In an effort to become more competitive, to increase profitability and improve quality, and to meet or exceed a customer’s schedule, companies are turning to automated processes that are based on increasing production throughput and profitability, while improving quality and work consistency.
Despite the significant initial costs associated with the integration of new technology into existing operations and the modernization of facilities, the long-term benefits of automation include profit increases, shortening lead times, and improving quality and customer satisfaction.
Industries Suitable for Implementing Automated Specimen Handling Systems
Materials testing laboratories across all industries, including metals, plastics, elastomers, biomedical, paper, textiles and films, also have the opportunity to automate many of their R&D and Quality Control (QC) testing processes to provide increased throughput and better financial performance of the business. There is a need for testing laboratory managers to reduce overall operating costs, yet still meet the demands of higher testing volumes, timeliness of results, improved reliability and reproducibility of data, and ensured operator safety. Automated materials testing systems are a viable solution that satisfies all of these requirements.
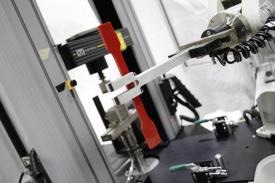
Return on Investment (ROI) Analysis of Implementing Automated Specimen Handling Systems
Automated specimen handling systems designed for mechanical testing of materials or components in any environment, whether it is R&D or QC, can be quite expensive. In order to justify the purchase of such equipment, you must have a good understanding of the true value that can be obtained from this equipment; especially in today’s economy. As the economy continues to spiral downward, companies in all industries are beginning to focus their efforts on running leaner in effort to remain competitive and to maximize profits.
Running leaner does not necessarily mean reducing head count or minimizing production. Companies are investing resources into their operations such as automated specimen handling system when the benefits out weigh the cost. Large equipment purchases need to be carefully planned and most often, a return on investment (ROI) analysis needs to be carried out. The purpose of this article is to help you understand the benefits and costs associated with automated specimen handling, as well as suggestions on how you may want to evaluate ROI. The equation for ROI is simple and is most often expressed as:
ROI = Benefit / Cost or Value / Cost
Calculating Return on Investment of Implementing Automated Specimen Handling Systems
Calculating ROI is necessary and most often mandatory for the majority of businesses due to a substantial upfront cost. Determining the ROI for an automated specimen handling system can be difficult, as it would be for most large complex pieces of machinery. One of the reasons for this is that the benefits, or the return in value, is not always tangible, and it is often difficult to measure or associate a dollar value to it. Certainly, there are benefits that are simple to measure; these may include a reduction in training expenses, less man power, and less scrap as a result of faster turn-around time in a QC environment.
Costs Associated with Implementing Automated Specimen Handling Systems
In order to properly assess a large purchase, you must understand the true benefits or value obtained from the purchase. You also need to have a good understanding of the costs that are associated with the purchase. There are costs for the actual equipment and installation, as well as costs that relate to maintenance, energy, and training. Mentioned previously was that the cost of training would be less when compared to a manual system, but some level of training would still be required and should be factored into the ROI. An effective approach in evaluating the costs of automating a system is to focus on the additional costs that would not be present in a manual system. If both systems require the same tensile frame, it is not necessary to factor that cost into your analysis. On the other hand, if more (or less) training is required, that cost should be factored into your analysis.
Benefits of of Implementing Automated Specimen Handling Systems
Let’s first look at the benefits, or value, that you can expect after purchasing an automated specimen handling system. The most significant benefit would be an improvement in the consistency and repeatability of data. Technique and precision is critical for obtaining accurate and consistent data and inconsistencies in how specimens are inserted into a grip or fixture will impact results. Gauge R&R studies have suggested that operator error is the most common source of error, when compared to error within a testing system or from the specimen itself. If an operator is conducting high degrees of repetitive testing, it could cause fatigue and boredom, ultimately leading to operator error.
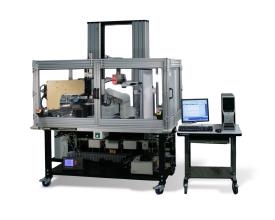
The same is true for dimensional measurement. By manually measuring each specimen, it’s virtually impossible to place the measuring device on the specimen at the same location each time, from specimen to specimen. The same is true for the amount of force that is applied when the measuring device is attached to the specimen. Measuring at different points may result with different cross sectional areas, which impacts stress related calculations. Slight inconsistencies in these processes may have substantial effects on these results. These measurement inconsistencies exist when individual operators conduct the test, but are also likely to occur when testing is conducting between multiple operators.
Quality Control Testing in Automated Specimen Handling Systems
Additional benefits of an automated testing system include more throughput or quicker turn-around time. This is important in QC testing. Test results often determine if a product is within spec or not. Additionally, a product is identified as being out of spec in a quicker time frame if running an automated test, which in turn reduces the amount of out-of-spec product that is scrapped. Manufacturing costs are extremely high so the payback for faster testing, and being able to quickly identify a non-conforming product, is very beneficial.
Time Management in Automated Specimen Handling Systems
There may be cases when throughput will not significantly improve. This can occur when the amount of time it takes for one specimen to test is long enough that an operator can measure and prepare the next specimen during that test time. Although, in this case, the throughput does not improve, automated specimen handling will improve manpower efficiency. If it takes five minutes for the specimen to fail, and it takes two minutes to measure and insert a specimen into the grips, what does the operator do during the remaining three minutes? Three minutes may not sound like a lot of time, but think about high volumes of testing, multiple shifts, etc … it all adds up rather fast. An example of this situation is available below.
In real life situations, operators do not function like machines, and the amount of time it takes the operator to measure and insert a specimen will vary greatly. Operators may get distracted, take breaks, or make mistakes that require time to rectify. By utilizing an automated specimen handling system, the throughput will no longer be operator dependent, while the consistency of your test results will improve, and your operator can now be available to work on more challenging projects.
Occupational Hazards with Implementing Automated Specimen Handling Systems
One last benefit of using an automated testing system relates to injury costs. Injuries, and the costs associated with medical bills, will decrease as the operator’s level of repetitive movement and physical interaction with the equipment is minimized. These benefits add value that should also be factored into the ROI.
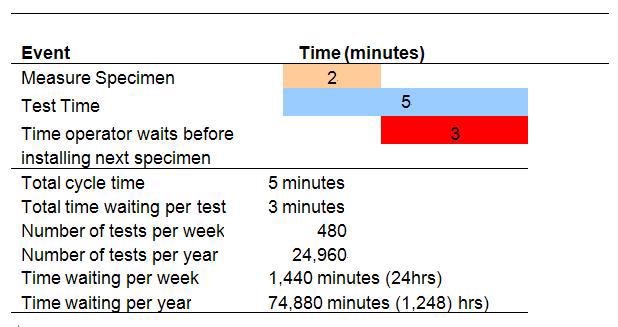
Figure 1. An example of how down time adds up quickly
Summary
This rough time line indicates that for every week an operator tests manually, he or she waits 24 hours for specimens to be tested before he or she is ready to install the next specimen. This is assuming that testing is conducted non-stop, 40 hours per week. This is typical for an automated specimen handling system.
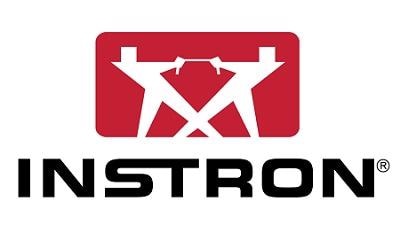
This information has been sourced, reviewed and adapted from materials provided by Instron.
For more information on this source, please visit Instron