The Potters’ Thumb is about to become obsolete. Potters will no longer have to rely on having years of experience of pressing their thumbs into extruded ceramic clays to judge the suitability of the material for subsequent processing. Instead, a newly‑developed test method is now available for making standardised assessments of the stiffness of clays. Such a test has been in demand by the ceramic extrusion industry, and in particular the tableware sector, for many years. The industry has long wanted to replace the Potters Thumb technique with a more reliable yet just as simple method of assessing the plastic properties of extruded clay. Experienced potters use this technique to assess the stiffness of clay by pressing their thumbs into the clay pugroll, to check its suitability for processing. CERAM Research, with support from the Department for Trade and Industry, has developed the new test method to meet the needs of this sector of the industry (figure 1). It is an indicative test that will help users to set process control limits that are specific to their materials. 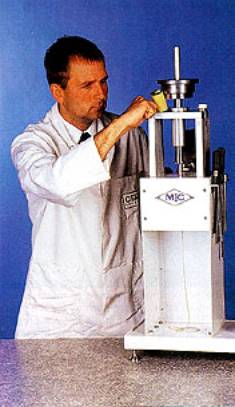 | Figure 1. The MFI ceramic rheology tester. | Principle of the System The test uses a piece of apparatus known as the Martin Flow Instrument (MFI). The MFI is a modified version of the melt flow indexer, which is a recognised test method for measuring the flow properties of plastics and polymers. The principles of how both instruments work are similar, although the Martin flow instrument has been specifically developed to test the plastic flow properties of extruded clays. The Martin flow instrument has two main differences compared to the melt flow indexer: • structural modifications have been made to the dead weight loading system to minimise the effects of friction during test • heater bands have been removed, as there is no need to melt the test sample. Testing Process The process for testing a sample of material is very simple. A sample of the material is inserted into a cylindrical barrel inside the instrument, which contains a die at the base. A piston is then placed in the barrel and pressure is applied to the sample using a dead weight load. The sample material is extruded through the die, and the time taken for a set volume of material to flow through the die is measured with the aid of an electronic timer that contains an infrared sensor unit. The flow time varies according to the stiffness of the material, with stiffer materials will take longer to flow through the die. The test method has been carefully designed to minimise the effects of key factors such as sampling and operator dependency. For example, a coring device is used to extract the sample from the material, and a standard length of sample is inserted into the test barrel without the need to handle it. Advantages of the Systems This simplified rheology test not only meets the requirement of industry but also has the added benefit of testing the sample under shear and pressure conditions that are experienced in the actual extrusion and subsequent forming processes. The instrument’s flexibility enables a range of dead weights between 2 kg and 30 kg to be used, allowing an operator to test the sample within a preferred shear rate range. Faster flow time is directly related to higher shear rates. The instrument therefore allows an operator to measuring the flow time of a material at different weight settings, depending on what is relevant to subsequent processing. Range of Materials The Martin flow instrument can test a wide range of extruded materials, from soft earthenware clays to some advanced ceramic materials. The instrument is also capable of testing pastes prior to extrusion. This test provides the industry with a measurement tool that aids process control. Development History The instrument has already proved its’ worth, performing successfully in a number of applications. CERAM developed the technique in an industrial environment and so was able to assess the capability of the MFI as a process control tool. Philip White, Technical Director of Portmeirion Potteries, has already endorsed the technique. Portmeirion helped to pioneer the apparatus through an intensive on‑site programme of work, aimed at developing the test and studying the clay production process. Process Variables The work carried out included a factorial experimental design exercise to study the influence of process variables on the plastic properties of a clay. The Martin flow instrument helped to identify process variables that are the most significant in affecting the plastic properties of the clay. Additional measurements using the more sophisticated capillary rheometer confirmed these results. This work identified moisture content and clay pugroll diameter as the most critical factors affecting the plastic properties of earthenware clay. Results showed an increase in plasticity with an increase in pugroll diameter. Production Losses Another project involved correlating measurements taken with the Martin flow instrument with forming losses in production. Flow time measurements were taken on random batches of clay over a three month trial period. The clay was produced at a range of diameters and moisture contents. By using factorial experimental design software to analyse the results, it was possible to predict the processing conditions required to achieve minimum losses at forming. These conditions involved controlling the clay within specific pugroll diameters and between specific flow times as measured on the MFI. By controlling the clay within these limits, a five-fold reduction in clay losses was predicted. Future Developments CERAM now operates a service providing companies with the opportunity to test materials using the MFI. This service also extends to a more comprehensive approach incorporating factorial experimental design study work that provides a greater knowledge of customers’ processes. CERAM are also considering further project work with the MFI with a view to developing the test for other sectors of the ceramic industry, including clay raw materials, sanitaryware bodies and injection moulded ceramics among others. Summary The apparatus has been successfully operated in a number of industrial environments, with considerable interest being shown both by UK and overseas companies. It seems as though it is a case of ‘thumbs up’ for the Martin flow instrument from the ceramics industry, and no more pressing thumbs down for potters. |