Updated by Reginald Davey 13/01/23
This article will explore tungsten hot work steel, an alloyed tool steel variant used in industrial applications that require steels that can be reliably worked at elevated temperatures.
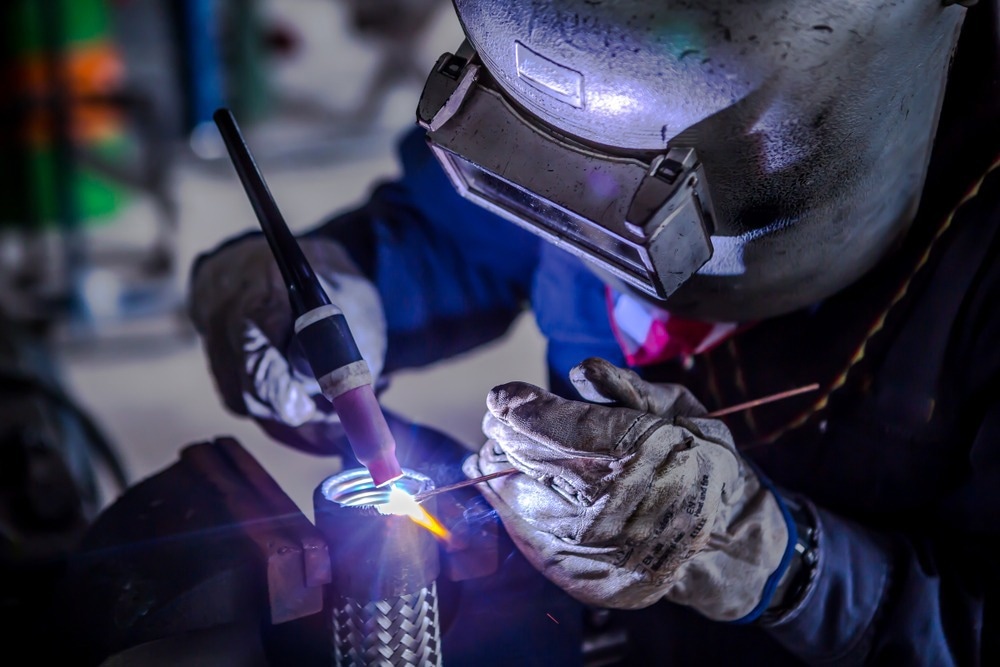
Image Credit: Extarz/Shutterstock.com
Overview
Tungsten has one of the highest melting points of all the metallic elements, with a density close to gold (19.3 g / cm3.) Tungsten is also extremely hard, with tungsten carbide’s hardness close to that of diamond.
Due to its favorable properties, tungsten improves the hardness, strength, and wear resistance of steel, with common steels including tungsten-cobalt magnetic steel and tungsten steel. Tungsten hot work steels are industrially important alloys ideally suited for applications that must withstand high temperatures in the 480-760 oC (900-1,400 oF) range.
Tungsten hot-work steels are of different types, namely, H21 to H26 types. These steels have similar characteristics to that of high-speed steels. The primary alloying elements of tungsten hot-work steels include tungsten, chromium, carbon, and vanadium. The high alloy content enhances the steel’s heat resistance. Scaling can be reduced in these steel alloys by quenching them in hot salt or oil.
Tungsten hot-work steels are resistant to distortion when they are air-hardened and have a higher hardening temperature when compared to that of chromium hot-work steels. Breakage of tungsten hot-work steels can be reduced if they are preheated to operating temperature before use.
Thermal shock resistance and toughness of these steels can be improved by reducing the carbon content. However, to achieve this, the tungsten and vanadium content must also be adjusted as these alloying elements reduce the steel’s hardenability. This is due to too much carbon being trapped in carbides.
Applications
Tungsten hot work steel is used to produce tools including punches, mandrels, and extrusion dies for steel and nickel alloys and brass. They can be used for applications that require significant wear resistance in extreme conditions, being resistant to wear at temperatures up to around 540 oC (1,000 oF.)
In contrast to chromium hot work steels, however, tungsten hot work steels are unsuitable for in-service water cooling due to their high tungsten content.
Tungsten Hot Work Steels Vs Cold Work Steels
Tungsten hot work steels are similar to cold work steels, but the main difference is the temperature they are used at. Cold work steels are used for applications where tools remain at temperatures under 200 oC. Cold work steels are typically high carbon-content alloys.
Common types of cold work steels include oil hardening low-alloy grade steels, air-hardening medium-grade steels, and high-chromium, high-carbon steel grades. Cold work steels are commonly used for applications such as rollers, die casting for plastics, lathe chucks, broaches, roll forming dies, gauges, and blanking dies.
Composition and Properties
The following datasheet will provide details of H23 tungsten hot-work tool steels.
Element |
Content (%) |
C |
0.25-0.35 |
Mn |
0.15-0.40 |
Si |
0.15-0.60 |
Cr |
11.00-12.75 |
Ni |
0.3 |
W |
11.00-12.75 |
V |
0.75-1.25 |
Cu |
0.25 |
P |
0.03 |
S |
0.03 |
Physical Properties
The physical properties of H23 tool steels are outlined in the following table.
Properties |
Conditions |
T (°C) |
Treatment |
Density |
7.7-8.03 x 1000 kg/m3 |
25 |
- |
Mechanical Properties
The mechanical properties of H23 tool steels are tabulated below.
Properties |
Conditions |
T (°C) |
Treatment |
Poisson's ratio |
0.27-0.30 |
25 |
- |
Elastic modulus |
27557-30458 ksi |
25 |
- |
Other Designations
Other designations that are equivalent to AISI H23 tungsten hot-work tool steels include:
- ASTM A681
- UNS T20823
- DIN 1.2625
- FED QQ-T-570