Rare earth (RE) magnets have revolutionised the properties and applications of permanent magnets. They offer many advantages, and have drastically increased flux compared to traditional magnets with comparable volumes. A figure of merit for a permanent magnet is the maximum energy product, (BH)max - the larger the value of (BH)max, the smaller the volume of the magnet required to produce a given magnetic flux. This is graphically illustrated by figure 1 where the three magnets, lodestone, strontium ferrite (SrFe12019) and NdFeB (Nd2Fe14B) all develop the same flux. The variation of (BH)max over this century is illustrated in figure 2, which shows that there was a dramatic rise with the advent of magnets based on SmCo5 in the mid-sixties. The steep rise continued with the development of magnets based on Sm2(Co,Fe,Cu,Zr)17 and, most recently, Nd2Fe14B. It is now possible to purchase NdFeB-type magnets with (BH)max values in excess of 400 kJ.m-3 compared with the old 10 kJ.m-3 steel, horse-shoe-type magnets at the beginning of the century. It is, however, still a question of ‘horses for courses’ and ‘bucks per flux’, so all three types of the rare earth magnets are still in production, together with AlNiCo types and the much cheaper but lower performance strontium ferrite magnets. 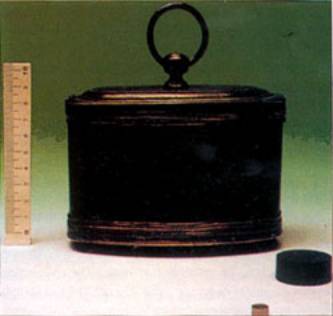 | Figure 1. Size comparison of a lodestone, strontium ferrite and NdFeB-type magnets all producing the same magnetic energy. | 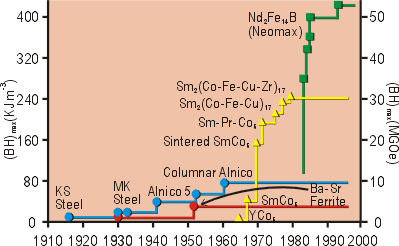 | Figure 2. Evolution of high (BH)max permanent magnets. | Applications The rate of growth in the production of RE magnets has continued unabated even during the current downturn in the world economy. Sintered NdFeB magnets are exhibiting a current growth rate of ~12% whereas the growth rate for bonded NdFeB magnets is in excess of 20%. The total value of hard magnets now exceeds that of soft magnets and the gap is widening. Why has there been this spectacular growth in RE magnets, and in NdFeB in particular? To some extent it reflects the global growth in PCs, as around 60% of NdFeB magnet production goes into disc drive applications, primarily voicecoil-motors (VCMs). This is by no means the whole story, however with rare earth magnets finding uses in industries such as automotive, telecommunications, data processing, consumer electronics, electronics and instrumentation, astro and aerospace, biosurgical and industrial applications such as Dc motors, robotics and magnetic separators to name but a few. Many of these are capable of substantial further growth. A particularly promising area is the use of permanent magnets in medicine and a potentially major use could be in magnetic resonance imaging (MRI) systems. Servo and linear drives also constitute strong growth areas, particularly in industrial robots where high performance, high torque motors are required. Another strong influence on the growth of NdFeB-type magnets has been the huge expansion in the use of mobile phones, and NdFeB magnets are employed in significant amounts as isolators in microwave stations. Automotive Industry In general terms, permanent magnets are far more important than is generally realised and this is perhaps, best illustrated by their growing use in the motor car. In the early 1950s a car would have only one magnet, in the speedometer, whereas a modern car can have over 50 permanent magnets. Currently these are almost exclusively based on the low cost Sr-ferrite (SrFe12019) magnets, and the penetration of NdFeB magnets into this area would require a significant cost reduction. The potential benefits of using the NdFeB magnets would be a significant reduction in volume and weight and an improved efficiency. Thus a taxation regime that favoured low C02 production (due to the pressures of global warming) could radically affect the cost effectiveness of NdFeB magnets in transport-type applications. This could be a major influence in the use of these magnets in the future. Other Applications Some of the many and varied applications of permanent magnets are summarised in table 1. Table 1. Summary of uses for permanent magnets. | Automotive | Starter motors, anti-lock braking systems, motor drives for wipers, injection pumps, fans and controls for windows, seats etc, loudspeakers, eddy current brakes, alternators, speedometers. | Telecommunications | Loudspeakers, microphones, telephone ringers, electro-acoustic pick-ups, switches and relays. | Data Processing | Disc drives and actuators, stepping motors, printers. | Consumer Electronics | DC motors for showers, washing machines, drills, citrus presses, knife sharpeners, food mixers, can openers, hair trimmers etc, low voltage DC drives for cordless appliances eg drills, hedgecutters, chainsaws, magnetic locks for cupboards or doors, loudspeakers for TV and audio, TV beam correction and focusing devices, CD drives, video recorders, computers, electric clocks, analogue watches. | Industrial | DC motors for magnetic tools, robotics, magnetic separators for extracting metals and ores, magnetic bearings, servo-motor drives, lifting apparatus, brakes and clutches, meters and measuring equipment. | Electronics and Instrumentation | Sensors, contactless switches, NMR spectrometers, energy meter discs, electro-mechanical transducers, crossed field tubes, flux-transfer trip devices, dampers. | Astro and Aerospace | Frictionless bearings, stepping motors, couplings, instrumentation, travelling wave tubes, auto-compass. | Biosurgical | Dentures, orthopaedics, wound closures, stomach seals, repulsion collars, ferromagnetic probes, cancer cell separators, magnetomotive artificial hearts, MRI scanners. | Future Applications Growing concern about global warming has many scientific and technological implications and some of these impinge on the use of NdFeB magnets. Future applications could include their more widespread use in ‘white goods’ such as washing machines, refrigerators etc, in order to improve energy efficiency and hence reduce C02 emissions. Another major use could be in generators for domestic combined heat and power (CHP) units and in clean energy production such as windmills. The biggest potential, however, is in electrical vehicles (EVs) which could be hybrid vehicles or totally driven by electricity in the form of batteries or a fuel cell. There has been an enormous increase of interest and activity in this area over the past 5 years and, as usual, the Japanese have been the first to commercialise these vehicles on a significant scale. Toyota is currently producing about 4000 hybrid vehicles per month (the Prius), which employ NdFeB-permanent magnet electric motors and Ni-metal hydride (also RE alloys) batteries. Many of the prototype EVs throughout the world employ NdFeB magnet motors and the commercial production of these vehicles would represent a very substantial rise in the amount of sintered NdFeB magnets required by the automotive industry. One possible production prediction is given in Table 1. | Percent EVs using PM Motors (%) | 5 | 25 | 50 | 80 | Average weight of NdFeB/car (kg) | 2 | 1.75 | 1.5 | 1.25 | Total weight of NdFeB (tonnes) | 2.3 | 97 | 665 | 3400 | Assumed price of NdFeB/kg ($/kg) | 150 | 100 | 75 | 50 | Net value of NdFeB (millions $) | 0.35 | 9.7 | 50 | 170 | Technical Challenges There are many technical challenges related to these developments which appear destined, in the long run, to replace the internal combustion engine. The NdFeB magnets required for EVs need to be able to operate up to a maximum temperature of ~180°C, and this currently requires a significant amount of dysprosium (Dy) substitution for the neodymium (Nd). This results in a substantial increase in the cost of the magnet and Dy is much less plentiful than Nd, so there will eventually be a resource problem if an effective substitute cannot be found. This represents just one of the many scientific/technological challenges associated with these materials. Another is the need for improved corrosion resistance in what could be very aggressive environments. A prototype all-electric vehicle is shown in figure 3. 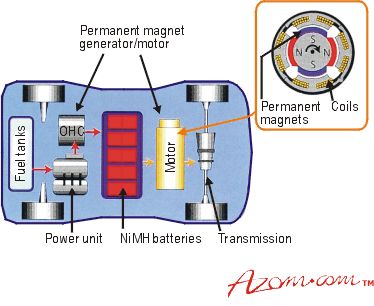 | Figure 3. Prototype electric vehicle (EV). | Magnetic Anisotropy The properties of strontium ferrite and the RE-magnets depend upon the phenomenon of uniaxial magnetocrystalline anisotropy. This means that they possess a crystal structure with a unique axis, which corresponds with the easy axis of magnetisation. In the case of Nd2Fe14B, the c-axis of the complex tetragonal structure, is the easy axis of magnetisation and this means that fine, single crystal powder of this phase can be aligned along the c-axis by the application of a magnetic field. This allows the production of an aligned, fine grain, fully dense compact which, when magnetically pulsed (~4 T) along the c-axis becomes fully magnetised and exhibits a very high resistance to demagnetisation (i.e. it has a high coercivity). The coercivity depends on the grain size and degree of orientation, among other factors, and may be reduced significantly by certain microstructural parameters. The production process for fully dense sintered magnets is designed to produce a well-aligned, uniformly fine grain structure with a low density of demagnetisation sites. The latter can be achieved by a liquid phase sintering process, which smooths the grain boundaries. The coercivity can also be enhanced by the magnetic isolation of the individual grains, which inhibits the propagation of reverse magnetic domains from one grain to another. The HD Process Work at Birmingham (UK) has shown that hydrogen can be used very effectively in the production of fully dense sintered NdFeB-type magnets. The process is called the hydrogen decrepitation (HD) process, figure 4. It relies on the fact that the bulk alloy (induction melted) consists of the ferromagnetic matrix phase, Nd2Fe14B and a Nd-rich, grain boundary eutectic which readily absorbs hydrogen at room temperature and at <1 bar hydrogen pressure. This results in the formation of neodymium hydride and the consequent differential expansion results in the decrepitation of the bulk material. The initial failure is predominantly intergranular in nature and the exothermic nature of the reaction causes the alloy to heat up and hydrogen is absorbed subsequently by the matrix phase to form a Nd2Fe14BHx solution. 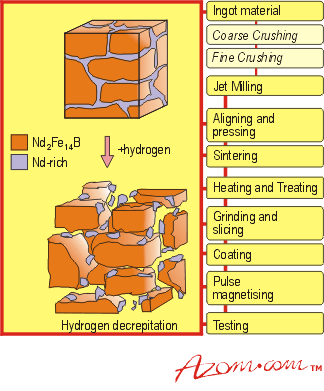 | Figure 4. The HD-route for the production of sintered NdFeB-type magnets. | Advantages of the HD process The HD-powder is extremely friable and can be readily jet-milled to the final powder size of a few microns required to produce the fully dense, sintered magnet. There are a number of advantages of the HD process but the main one is the much increased friability of the powder compared with that of the conventional material. It has been estimated that the capacity of the jet mill can be increased by a factor of around 4 by using the HD-powder and this represents a very significant economic and environmental advantage. At this stage, the composition of the magnet can be adjusted by appropriate powder blending. Production of permanent Magnets using the HD Process The fine, single crystal powder is then aligned in a magnetic field prior to compaction to form an aligned ‘green compact’ which is ~50% dense. Another interesting and useful feature of the HD-process is that, unlike the conventional powder, these compacts do not exhibit any coercivity and are therefore easy to handle. The hydrogen is still contained within the compact but is removed completely during the subsequent vacuum sintering operation. The loss of hydrogen can be monitored and the various stages of the desorption process are shown in figure 5. Once the hydrogen is fully desorbed, the Nd-rich material melts and liquid phase sintering is achieved at around 1000°C. The sintering temperature and time have to be carefully controlled to avoid excessive grain growth, which degrades the magnetic properties, in particular the coercivity. In addition to the normal reduction in volume during sintering, there is also anisotropic shrinkage and substantial machining is often required to achieve the final dimensions. These are hard and brittle materials and the dimensional changes are usually achieved by centreless grinding. The waste material is not recycled and machining represents a significant fraction of the cost of the magnet. There are powerful environmental and economic arguments for producing net-shape magnets and this is the subject of one aspect of the research and development programme being carried out in the NetShape Manufacturing Laboratory at Birmingham. 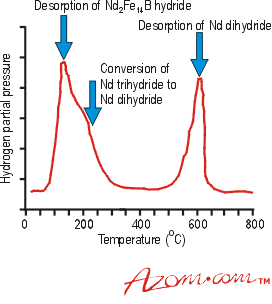 | Figure 5. The loss of hydrogen during vacuum sintering. | The magnets with the best properties are achieved by the process of magnetic pulsing and cold isostatic pressing, followed by sintering. However, this is a batch process and hence not best suited to mass manufacture. A compromise technique has been developed in Japan which is called rubber isostatic pressing, with the unfortunate acronym of RIP. This is a cross between uniaxial and isostatic pressing. The powder is pressed in a rubber mould and much better alignment of the powder is achieved by this means, compared with that of standard uniaxial pressing, through the use of a magnetic punch. This is manifested in much improved values of (BH)max. The trend in NdFeB-type magnets is towards higher and higher (BH)max values towards the likely maximum value of about 450kJ.m-3. To achieve these high values (>400 kJ.m-3) requires alloys with compositions close to that of stoichiometry (Nd2Fe14B). The problem is that this phase forms by a peritectic reaction between α-Fe and liquid so that, in the normal, as-cast ingots there is a substantial amount of dendritic free iron. To avoid this problem, a process of ‘strip casting’ is employed to produce an α-Fe-free material prior to the HD-process. The strip cast material is cooled rapidly and has a regular grain size with a uniform distribution of the Nd-rich material. Because of the limited amount of the latter, the oxygen content has to be very carefully controlled in order to maintain sufficient liquid phase to achieve full density on sintering. This demands a high level of process engineering. The HDDR Process This is not the end of the hydrogen story. Hydrogen is also employed in the hydrogenation disproportionation desorption and recombination (HDDR) process, figure 6. Unlike the more straightforward HD-process, the HDDR route involves heating the bulk alloy in around 1 bar of hydrogen to ~800 °C. The first stage is the decrepitation of the alloy due to the initial absorption of the hydrogen, as described previously. 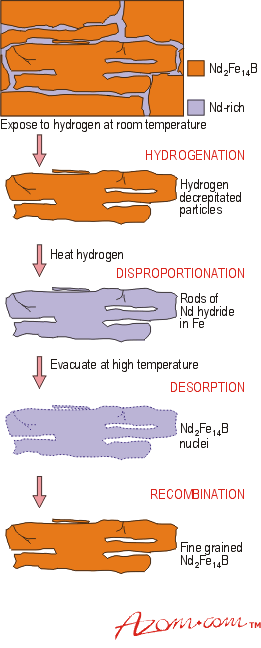 | Figure 6. The HDDR process. | However, at ~700 °C, the Nd2Fe14B matrix phase disproportionates according to the reaction: Nd2Fe14B + (2±x)H2 ⇔ 2NdH2±x + 12Fe + Fe2B + ΔH where the particular value of x depends on the pressure and temperature. This is an exothermic reaction and the disproportionated alloy consists of an intimate mixture of fine rods of NdH2±x in an α-Fe matrix. The Fe2B phase forms isolated grains. The vital feature of this reaction is that it is fully reversible and when a vacuum is applied, the hydrogen is desorbed and the original Nd2Fe14B phase reformed. The most significant aspect of the HDDR process is that there is a dramatic change in the microstructure from an initial grain size of typically 150µm to a very fine, uniform grain size of about 0.3µm, i.e. a reduction of 500 times. On magnetisation, the HDDR powder exhibits an appreciable coercivity and this means that, in its simplest net shape form, the powder can be mixed with a thermosetting resin to produce an isotropic permanent magnet by compression moulding. Modification of both the composition of the start material and the processing conditions can also result in the production of anisotropic powder with a substantial improvement in the magnetic properties. Advantages of the HDDR Process Another promising feature of the HDDR powder is that it exhibits excellent hot pressing characteristics and fully dense, near net shape, isotropic magnets can be produced by hot pressing at 750°C in an inert atmosphere. The hot pressing and magnetic characteristics of this material are being examined as part of the research and development programme within the NetShape Manufacturing Laboratory and this could represent a very cost effective means of producing fully dense NdFeB-type magnets for electric motors. The HDDR process has wider possibilities than just the production of NdFeB-type magnets and work in Japan has shown that it can be employed very effectively to produce ultra fine grain material based on the compound TiAl. It will not be universally applicable however, as an essential prerequisite is that at least one of the component elements in the particular compound must be a stable hydride former (e.g. Nd or Ti). Summary There remains considerable potential for process innovation in the manufacture of RE magnets with the aims of improving their performance and/or reducing their cost. There are also exciting possibilities in the general area of the hydrogen processing of materials because of the influence hydrogen can exert on various solid state processes and because of the need to avoid C02 production. The materials scientist and engineer will continue to play a vital role in these challenging new areas of science and technology. |