Updated by Reginald Davey 08/09/22
Hot working conditions demand metals such as steel which can withstand extreme environments and retain their superior performance and physical properties.
Topics Covered
Introduction
Overview
Properties
Composition
Applications
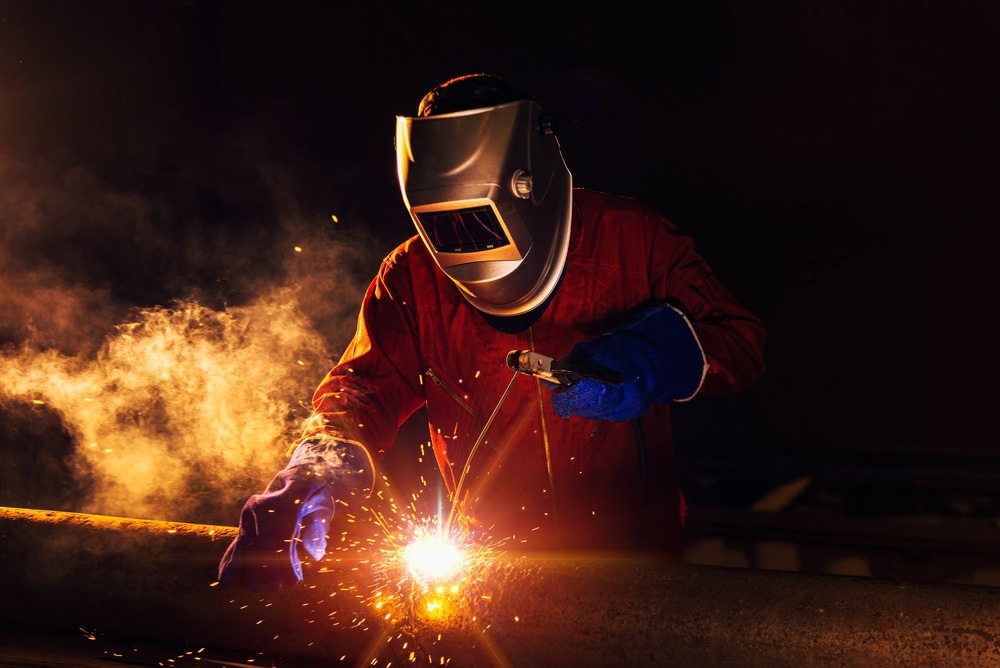
Image Credit: weerasak saeku/Shutterstock.com
Introduction
Hot work tool steels are steels capable of withstanding high abrasion, heat, and pressure conditions that prevail in manufacturing units that perform processes such as forming, shearing, and punching of metals at high temperatures of 480 to 760°C (900 to 1400°F). These steels have wear resistance up to 540°C (1000°F).
Steels used in hot working conditions demand alloying materials which can retain their performance in these environments.
Tungsten has been used to alloy steel for a long time, forming extremely hard carbide and iron tungstite. However, the high tungsten content in these steel alloys makes them extremely brittle, causing them to fracture rather than bend. Compared to some other types of hot working steels, such as chromium steels, tungsten hot work steels are not suitable for applications that use in-service water cooling.
Hot work tool steels are designated as group H steels, and they have 0.35% to 0.45% carbon, 6% to 25% chromium, with vanadium, molybdenum, and tungsten as the other alloying elements. Tungsten is primarily used in hot forming tool steels due to its high-temperature strength, toughness, and resistance to grain growth.
Overview
Tungsten hot-work steels constitute the H21 to H26 types of hot work steels. These steels have similar characteristics to those of other of high-speed steels. The hot work steel type H26 has low carbon content when compared to that of T1 high-speed steel. The primary alloying elements of tungsten hot-work steels include tungsten, carbon, chromium, and vanadium.
Properties
Tungsten hot work steels have high alloy content, which enhances their heat resistance. The high alloy content also makes the tungsten steels brittle and unsuitable for the water-cooling process. Breakage of tungsten hot work steels can be reduced if they are preheated to operating temperatures prior to use. Tungsten steels have normal working hardness of 45 to 55 HRC. Thermal shock resistance and toughness of these steels can be improved by reducing the carbon content. In such cases, it is necessary to adjust the tungsten and vanadium content also as these two reduce the hardenability of steel by trapping large amount of carbon in the form of carbides.
Scaling can be reduced by quenching tungsten hot-work steels in oil or hot salt. Tungsten hot-work steels are resistant to distortion when they are air- hardened, and have higher hardening temperature when compared to chromium hot-work steels.
Composition
The following table shows the composition limits of tungsten hot-work steels.
Designation |
Compositiona, % |
AISI |
UNS |
C |
Mn |
Si |
Cr |
Ni |
Mo |
W |
V |
Co |
H21 |
T20821 |
0.28-0.36 |
0.15-0.40 |
0.15-0.50 |
3.00-3.75 |
0.30 max |
- |
8.50-10.00 |
0.30-0.60 |
- |
H22 |
T20822 |
0.30-0.40 |
0.15-0.40 |
0.15-0.40 |
1.75-3.75 |
0.30 max |
- |
10.00-11.75 |
0.25-0.50 |
- |
H23 |
T20823 |
0.25-0.35 |
0.15-0.40 |
0.15-0.60 |
11.00-12.75 |
0.30 max |
- |
11.00-12.75 |
0.75-1.25 |
- |
H24 |
T20824 |
0.42-0.53 |
0.15-0.40 |
0.15-0.40 |
2.50-3.50 |
0.30 max |
- |
14.00-16.00 |
0.40-0.60 |
- |
H25 |
T20825 |
0.22-0.32 |
0.15-0.40 |
0.15-0.40 |
3.75-4.50 |
0.30 max |
- |
14.00-16.00 |
0.40-0.60 |
- |
H26 |
T20826 |
0.45-0.55b |
0.15-0.40 |
0.15-0.40 |
3.75-4.50 |
0.30 max |
- |
17.25-19.00 |
0.75-1.25 |
- |
aExcept group W, all steels contain 0.03 max S, 0.03 max P and 0.25 max Cu; group W contain 0.025 max S, 0.025 max P, and 0.20 max Cu. As mentioned, amount of sulfur may be increased from 0.06% to 0.15% to enhance the machinability of group A, M, T, H and D steels..
Industrial Applications of Tungsten Hot Work Steels
Tungsten hot work steels find applications in the following areas:
There are some key industrial applications for these steels. Their ability to resist extreme temperatures in hot working conditions make them a key industrial steel in multiple sectors. They are suitable for processes such as drawing, forming, and extruding and produce dies with extremely rugged designs.
High tungsten content significantly improves the operational life of die casting tooling such as sprue bushes, core pins, and spreaders. This superior durability allows longer production runs with reduced maintenance needs. Due to this, there are significant cost benefits when using these metals for this application.
These steels are also used for the manufacturing of extrusion dies and mandrels for extrusion applications. Some metals which can benefit from tungsten hot work steel dies and mandrels include nickel alloys, brass, and steel. They are also used in drop forging and glass and tube manufacturing.
More from AZoM: High-Density Tungsten Alloys for Aerospace Applications
Disclaimer: The views expressed here are those of the author expressed in their private capacity and do not necessarily represent the views of AZoM.com Limited T/A AZoNetwork the owner and operator of this website. This disclaimer forms part of the Terms and conditions of use of this website.