Overgrinding represents a substantial problem in milling, due mainly to the use of low throughput off-line particle size characterization methods. It is a problem in many industries, from pharmaceuticals (where the cost of the product is very high, and overgrinding leads to low yields), to cement manufacture (where there is a very high throughput and intensive energy requirements, and overgrinding means higher energy costs and lower throughput).
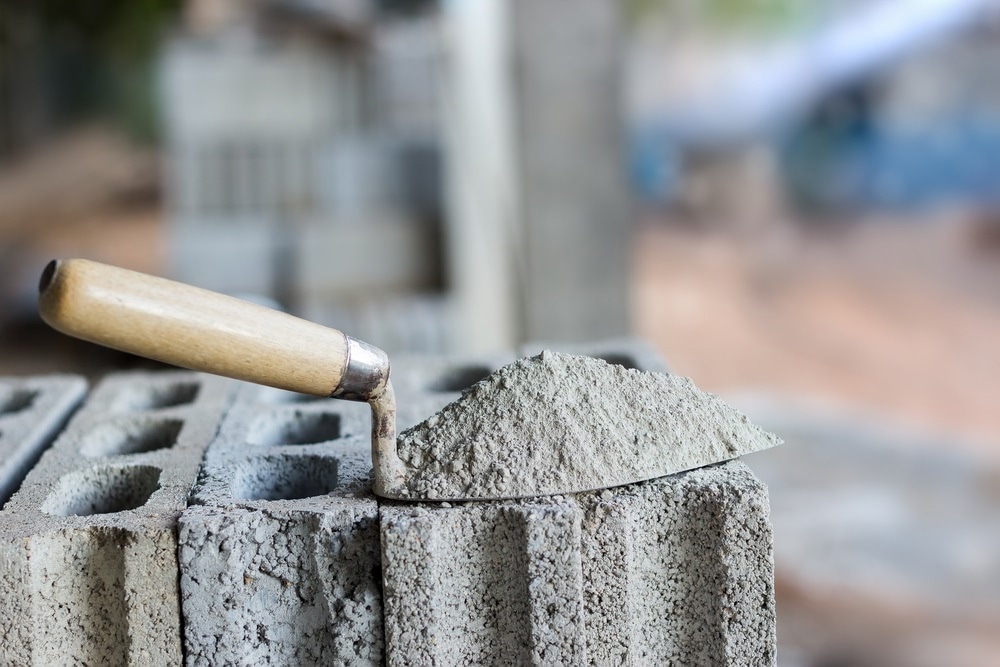
Image Credits: okcm/shutterstock.com
This can be reduced substantially with the use of Insitec, the real-time in-process particle size analyzer.
Case Study: The Cement Industry
High throughput (generally 20-150 t/h dependent on mill), high energy requirements for grinding. Ceramic ball mills are generally used with a dynamic separator to recycle coarse particles.
Typical Production Figures
100 t/h will normally mean using at least 100 tonnes of ceramic balls and a recycle rate of around 2/3 which means that around 300 t/h of cement is going through the mill. A very large amount of energy is required to mill the cement. The finer the cement is required, the higher the recycle rate (and therefore lower the yield and throughput) and the higher the energy costs.
The relationship between fineness and energy required to grind it is more likely to be exponential rather than linear. The objective therefore is to grind as close to the coarsest size possible without going outside the limits of the specification.
Using Manual Off-Line Particle Size Analysis Measurements
Manual off-line measurements are generally taken every 2-4 hours. The measurement is generally does not have a high repeatability due to vagaries in manual sampling and operator error.
At one company, the samples could be taken by any one of 20 different operators! For this reason, the process is operated relatively far from the maximum specification so as to prevent the product drifting out of specification during the time before the next sample is measured.
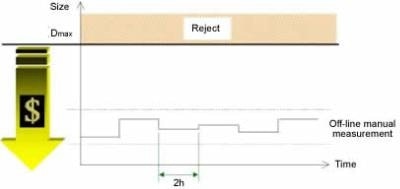
Figure 1. Particle size using manual off-line particle size analysis measurements.
Benefits of Using On-Line Particle Size Analysis Measurement
In going to on-line particle sizing, automatic continuous sampling and measurement will improve the repeatability of the size result. The measurement becomes more statistically significant as several kilograms of sample are now measured per hour, instead of a few grams every 2-4h.
Laser diffraction gives much richer information on the particle size distribution than many off-line measurements, further enhancing the plant operators view of the process. All of these benefits help to increase dramatically the confidence limits on the measurement. Now the process should always remain in specification, as alarms can sound should the product size deviate by more than a set amount.
Automatic Process Control
To improve the situation even further, automatic process control via a simple PID control loop to the classifier, or more performant MIMO controller, will further tighten the measured size parameters.
In this situation, the operator then only needs to "dial-in" the product specification required, and it is the controller which will find the optimal setting.
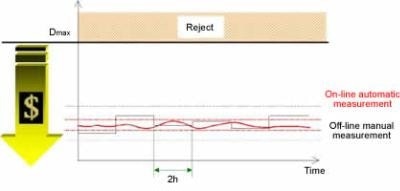
Figure 2. Comparison or on-line and manual particle size analysis measurements.
Summary of the Benefits of On-Line Particle Size Analysis and Automated Process Control in Cement processing
If you are now using on-line particle sizing, perhaps coupled with automatic process control, why stay so far away from the specification limit. Your process won't drift in the same way a manually monitored process might. With on-line sizing, manufacturers can now afford to sail closer to the wind and grind closer to the maximum specification.
Although this will coarsen the product, the product will always stay in specification and give a much more consistent product with much less batch-to-batch variation. The overgrinding will be significantly minimized, leading to higher throughputs and lower energy requirements.
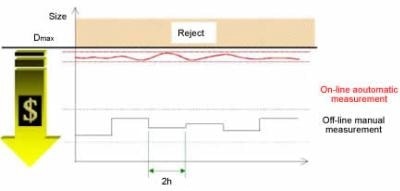
Figure 3. Comparison of particle size analysis using on-line particle size measurements combined with automatic process control and manual particle size analysis measurements.
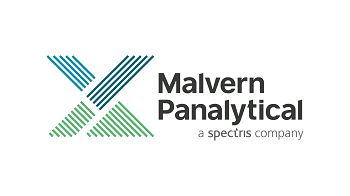
This information has been sourced, reviewed and adapted from materials provided by Malvern Panalytical.
For more information on this source, please visit Malvern Panalytical.