At the heart of a thermal anemometer are two sensors: an air velocity sensor and a temperature compensation sensor. The velocity sensor is heated to an elevated temperature (relative to the surrounding air) by means of control electronics.
The temperature compensation sensor senses the ambient, or surrounding, air temperature and forces the velocity sensor to stay at a constant "overheat" above the ambient.
The sensors form two opposite legs of a Wheatstone bridge (Figure 1). The circuit forces the voltage at points A and B to be equal by means of an operational amplifier. Air flowing past the velocity sensor tends to cool the sensor, thus driving down its resistance.
The operational amplifier responds by immediately delivering more power to the top of the bridge to maintain voltage equilibrium at points A and B. As more air flows past the sensor, more power is required to maintain a balanced bridge. Thus, the power going into the top of the bridge is related to the velocity of the air flowing past the sensor. This is the basic principal of operation for constant temperature thermal anemometers.
.jpg)
Figure 1: Wheatstone Bridge Diagram
Types of Constant Temperature Anemometers
Following are two types of constant temperature anemometers:
- Hot wire anemometer
- Hot film anemometer (IST AG)
Measurement Principles of Constant Temperature Anemometry
Constant Temperature Anemometry (CTA) is used to measure fine structures in turbulent gas and liquid flows. The working principle is based on the cooling effect of a flow on a heated body. The CTA measures velocity at a point and provides continuous velocity time series, which can be processed into amplitude and time-domain statistics. Examples are mean velocity, turbulence intensity, higher order moments, auto-correlations and power spectra.
Features of Constant Temperature Anemometry
Features of Constant Temperature Anemometry include:
- Measures velocities from a few cm/s to supersonic
- High temporal resolution: fluctuations up to several hundred kHz
- High spatial resolution: eddies down to 1 mm or less
- Measures all three velocity components simultaneously
- Provides instantaneous velocity information
Heat Transfer from Cylinders
Convective heat transfer Q from a wire is a function of the velocity U, the wire over-temperature Tw -T0 and the physical properties (k,r,m) of the fluid. The basic relation between Q and U for a wire placed normal to the flow was suggested by L.V. King (1914). In its simplest form it reads:
Q = (TW - TO) AW h = A+BUn; n=0.5ì
Advantages of Constant Temperature Anemometry
The advantages of Constant Temperature Anemometry include:
- Very simple to use, because no individual sensor housing (channel requiered)
- measure in turbulent and laminar flow profiles
- Heater is also the sensor. It measures by itselfs
- Reference sensor is on the same chip
- High flow rates possible
Disadvantages of Constant Temperature Anemometry
The disadvantages of Constant Temperature Anemometry include:
- Flow signal depends on sensor alignment
- There is a thermal coupling between heater and sensor
- Chip contamination possible, no flow direction detectable
- Relatively high heating power necessary
Calorimeter Flow Sensors
FS2 T Flow Modules
FS2 T Flow Module uses the temperature distribution over a heating element with two or more temperature sensors left and right. For accurate measurings a laminar flow is required to keep up the temperature distribution gradient.
.bmp)
.bmp)
.bmp)
MikroflowSens Flow Sensors
MikroflowSens Flow Sensors uses the temperature distribution over 4 heating/sensor elements with serial down / up- stream arrangement. For accurate measurings a laminar flow is required to keep up the temperature distribution gradient.
.bmp)
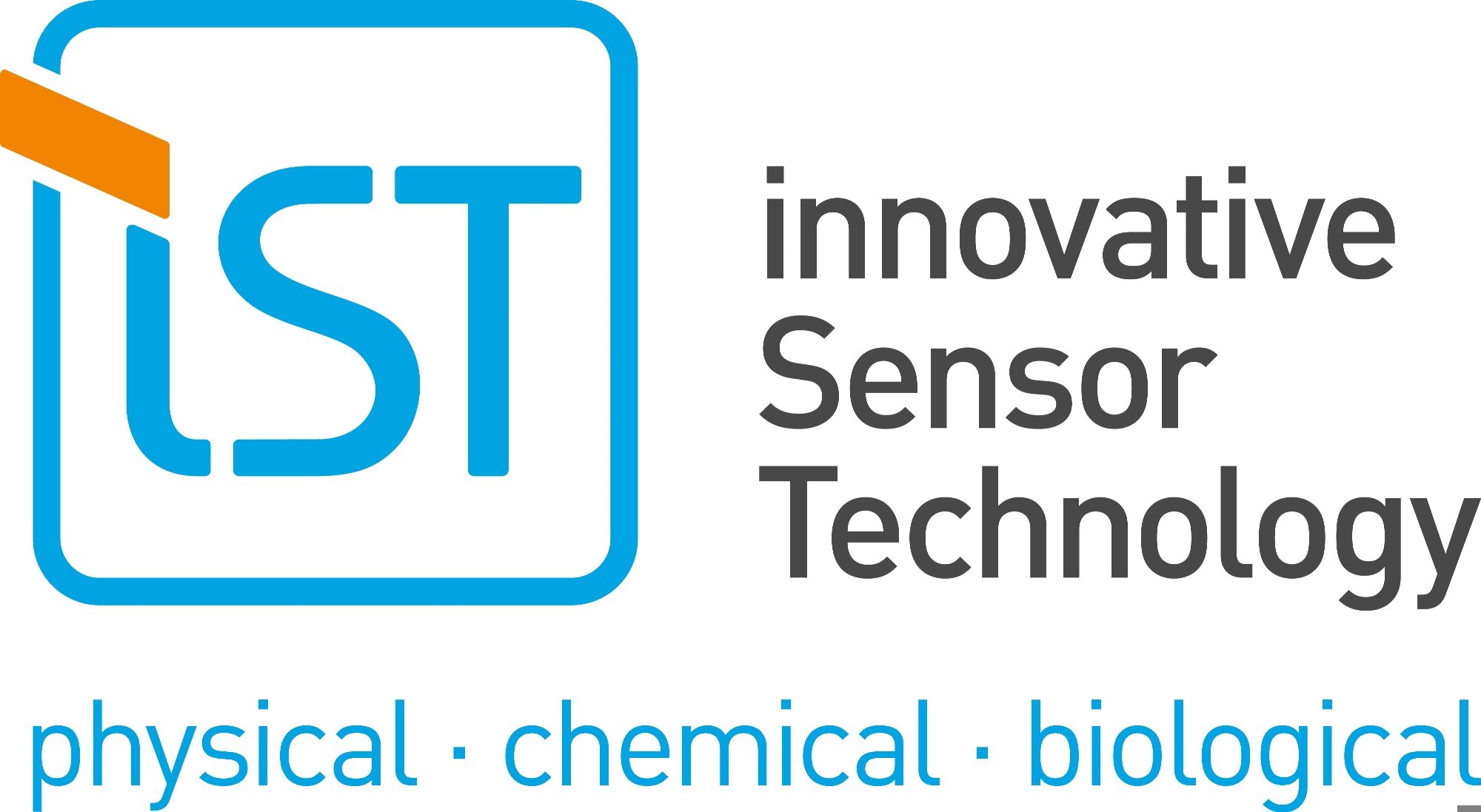
This information has been sourced, reviewed and adapted from materials provided by Innovative Sensor Technology, USA Division.
For more information on this source, please visit Innovative Sensor Technology, USA Division.