The current economic scenario requires manufacturers to be both flexible and accommodating. This applies to both capital equipment suppliers and end users as its imperative that goods reach either their clients or the market place within a fixed time frame.
Challenge Faced by Life Technologies, Paisley
Equipment upgrades are a difficult task for suppliers of consumable goods with a continuous production schedule. A part of the global biotechnology tools company, Life Technologies provides products relating to 21st century forensics, personalized medicine and biofuels to numerous scientists around the world on a daily basis. Their website declares that whether in the university, lab or the field, they expect that the requirements of the scientists will facilitate the scope, quality and speed of research. Since the stakes are really high, there is a sense of urgency in their innovation process with a voracious desire to make new discoveries.
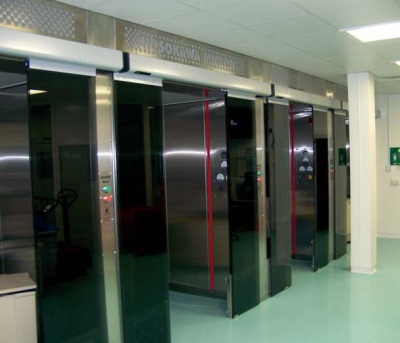
Life Technologies faced a time constraint problem when they needed to upgrade the central dispensary suite of the downflow booths. This particular room is normally used for three shifts, five days a week and sometimes used even during weekends, hence reducing the production schedule could not be afforded.
Suite Makeover Project
It was decided by Life Technologies that a full suite makeover should be organized and completed during the 2009 Easter holidays. They had to find a reliable partner to plan, supply, install and commission the upgraded booths within that time period.
Selection of Hosokawa Micron Ltd
After several enquiries and completion of the selecting procedures, on 26th January Hosokawa Micron was given the project order with all the technical specifications and a time frame of 54 days to begin site installation. The Life Technologies project team led by Elaine Ritchie and the Hosokawa Micron Ltd. Project team arranged for a site meeting and developed a booth design concept. Their task was to replace four worn-out downflow booths with five state-of-the-art containment suites. The quality of the suites had to meet high standards of cGMP.
Constrains and Solutions
The room had certain constraints that required specific solutions. The support columns were situated in odd positions in front of one of the booth doorways. The team decided to place all the 5 off 2m wide recirculation format booths along the wall and install in-fill panels between each booth, such that it gave the look of a continuous stainless steel wall with glass doors. Prevention of cross contamination between the booths was one of the top priorities while designing all this. The Hosokawa team decided on sliding glass doors for each booth and fitted them with touchless sensors to reduce any chance of cross contamination. The suite design had to include IT equipment that would track and log dispensed liquid and powder form materials. The equipment had to be hidden or follow cGMP design, and installed within the rear wall of each booth.
The Hosokawa team delivered the final design concept within the first week of the site meeting. Then the manufacturing phase started, which included purchasing third party items such as fans and motors.
Time-bound Delivery by Hosokawa Micron
The project was closely monitored to prepare for possible delays and routinely updated to all the concerned people. The FAT was planned 45 days from being awarded the project order. The project was on schedule. The Hosokawa installation team worked on stripping and packing the booths for transportation to the site. The unit shutdown day was Thursday evening, when the Life Technologies employees worked through the night to ready the room for the Hosokawa installation team who will be arriving on Friday.
Co-ordination between the teams working with IT, electrical and room finishing was crucial for progress. Commissioning was almost immediately undertaken when a booth was completed. Hence by the sixth day, the last booth was commissioned. The new floor was built and allowed to set after the sliding doors were temporarily removed. The doors were fitted again on Sunday. The booths were finally tested for completion and usability on Monday.
The Final Solution
The production staff of Life Technologies were in for a huge surprise when they came in for their 6 am shift. They walked into a brand new facility fitted with the latest equipment. All this was accomplished within a few days. The successful completion of the project speaks highly about Hosokawa’s commitment to design, project execution and quality. The satisfied client, Life Technologies once again approached Hosokawa Micron for a booth for their quality facility.
.jpg)
This information has been sourced, reviewed and adapted from materials provided by Hosokawa Micron.
For more information on this source, please visit Hosokawa Micron.