The use of magnetic inks to produce cards with strips containing information or, more recently, documents with magnetic characters which are read directly is becoming more widespread.
Magnetic strip cards are used as ID cards, transport cards and season tickets, credit cards and entry cards. Also, characters may be printed on to documents (e.g. bank cheques or mail) which are then sorted by means of a magnetic reader.
These applications afford problems to the formulator since, in the case of the magnetic strip, the ink has to be of sufficient low viscosity to form a thin film on the card, but needs to be of sufficient body to print the characters clearly.
Introduction to Ferro-Magnetic Particles
Introduction Magnetic inks of this type consist of ferro-magneto pigment particles (~30%), a resin (~10%) and a solvent (~60%). There are some other constituents present to aid, for example, adhesion and dispersion. It is important that these types of ink do not exhibit too much body as this would cause problems during pumping, but they have to have sufficient body so as not to show syneresis during storage and transportation. Also, they have to be rapidly shear thinning on application so as to form a uniformly thin film of ink on the substrate.
For the strip cards, the particles have to be well dispersed as this can cause problems in reading information to and from the card.
Properties That Can Be Quantified using Rheological Methods
Description of the problem There are a number of properties associated with these types of ink that can be quantified using rheological methods:
- Pumping - in some instances the inks need to be pumped in order to be in place for application or transportation;
- Application - the inks will be applied either via rollers and printing blankets or screens; and
- Information transfer/reading - when the ink has been applied on the card in the form of a film it needs to have uniform properties in order to receive information and then be read.
These properties can be accessed using modern rheometers by designing experiments that either simulate closely the process of interest or, by using prior knowledge of dispersion behavior, give microstructural information from the bulk rheological properties.
Rheological analysis
All of the experiments in this note were performed on a Bohlin rotational rheometer.
Viscometry Measurements
Figures 1 (a) and 1 (b) show data for two magnetic inks - curve (a) has shear rate on the x-axis, while curve (b) has shear stress on the x-axis. In this experiment, a stress is applied to the material and the resulting shear rate is measured.
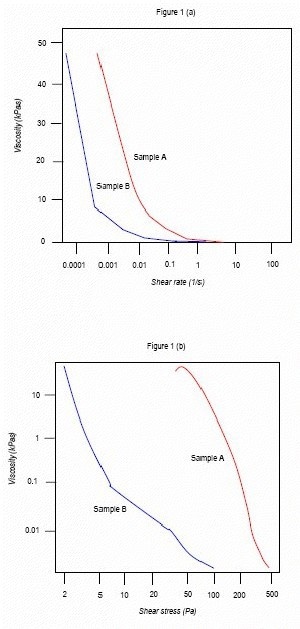
Figure 1. (a) Viscosity vs. shear rate, and (b) viscosity vs. shear stress for two magnetic inks.
The viscosity is calculated using the simple relationship: viscosity = shear stress/shear rate. The stress is increased step-wise during the experiment and the viscosity calculated at each stress.
In (a) the viscosities of A and B become asymptotic above a shear rate of about 0.1 s-1, indicating that conventional tests on viscometers would show no differences between the two samples. However, at low shear rates (and low shear stresses - Figure 1 (b) there are very large differences in the samples. These differences are due to differences in the microstructure of the inks, which may be caused by variations in the properties of the raw materials or non-reproducible production of the ink dispersion. This will, almost definitely, result in differences in performance of the inks.
Yield Stress Analysis
Figure 2 shows curves produced using the yield stress analysis software of the Bohlin rheometer. In this test, the stress is gradually ramped upwards over a pre-set time scale.

Figure 2. Yield stress analysis curve produced using Bohlin rheometer.
At any given time during the experiment, the viscosity is calculated using the simple relationship:
viscosity = shear stress/shear rate
Materials that have structure can absorb the applied stress until the structure starts to break down. This manifests itself in an increase in the viscosity as the structure is maintained, followed by a rapid decrease in the viscosity as the structure collapses.
The stress at which this collapse occurs is the so-called yield stress. The higher yield stress of sample A suggests that this ink would be more difficult to pump or dispense than sample B, and would be less susceptible to 'dripping' during screen printing, which is one method of printing the magnetic strips.
Stress sweep analysis
Figure 3 shows data produced on samples A and B from a stress sweep analysis.
In this experiment the material is subjected to a sinusoidally variable stress (at a constant frequency) which is systematically increased and the sinusoidal strain response is measured. At low stresses the material will behave in a linear manner, i.e. the strain is proportional to the stress; while at higher stresses the response will be non-linear. The extent of the linear response region gives information on both the microstructure and performance characteristics.
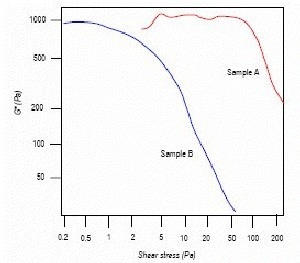
Figure 3. Stress sweep analysis of samples A and B.
The curves in Figure 3 indicate that the magnetic particles in sample A are better dispersed than those in sample B, since a more extensive linear region suggests more interparticle interactions and hence, better dispersibility. Also sample A will be less likely to exhibit sedimentation since it can absorb higher stresses without losing its structure.
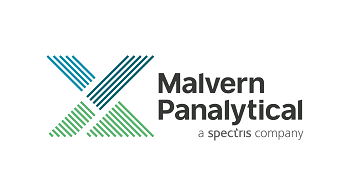
This information has been sourced, reviewed and adapted from materials provided by Malvern Panalytical.
For more information on this source, please visit Malvern Panalytical.