Hydrogels, which are water-swollen cross-linked polymers, are becoming increasingly important in a wide array of biomedical applications. One of the earliest uses of hydrogels was in the development of soft contact lenses. Currently hydrogels are also being used in areas including cosmetic and reconstructive surgery, drug delivery systems and tissue engineering. It has become increasingly important to determine the material properties of hydrogels, particularly for applications where they are being used as structural components in vivo.
.jpg)
Dynamic Stiffness and Modulus of A Polyvinyl Alcohol Hydrogel
Cambridge Polymer Group, a Boston, MA based contract research laboratory specializing in polymers, contacted Bose® with the challenge of accurately determining the dynamic stiffness and modulus of a polyvinyl alcohol hydrogel. The ElectroForce® 3100 test instrument and DMA (Dynamic Mechanical Analysis) software, in conjunction with the WinTest® control software, were used to determine the specimen stiffness and material properties of the hydrogel. The ElectroForce 3100 test instrument is a tabletop system that is uniquely designed for low force applications that require greater control resolution than is typically available with moderate to high force testing systems.
Testing Procedure
Cambridge Polymer supplied small irregularly-shaped cylindrical samples of the hydrogel for testing. The specimens were approximately 3 to 4 mm in diameter and 3 to 4 mm in height. Testing was performed in compression with platens 12.7 mm (0.5 in) in diameter, a 5 mm (0.2 in) displacement transducer and a 250 gram (2.45 N) force transducer mounted on an ElectroForce 3200 test instrument.
Compression Testing Results
The initial test performed was a displacement ramp from contact to 430 mN at a rate of 0.02 mm/s (0.0008 in/s). The resultant data was plotted on a force-displacement curve to determine the linear region of the material (Figure 1). A distinct linear region was not observed as the specimen made a very gradual change in stiffness as a function of % strain.
.jpg)
Figure 1. Hydrogel Force Vs. Displacement
The second test performed was a frequency sweep from 1 to 100 Hz for a variety of strains, from 4% to 14% compression, using the DMA software. A 0.001 N compressive contact force was applied to the specimento ensure that the data collected was repeatable. This also ensured that the upper compression platen did not lose contact with the hydrogel sample. Upon completion of data acquisition, the DMA software calculates the modulus and tan delta for the specimen and exports the data for plotting as a function of frequency at the various levels of strain. The plotted data agrees with the expected material modulus and tan delta; however, there appears to be a specimen resonance or other abnormality as other specimens do not show this behavior between 20 and 100 Hz (Figure 2).
.jpg)
Figure 2. Hydrogel DMA
The 3100 system is well-suited to very low force applications as is demonstrated in Fig. 3. The plot presents data taken at a frequency of 1 Hz and a mean strain of 4%. Fig. 3 shows that peak-to-peak loading on the hydrogel was approximately 2 mN with a corresponding peak-to-peak displacement of 28 ìm.
.jpg)
Figure 3. Sample Data at 1 Hz and 4% mean strain
Summary
This series of tests demonstrates the capabilities of the ElectroForce 3100 test instrument to characterize the material properties of very soft viscoelastic materials such as hydrogels. The material properties of the hydrogel agreed very well with properties measured by other industry standard testing protocols where there was overlap with test conditions. The 3100 test instrument is able to provide an expanded range of test conditions in an easy to use, versatile product.
.jpg)
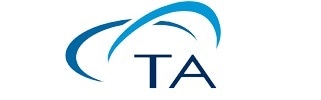
This information has been sourced, reviewed and adapted from materials provided by TA Instruments.
For more information on this source, please visit TA Instruments.