Many exterior components on modern automobiles are fabricated from advanced polymer and composite materials. Knowledge of the strength and durability of these raw materials is becoming increasingly important for suppliers who support the automotive industry. These materials must have the appropriate strength and durability. Additionally, the finished components must resist environmental extremes and be able to sustain significant deformation in service. As a result, many automotive manufacturers are seeking consistent material properties data.
.jpg)
Fatigue Testing on Polymer Materials
A manufacturer of polymer materials contacted Bose with the need to assess fatigue response and also to perform a DMA assessment on their raw materials. The ElectroForce® 3330 test instrument with DMA (Dynamic Mechanical Analysis) software, in conjunction with WinTest® control software, was used to conduct these tests. The ElectroForce 3330 test instrument is a table-top system that is uniquely designed for testing small and medium size samples. The ElectroForce 3330 has excellent control resolution at lower forces and loading capacity up to 3 kN.
Fatigue Testing Properties and Optimization
The manufacturer supplied two specimen configurations of the matrix polymer for testing. The testing was performed using Bose® 3 kN tension grips. The 3330 test system was configured with the standard 25 mm displacement transducer and 3 kN force transducer.
The initial testing performed was force controlled fatigue testing from 15 N to 145 N using a 5 Hz sinusoidal waveform. Typical single test resultant data is plotted below. The accumulation of plastic strain is evident over the course of the test up to failure at 2700 cycles. This type of testing is simple and easily accomplished with the 3330 table-top instrument and standard WinTest software.
.jpg)
Multiple tests and multiple applied stress levels were conducted to generate a traditional S-N curve for the material.
.jpg)
Dynamic Mechanical Analysis (DMA) Testing
The second round of tests were performed on the second sample geometry. These tests were typical DMA tests which consisted of a frequency sweep from 0.1 to 10 Hz using the force control capability in the DMA software. A 15 N pull contact force was applied to the specimen to ensure all the samples were subjected to the same loading history. The force applied on the matrix polymer was a mean force of 100 N and dynamic amplitude of 60 N. Upon completion of the test data acquisition, the DMA software calculated the modulus and tan delta for the specimen and exported the data for plotting as a function of frequency. The plotted data agreed with the expected material modulus and tan delta behavior.
.jpg)
Applications of Bose ElectroForce System
The Bose ElectroForce system is well-suited to applications where there is a need to apply low forces but still have capacity to perform tests up to several kiloNewtons.
.jpg)
Summary on Fatigue Testing of Automotive Polymers
This series of tests demonstrates the capabilities of the Bose ElectroForce 3330 test instrument to characterize the material properties of raw materials for automotive industry applications. The material properties of the matrix polymer agreed very well with properties measured by other industry standard testing protocols where there was overlap with test conditions. The instrument also is well-suited for testing components of products made of the same raw material. The 3330 test system is able to provide an expanded range of test performance in an easy to use, versatile instrument.
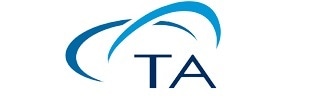
This information has been sourced, reviewed and adapted from materials provided by TA Instruments.
For more information on this source, please visit TA Instruments.