The basic steps in the manufacture of sialon ceramics (and many other advanced ceramics such as alumina, zirconia and sintered silicon carbide) can be split into 3 main stages and an optional fourth stage, as shown in the flow diagram below:
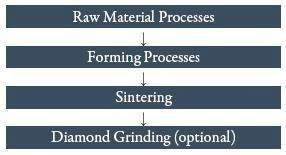
Each of these stages in the manufacturing process influences the properties of the final product.
High Purity Raw Materials
The raw materials for manufacturing sialon ceramics come in powder form. The powders used by International Syalons are of the highest quality, both in terms of purity and particle size. Particle sizes are usually sub-micron. This helps ensure the best sialon ceramics available.
Processing of Raw Materials
Prior to forming, three or more of these powders need to be mixed together to form the stock material used in the forming processes. At International Syalons this is usually one of 3 types:
- Spray dried powder
- Aqueous slip
- Granulated feedstock
Feedstocks Produced by Spray Drying
Spray drying is a method of producing a free flowing, uniform powder, which is the ideal feedstock for a variety of pressing processes such as uniaxial pressing and wet and dry bag isostatic pressing. This powder can contain up to 5% organic binders, including lubricants and binders to give good green strength.
Aqueous Slip Feedstocks
Aqueous slip is prepared by milling together the raw materials in water along with an organic dispersant to produce a fluid, highly concentrated slurry, which is used for slip and pressure casting to produce a high green density part.
Granulated Feedstocks with Organic Binders
Granulated feedstock is prepared by mixing the powders with a blend of organic binders to produce a plastic like material that is deformable under pressure, for example by extrusion.
Quality of Raw Material Feedstocks
The quality of these raw material feedstocks becomes critical in the next stage of manufacture, the forming process. The better the feedstock, the better the green density achieved during consolidation and consequently lower the sintering shrinkage in the final process stage.
Forming Processes
The forming process involves a consolidation stage and an optional machining stage, as shown in the flow diagram below:
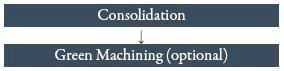
Consolidation Techniques Used by International Syalons
Consolidation aims to produce a near net shape part with sufficient strength for subsequent handling (and green machining where required). Consolidation techniques used by International Syalons include:
- Uniaxial pressing
- Isostatic pressing
- Slip casting
- Extrusion
Uniaxial Pressing
Uniaxial or die pressing is a medium to high volume consolidation method for simple (for example discs or plates) to relatively complex parts (for example parts with holes or recesses) and involves the uniaxial compaction of a spray dried powder in a die.
Components made by uniaxial pressing do not usually have any green machining stage and where possible are made to as-sintered tolerances.
Wet Bag and Dry Bag Isostatic Pressing
Isostatic pressing is a small to medium volume technique of which there are two variations: wet bag pressing and dry bag pressing. In both cases, a spray dried powder is contained in a flexible (usually rubber or polyurethane) bag which is subjected to an isostatic pressure.
Wet bag pressing is primarily for simple stock shapes, such as rods or billets, which are subsequently green machined to the required shape, whereas dry bag pressing can produce more complex shapes, such as nozzles, which are generally not green machined.
Slip Casting
Slip casting, also known as drain casting, is a small to medium volume consolidation method for generally simple shapes, such as tubes or crucibles, but also for more complex shapes such as ladles.
Slip casting uses a highly fluid, concentrated aqueous based slip which is poured into a porous mould (usually made from plaster). The water is drawn from the slip into the plaster by capillary action which leaves the sialon powder mix deposited on the inside of the mould. Over time, the thickness of the cast increases. When the required thickness is achieved the remaining slip is drained from the mould.
In pressure casting, a variation on slip casting, a pressure is applied to the slip. This method can be used for solid shapes such as large plates or rods or for tubes with a large wall thickness.
Extrusion
Extrusion is a medium to high volume consolidation technique for producing simple shapes such as small diameter tubes. The granulated feedstock deforms under pressure and the binders in the mix help retain the extruded form as it dries.
Green Machining
Green machining is the machining of an un-fired, ‘green’ or raw body. This need to be done when the consolidation method used cannot produce the required part. For example, the best way to make a part like a weld location pin is to green machine an isostatically pressed rod.
At International Syalons we use standard and CNC lathes and milling machines. Depending on the part, as much of the machining as possible is done in the green state. Not only is green machining quick, it is also much cheaper than diamond grinding and the dust from the machining process can be collected and recycled.
The Sintering Process
Sintering is the process during which the consolidated green sialon part is fired to give a dense, advanced technical ceramic. For sialons, this occurs at around 1750°C and the sintering process is known as liquid phase sintering.
Liquid Phase Sintering
Liquid phase sintering is a type of sintering process in which a part of the powder blend melts to produce a viscous glassy liquid. In the case of sialons, the oxides in the formulation, yttrium oxide, silica and alumina, melt to produce a glassy yttrium-silicon-oxynitride liquid.
During the liquid phase sintering of sialons, firstly the particles rearrange due to capillary forces, giving better packing. Then at the points of contact between particles some of the solid particles begin to dissolve in the liquid and are re-precipitated at the neck areas between the particles.
The Syalons developed by International Syalons have been optimised such that just the right amount of liquid is formed during sintering to aid densification without there being too little or too much, which would have a negative impact on the materials mechanical properties.
Typically, Syalons shrink approximately 20% on sintering, hence the importance of obtaining a good green density during consolidation.
Diamond Grinding Sintered Components
Diamond grinding is a machining process which is carried out on a sintered part that needs to be tightly toleranced, needs an improved surface finish or to remove surface flaws and as such is an optional process.
Finishing – Final Machining
Final machining processes include grinding, cutting, honing and lapping and polishing. Each of these processes requires diamond tooling due to the high hardness of sialons. Also, the rate of material removal is very slow as care must be taken not to cause surface damage. These are therefore relatively expensive processes and so best efforts are always made to minimise the need to diamond grind by, where possible, working to as-sintered tolerances.
|