Hydrogenated nitrile rubber (HNBR) has an intriguing combination of properties. Like other elastomers, the material has high tensile strength, low permanent set, very good abrasion resistance and high elasticity. But in HNBR, these are complemented by good stability towards thermal ageing and better properties at low temperatures compared to other heat- and oil-resistant elastomers. This combination of properties is opening up a broad range of applications for the materials, mainly in the automotive industry. HNBR is replacing polychloroprene in timing belts for cars, figure 1, thanks to its good static and dynamic properties at operation temperatures and good retention of properties under continuous heat exposure. In addition, new grades of material with improved low temperature flexibility are extending the HNBR service temperature range, allowing new applications in seals and mounts, for example. HNBR is also proving useful in the seals and mouldings of car engines that run on new fuels such as rapeseed oil methyl ester. 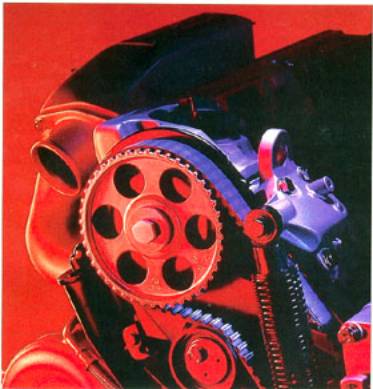 | Figure 1. A HNBR timing belt. | There are several other key properties of HNBR that make it useful in automotive applications. These include good viscoelastic properties in HNBR vulcanisates, a wide service temperature range from -40°C to +150°C, resistance to fluids of various chemical compositions and excellent resistance to strongly alkaline and aggressive fluids. What is HNBR? The material itself is a derivative of nitrile rubber, which is hydrogenated in solution using precious metal catalysts. The nitrile groups are unaffected during the process, but the carbon-carbon double bonds in nitrile rubber are converted into more stable single bonds. Different grades can be made by precise control of the proportion of unconverted double bonds in the material - 10% is considered to be an upper limit, but grades containing 4-8% (partially hydrogenated) or virtually no double bonds (fully hydrogenated) are used in most cases. Partially hydrogenated materials can be cross-linked using both sulphur and peroxide cure systems, and the fully hydrogenated grades can be cross-linked with peroxides. This further expands the range of grades and opens up more applications for these HNBR materials. The Market for HNBR Although HNBR is available in a wide range of grades for a range of applications, it is a speciality engineering elastomer and so its market volume is relatively small. The overall consumption of synthetic rubber in technical rubber goods in Western Europe is about 1.5 million tonnes, compared to HNBR consumption of 1,750 tonnes in 1995. However, in-house studies at Bayer show that things are growing rapidly, and the market volume by the year 2000 could well be more than 3000 tonnes. Applications Timing Belts Belts, seals and hoses are among the most important applications of HNBR, and the automotive industry is the most powerful driving force in the further expansion of these materials’ use. Automotive belts - mainly timing belts - currently account for more than 50% of HNBR use in Europe. HNBR materials allow manufacturers to produce belts with a lifetime of more than 100,000km, and could help stretch this to as much as 200,OOOkm. By 2000, it is believed that the vast majority of timing belts will be made from HNBR rather than traditional chloroprene. Seals Seal applications include air conditioner O-rings, shock absorber seals, power steering seals, water pump seals and in-tank seals. HNBR is particularly popular for these applications because of the materials’ resistance to fluids in general and specifically to aggressive fluids, plus their wide service temperature properties, including: • a high standard of dynamic and mechanical properties, to ensure long term operation • resistance to theremo-oxidative ageing, to withstand high under-bonnet temperatures • safety, serviceability and environmental acceptability • good cost/performance ratio. Thanks to advances in HNBR materials, these can all be achieved. Properties Mechanical Properties The mechanical properties of vulcanisates based on HNBR are extremely good. They generally have high tensile strength at room temperature and also at service temperatures of 100-140°C. In addition, suitably compounded HNBR vulcanisates are at least as resistant to crack growth as the vulcanisates based on conventional CR elastomers. Thermo-Oxidative Properties HNBR is commonly called the ‘150 degree elastomer’ owing to its resistance to theremo-oxidative ageing. A vulcanisate crosslinked in a standard manner with peroxides can achieve a service life corresponding to a long-term exposure of 1000 hours at 150°C. Sulphur-crosslinked vulcanisates can achieve 1000 hours at 130°C. These values are much higher than for CR, and so HNBR is more suitable for withstanding the relatively high temperatures in the engine compartment, which can reach 135-140°C in the timing belt area. Cost Benefits of HNBR Such performance improvements have to be paid for, and in terms of actual materials, HNBR is more expensive than conventional polychloroprene. With regard to the polymer content in a timing belt, it is assumed that direct replacement of CR with HNBR in a timing belt increases costs an estimated 5.7 times, and even tailoring the belt material for HNBR (e.g. accounting for the difference in specific gravities) and formulating with an elastomer content of about 55% gives a cost increase of around 4.2 times. However, other factors swing the equation in the favour of HNBR. For example, the relative cost of the non-elastomer materials to the elastomer content in the timing belt is reduced when CR is replaced by HNBR. So, the finished belt based on HNBR will cost only 2 to 3 times that of a CR belt. In addition, thanks to the enhanced properties of HNBR, the service life of belts at 110°C can be increased by a factor of 5.5 when standard CR is replaced by HNBR and by a factor of 2.3 in comparison with an optimised CR formulation. The advantage of using HNBR is even more marked at higher temperatures. At 130°C the service life of HNBR is about 12 times that of even the improved CR grade. HNBR also brings greater safety. If a timing belt breaks in certain types of car engine, valve control can fail and cause engine locking. So the belt must he made of strong, reliable materials. HNBR belts give a longer service life. Belts are normally replaced in car engines before there are any signs of defects, and using HNBR belts should contribute to the general objective of extending the interval between replacements from 100,000km to 150,000km. Industry Demands New grades of HNBR materials are being produced to give an extended service temperature range, as the automotive industry is making ever-stricter demands to improve reliability and performance. Specifications frequently include properties that are very difficult to optimise simultaneously, such as excellent heat ageing stability, good oil resistance and good low temperature flexibility Typically, oil-resistant elastomers have relatively poor low temperature flexibility, and normal HNBR vulcanisates are no different, having a glass transition temperature of -30°C or above. This means that the materials are often unsuitable for static seals and sometimes also dynamic seals. Bayer has managed to lower the glass transition temperature in some of its HNBR materials, sold under the Therban name, by as much as 10°C through structural modifications to the main polymer chain. HNBR grades with these properties have been on the market for some time now. As far as the he ageing stability is concerned, the improved grade Therban XN535C is comparable with standard grades, as it has a similar double bond content. However, it differs in its stress/strain characteristic. With a comparable vulcanisate composition, the modulus is lower at equal strain. The improvement in compression set is drastic. With conventional HNBR the values at -10°C are very high, but with Therban XN535C the values of around 30% are still acceptable for many purposes. The new grade al exhibits good oil resistance, comparable with NBR. Challenges from New Fuels Clearly, HNBR grades with a reduced glass transition temperature are suitable materials for being used in motor vehicles under the extreme climatic conditions experienced in Northern Europe, Asia and North America. At the same time, they can withstand the high operating temperatures required for economic running of an engine. The engine environment and the climate conditions are not the only challenges being faced by HNBR materials in the automotive industry. In recent years, rapeseed oil methyl ester (RME) has been introduced on to the fuel market as a supplement or alternative to diesel-powered vehicles. This fuel is a more aggressive substance in terms of corrosion, and so the fuel filters and other parts must be changed more frequently. RME also tends to leak into the lubricating oils more than traditional fuels. Of all the elastomers available for use in seals and gaskets to withstand RME, only HNBR exhibits all the necessary properties while being cheap enough. It has good resistance to RME, has the desired mechanical properties and does not decompose at elevated temperatures. Vehicle manufacturers are already realising the benefits of using HNBR and the elastomer has been approved for use in peripheral parts of diesel / RME engines, such as tanks and piping. The Future Further improvements in the properties of HNBR grades will provide even more scope for the use of these materials in the automotive and other industries. Car timing belts are just one example of an application in which the materials’ excellent properties have led to their selection over established materials. Many more such examples can be expected in the future. |