Materials testing is an important part of product development and quality testing for a host of different products in a diverse range of industries, including aerospace, automotive, food, beverage, medical, pharmaceutical, power, oil, and gas.
.jpg)
While testing of a component or a section of a product is frequently adequate, it may be necessary to test the complete product. This can create difficulties if the product is large. However, Lloyd Instruments, manufacturer of the ‘Plus’ series of material testing machines have a number of solutions to address this challenge.
Even standard machines can readily accommodate large samples (Figure 1). Maximum crosshead travel ranges from 500 mm for the single column benchtop LFPlus instrument to 1295 mm for the twin column LR300K floor standing machine. Extended versions of the instruments are also available and for extra-large samples, such as complete car seats for children, compression cages are available.
A special ‘pogo’ version of the instruments gives added versatility and this is illustrated through a case study, with the testing of three-dimensional nailing plates at CERAM Building Technology.
‘Extended’ Instruments
Extended column versions of the ‘Plus’ range of material testing instruments offer increased crosshead travel (Figure 2) and are available for testing larger or non-standard shaped samples and for high elongation, ductile materials such as plastics or rubber or longer than normal test specimens.
Extended crosshead travel ranges from 750 mm for the single column 1kN LFPlus materials testing machine up to 1620 mm for the twin column LR100KPlus and LR150KPlus machines with 100kN and 150kN capacities respectively.
.jpg)
In addition, the LFPlus machine can accommodate large samples or fixtures due to a deep throat measuring 175 mm and by fitting an expanded work table to the instrument.
Extended work tables are supplied with a matrix of metric or imperial threaded holes for ease of mounting of samples and fixtures. An optional T-slot table allows unusually shaped samples to be clamped to the base or customized grips and fixtures to be fitted.
Compression Cages
Lloyd Instruments offers a range of compression cages for its universal testing machines, designed for very large or bulky sample testing. These rugged assemblies allow a full range of compression tests to be carried out on samples wider than 400 mm.
Applications include testing of components as diverse as complete car seats (Figure 3), items of furniture, mattresses, large cardboard cartons, crates, complete assemblies and large diameter pipes.
.jpg)
The frames are constructed from aluminium and built to individual customer specifications. One of the largest sized frames supplied to date has dimensions of 1.6m x 1m x 1.3m.
The sides of the cages can be open or shielded with wire mesh or polycarbonate panels. Compression platens can be integrated into the frame and mounted on guide bearings to ensure alignment. Since the addition of a compression cage can significantly raise the height of the instrument itself, the machine's control console and emergency stop switch are mounted on the cage for easy access.
Although generally dedicated to large sample testing applications, the instruments can be returned to a normal configuration by removing the through rod, platen and lower bearing and replacing the anchor pin. Lloyd Instruments produces a range of ‘Pogo’ machine configurations that can accommodate these specially designed cages.
Cages can be supplied to fit below any of the company's pogo machine versions, which include: LFPlus (1kN) and LRXPlus (5kN) Series of single column instruments and the LR5KPlus (5kN), LR10KPlus (10kN), LR30KPlus (30kN), LR50KPlus (50kN), EZ20 (20kN) and EZ50 (50kN) Series of twin column machines.
Case Study – Testing of Three Dimensional Nailing Plates
Three-dimensional metal nailing plates are used to join load-bearing timber structures and also for fixing timber structures or wood-based structural members to their supports. These plates are generally available in a range of shapes and sizes and are secured to the structures using a range of nails, screws, bolts or dowels.
A typical example is shown in Figure 4. The plates must be capable of withstanding the loadings placed upon them during use and therefore should be tested to ensure that they are fit for their purpose. This requires testing of large components and poses significant practical challenges.
Testing includes mechanical resistance and stability and is carried out according to the requirements of ETAG 015, ‘Guideline for European Technical Approval of Three-Dimensional Nailing Plates’, published by the European Organisation for Technical Approvals in September 2002.
A leading manufacturer of three-dimensional nailing plates has commissioned CERAM Building Technology, to test their products according to ETAG 015. CERAM Building Technology has many years of experience working with clients in the materials industries and has a fully independent UKAS ISO 17025:2005 accredited laboratory.
.jpg)
Sample Preparation
Prior to testing, the timber is conditioned in accordance with ISO 554:1976. Timber conditioning takes place in a controlled temperature and humidity chamber corresponding to 20±2ºC and 85±5 % relative humidity.
The timber is classed as conditioned to an equilibrium moisture content when two successive weighings, taken on a calibrated balance, do not differ by more than 0.5% of the mass of the test sample when taken 6 hours apart.
The samples are constructed in the controlled environment before transferring to a second controlled temperature and humidity chamber corresponding to 20±2ºC and 65± 5% relative humidity. The samples are again classed as conditioned to an equilibrium moisture content when two successive weighings taken on a calibrated balance do not differ by 0.5% of the mass of the test sample when taken 6 hours apart.
Test Procedure
Material testing is carried out using an LS100Plus twin column materials tester from Lloyd Instruments. In view of the large size of the components to be tested, the LS100Plus is mounted on a specially designed frame in a “pogo” arrangement (Figure 5).
The top compression plate is mounted inside the frame under the machine. A vertical rod is fitted to the bottom of the load cell and this runs through a linear bearing in the lower crosshead and connects to the compression platens mounted below the machine.
This allows the compressive force to be applied to the sample under test. The timber samples are placed in a purpose-built test rig. They are tested within 24 hours of removal from the conditioning chamber. The timber joist is propped such that it is supported on a roller bearer. Calibrated linear voltage displacement transducers are placed on the top of the timber support and on the underside of the timber connector at the center of the timber connector.
The load is applied in accordance with BS EN 26891:1991 ISO 6891:1983 and is applied to the hanger at 1/3 length of the timber joist via a hydraulic ram acting on a load spreader plate to ensure that there is no localised crushing of the timber joist under load. The load is applied in a prescribed manner until either the estimated failure load for the hanger is reached or a 15 mm deflection is measured (as the difference between the two transducer measurements). Hangers are measured in batches of five.
.jpg)
Summary
A variety of options are available to allow materials testing of large components in a wide variety of industries. The example given here illustrates the versatility of the ‘pogo’ arrangement.
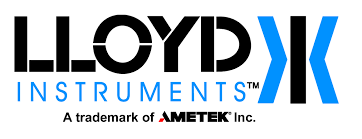
This information has been sourced, reviewed and adapted from materials provided by Lloyd Instruments Ltd.
For more information on this source, please visit Lloyd Instruments Ltd.