Developments in materials technology depend to some extent on the importance of the intrinsic value of each, and the proportion of total cost, which is accounted for by raw materials. At the two extremes are the traditional inorganic materials glass and metals. While only about 25% of a glass container’s cost is for its raw material content, for metals the proportion is 70-80%. For the organically derived materials, paper and plastics, the comparable figure is something like 50%.
Materials reduction is usually achieved through work on the geometry of the pack, the mechanical properties of the material, and the forming technology. The elements of this triple-pronged attack are used to different degrees in individual situations.
Paper and Natural Fibres
In the case of paper and board, there is limited scope for improving pack geometry, and only a little more for improving materials processing and pack constructional detail. Improvement in material performance provides the principal opportunity to reduce costs.
As paper is produced from natural fibres, its mechanical properties depend upon their individual strength, their length, orientation and the degree of inter-fibre bonding which can be achieved. Flow patterns in the lay-down of separate fibre layers are one aspect which can be improved by mechanical and electrostatic techniques.
Current concerns with the chlorine content of paper mill effluents has focused much attention on the use of natural (i.e. unbleached) kraft pulp for packaging paper. This is inherently stronger than bleached grades, and allows some worthwhile down-gauging to be achieved.
Glass Packaging
Chemical means can be used to improve the fundamental properties of glass. A development by Yamamura Glass in Japan involves the substitution of sodium ions by potassium ions in the surface layer to produce a tough stressed skin.
Recently the Moscow Glass Research Institute announced a new grade of glass with a strength of 200 MNm-2, over twice the usually accepted level. So far, due to the uncertain nature of the market, and the high capital expenditure, none of these have become commercially viable. Developments have, instead, concentrated on processing improvements and surface coatings to allow weight reduction without loss of mechanical strength.
Plastic Packaging
In the plastics sector opportunities continue to be identified in the basic materials, processing developments, and even in container geometry. A better understanding of relationships between molecular structure and physical properties is being combined with improved ability to tailor molecules in the polymerisation process to produce enhanced performance.
Linear low-density polyethylene was the first such material to be commercialised on a large scale, and new ‘super’ polyolefins are becoming available which will ensure that this group, by far the largest sector of all plastics, will maintain its pre-eminence. Polyethylene terephthalate (PET), developed initially as an engineering and textile polymer, found packaging applications relatively recently. In 20 years or so, it has become the industry standard for large containers for carbonated soft drinks due to its light weight, clarity, extreme strength and good gas retention characteristics.
Its low intrinsic viscosity (IV) made it unsuitable for blow moulding, but ideal for the newest technique of injection-stretch blow moulding. Recently new grades with higher IV have become available, and can now be expected to challenge PVC for such applications as bottles for edible oil, wine, and mineral waters.
After years of research, higher temperature-tolerant formulations have appeared, based on a new polymer, polyethylene naphthalate (PEN), which is used in combination with PET. This offers improved strength, UV barrier and gas barrier properties, in addition to being hot-fillable at temperatures from 85 to over 100°C, figure 1.
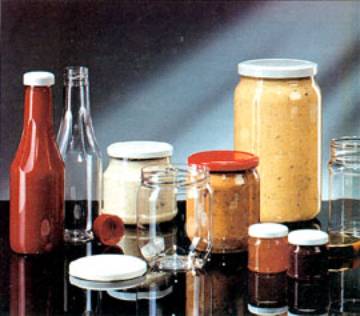
|
Figure 1. PEN/PET hot-fillable polyester bottles and jars.
|
Interest in environmental aspects of packaging has resulted in the wider use of refillable multi-trip containers. For this application polycarbonate, PET and the new PET/PEN grades are the main contenders.
Thin Forms
Thin forms of paper, regenerated cellulose, metal foil and all types of plastics, plus filament reinforcement and a range of coatings or surface treatments to further enhance their performance can be combined in thousands of permutations to meet virtually any performance specification except direct load bearing and extreme levels of physical abuse.
Reclosable Containers
The last piece in the jigsaw - improving the ability to open and reclose - has recently been put into place, as easy-open tear strips and reclosable screw caps have been developed. With these new options have come wider applications, ranging from liquid detergents to emulsion paint, fresh soups to breakfast cereals.
Metal Two-Piece Cans
On the metals front much effort has been put into improving the ductility of the two main competitors, steel and aluminium, to enable deeper drawing of two-piece containers, better materials distribution within them, and more easily produced (and used) easy-open devices for steel.
In Japan and Europe a new concept of producing two-piece cans from thin metal laminated on both sides with PET film, has emerged in recent years. This has been commercialised most widely in Japan under the names of HiRetoflex and TULC, for small trays and beverage cans respectively. A similar material Ferrolite, developed jointly by CarnaudMetalbox and British Steel, is also used in Europe. The best known example is the small white can used by H J Heinz for baby food, with its pigmented layer of PET on the outside.
In addition, there has been a continuous programme of improvement in side welding and end seaming techniques. These include adhesive bonding, mechanical crimping, induction welding and most recently laser welding, which allows a virtually waste-free butt join to be used. A recent development by CarnaudMetalbox is a pneumatic ‘blowing’ technique to produce asymmetrically shaped cans. This competes with mechanical stretching techniques previously used.
The two-piece style of packaging is widely used in the soft drinks sector. This consists of an ultra-thin wall stiffened by the internal carbonation pressure. A similar draw-wall-iron technique has been developed for heavier cans for processed foods, but the main uptake for these has been in pet foods and canned salmon. It is indicative of the multifaceted research efforts of the industry that 20 years ago all projections indicated that the two piece can offered the greatest potential, but today the three piece form is holding its own, and is seen as offering more flexibility in materials selection and its distribution between body, base and end.
|