a and 4c with Figures 4b and 4d). 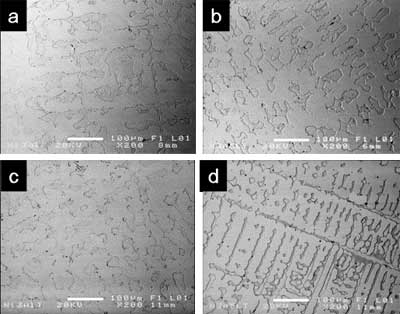 Figure 4. Different BEI-SEM micrographs. a) as-cast specimen without additions, b) as-casted 5 at% Li alloy, c) heat treated sample with no additions and d) heat treated 5 at.% Li alloy. Some microstructural changes were observed in the alloys after being heat treated, modification of the distribution and size of crystalline grain of the brittle B2 phase, which in turn contributes to the mechanical behaviour improvement. Grain size of the B2 phase seems to diminish and better distributed along the structure not only when the lithium content increases but also due to the heat treatment. It should be noted that the heat treated 5 at.% Li alloy shows a preferred grain growth direction (texture) (see Figure 4d). The best mechanical properties were obtained from this alloy and this result could be related with the Li additions to the alloy. We attribute these improved results to the microstructural changes observed when Li was added: texturization of the softer L12 phase and a small decrease of the highly twinned brittle B2 phase. All of this contributes to increase ductility in the alloy with no negative effects on the mechanical strength. Conclusions In this study, intermetallic alloys based on Ni72Al28 at.% with Li additions (1, 3 and 5 at.%) were prepared by conventional casting methods. The best deformation values were obtained with the highest addition of Li (5 at.%). The results indicate an 8% elongation which represents a 14.3% higher than the value obtained in similar alloys without any element addition. The heat treatments improve also the ductility of the intermetallic. In this case, all the alloys improve their deformation percentage. For the addition of 5 at.% Li, the deformation values were 8.7%. This result improves in 10% the values obtained from the same alloy without additions (7.9% deformation). On the other hand, the presence of L12 cubic phase tends to increase with the additions of Li. We attribute these improved results to the microstructural changes observed when Li was added to intermetallic alloy. References 1. S. C. Deevi and V. K. Sikka, “Nickel and Iron Aluminides: An Overview on Properties, Processing and Applications”, Intermetallics, 4, 357-375 (1996). 2. C. T. Liu and E. P. George, “Recent Advances in Alloy Design of Ni3Al Alloys”, Proceedings of the International Symposium on Nickel and Iron Aluminides: Processing, Properties, and Applications, ASM, Materials Park, OH, 21-32 (1996). 3. C. G. McKamey, Chapter 9 Iron Aluminides, in Phisical Metallurgy and Processing of Intermetallic Compounds, Edited by N. S. Stoloff and V. K. Sikka, 368-380 (1996). 4. S. C. Dee, P. Morris and V. K. Sikka, “Reaction Synthesis and Processing of Nickel and Iron Aluminides”, Proceedings of the International Symposium on Nickel and Iron Aluminides: Processing, Properties, and Applications, ASM, Materials Park, OH, 283-300 (1996). 5. C. T. Liu, E. P. George, P.J. Maziasz and J. H. Schneibel, “Recent Advances in B2 Iron Aluminide Alloys: Deformation, Fracture and Alloy Design”, Mater. Sci. and Eng. A, 258, 84-98 (1998). 6. R. Darolia and D. Lahrman, “The Effect of Gallium, Iron and Molybdenum on the Room Temperature Tensile Ductility of NiAl”, Scripta. Metall. Mater., 26, 1007-1012 (1992). 7. J. Zhou and J. T. Guo, “Effect of Ag Alloying on Microstructure, Mechanical and Electrical Properties of NiAl Intermetallic Compound”, Mater. Sci. and Eng. A, 339 (2003) 166-174 8. V. Rothova and J. Cermak, “Bulk and Grain Boundary Diffusion of Ga in Ni3Al Influence of Composition”, Intermetallics, 13, 113-120 (2005). 9. M. Salazar, R. Pérez and G. Rosas, “Environmental Embrittlement Characteristics of the AlFe and AlCuFe Intermetallic Systems”, J. New Mat. Electrochem. Systems, 8, 97-100 (2005). 10. M. Salazar, R. Pérez and G. Rosas, “The Effect of Li, Ce and Ni Additions on the Microstructure and the Mechanical Properties in the AlFe Intermetallic System”, Mater. Sci. Forum, 426-432, 1837-1842 (2003). Contact Details |