In contrast to visible light, X-rays cannot be effectively deflected by ordinary mirrors. Either natural crystals have to be used, or (particularly for soft X-radiation, where crystals with suitable lattice spacings are not available) a particular preparation of crystal-like structures at the reflecting surface is required, to realise the so-called Bragg reflection in the near-surface region of the mirror. An actual artificial reflector consists of a stack of typically 100-200 alternating nanometer-thick layers made from two different chemical elements. They are produced by coating each layer to a precise thickness, with an accuracy in the order of picometers. Layered synthetic microstructures (LSMs) are used in soft X-ray optics as Bragg reflectors for various applications, e.g. collimators, monochromators, mirrors, and focusing optics. In contrast to conventional Langmuir-Blodgett-films, these layer stacks show an outstanding reflectivity of typically 10-80%, even for near-normal incidence of X-radiation. Uses of X-Ray Mirrors X-rays are used in a wide spectrum of analytical technologies. Appropriate mirrors will find a widespread use in spectroscopy, e.g. total reflection X-ray fluorescence (TXRF), and in reflectometry (XRR), diffractometry (XRD), microscopy and astronomy. The techniques of XRR and XRD are frequently used for the characterisation of synthetic materials and natural products in bulk form or as thin solid films. Characterising a material requires information about morphological properties such as structure, thickness, and surface quality, physical properties such as density and reflectivity, as well as composition, i.e. which chemical elements form the major components. X-Ray Diffractometry Certain factors are important to obtain a good diffractometer performance - the accuracy of the line position i.e. the position of the detected radiation peak), the profile shape of the peak, the overall diffracted intensity and the signal-to-noise ratio. The low intensities involved in most of the conventional techniques necessitate the use of focusing geometries, where source, specimen surface and detector slit are located on a circle. This so-called Bragg-Brentano configuration is the standard device for powder diffractometry. It is obvious that deviations from the ideal geometry, i.e. surface irregularities, transparency, tilt or displacement of specimen will lead to significant shifts of line position. Further serious drawbacks - mainly resulting from the divergent beam configuration - that will influence instrumental performance are: • the need for time-consuming specimen preparation • the low intensity of primary radiation approaching the specimen • the critical and complicated adjustment of specimen position. Beam divergency of conventional X-ray sources and specimen surface morphology are the primary factors leading to complications in conventional diffractometry and reflectometry. The angles and distances between specimen and optical components have to be considered in taking measurements. Errors in measurements can be caused by specimen displacement, transparency and tilt, as well as surface irregularities. Profile asymmetries and displacements of peak intensities are one type of distortions of the diffractograms that may occur if the specimen and optical components are misaligned. Alignment procedures can waste large amounts of time and demand a great amount of patience. Gobel Mirrors Recently, we have realised a substantial development in reflectometer/diffractometer apparatus, by introducing a new and innovative X-ray optical element into the beam path. The integration of the so-called Gobel Mirror (GM) has resulted in a noticeable improvement in experimental conditions and analytical power for both the Single Gobel Mirror (SGM) and Twin Gobel Mirror (TGM) configurations. How do they Work? This improvement is achieved by collecting X-ray photons emerging from the line focus of a conventional X-ray tube within an increased acceptance angle, and forming an intense parallel and monochromatic beam with very low divergency. This forms the basis of new, highly efficient, parallel beam diffractometry/reflectometry techniques. Advantages In comparison to the conventional techniques, the SGM and TGM configurations have the advantages of: • a substantial increase in primary intensity at the specimen site • easy and quick specimen adjustment • an effective suppression of extraneous radiation, and • an improved signal/noise ratio. This results in either increased precision of measurement and power of detection, or considerable reduction of analysis time, regardless of surface morphology, specimen displacement and transparency. Figure 1 shows a schematic representation of the TGM configuration. This arrangement combines the characteristic parameters of the parallel beam geometry with the outstanding features of Ni/C-type Gobel mirrors. Extremely high photon fluxes, of the order of one billion counts per second, with a beam divergency of <0.02° can be realised in XRR and XRD without changing any optical component of the beam path. The suppression of unwanted radiation - because fluorescence radiation is almost completely eliminated - increases the signal-to-noise ratio significantly, so that second phase contents are detectable below 5% even with Cu(Kα) radiation. 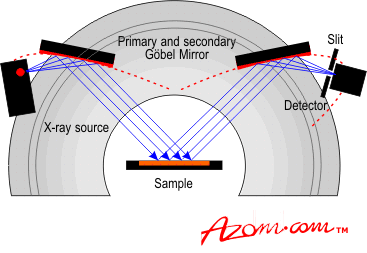 | Figure 1. Principal of a twin Gobel mirror diffractometer. | A noticeable improvement of adjustment procedures is achieved by using the parallel beam geometry. A single scan determines the alignment position in XRR, so that the specimen position is no longer the limiting factor for this technique. No change in Bragg peak position is observed for vertical specimen shifts of ±200µm from the ideal position. Structure of a Gobel Mirror A Gobel mirror must have a certain structure to give it the required properties. To convert a divergent beam (emitted from a point source) into a parallel beam of very low divergency, the partial beam intensity within a defined acceptance angle must be reflected at the surface of a parabolic mirror segment. This guarantees that in each point of the segment, Bragg’s law is fulfilled for the angle of incidence. The reflectivity of the segment is determined by the parameters of the multilayer stack that the segment is coated with. For optimum conditions, it is important that the period width of the multilayer follows Bragg’s law too, so that for lateral direction a continuously changing angle of incidence is compensated by a graded period width. How are they Produced? High quality X-ray reflectors are nowadays prepared by electron beam evaporation, sputter deposition or pulsed laser deposition (PLD). PLD is used for this highly technical process in only a few labs throughout of the world. Achieving thin film uniformity is a serious drawback of conventional PLD, so sophisticated coating equipment is required to provide high quality nm-layer stacks on substrates of technical dimensions. However, with the right equipment, PLD is a useful technique for mirror synthesis because the use of a precisely controllable system can create uniform and precisely adjusted average layer thicknesses in the sub-nm range. The coating process involves pulsed laser ablation (i.e. atomisation) of the coating material target with simultaneous ignition of a plasma plume, because of the high power density in the laser beam cross section at the target surface. Subsequent condensation of the atomic flux emitted by this plasma causes the formation of a thin solid film at the surface of a high quality substrate. The striking feature of this nm-film is an intrinsic surface roughness of infinitesimal amplitude (e.g. σ has an order of magnitude of typically 0.1 nm). Among the diverse coating techniques, PLD seems to be rarely used - hitherto its predominant application has been in laboratory experiments concerning above all methodical investigations. Only a few applications are found in literature dealing with exploitation on a technical level. The technique demands sophisticated hardware and automated control of the entire coating process to realise high quality coatings on substrates of technical relevance. Thus large area PLD is still in its infancy as a production tool. Recently, efforts by the Fraunhofer Institute of Materials and Beam Technology (Fh IWS) and its partners has led to the installation of an automated dual beam deposition system providing a fully automated coating regime for high quality nm-multilayers on 10 cm substrates for X-ray optical applications. Figure 2 shows the basic principle of the PLD target/substrate handling. The generation of a laterally homogenised integrated particle flux is achieved by an innovative control regime, utilising the periodic change of spatial orientation of the plasma plume. 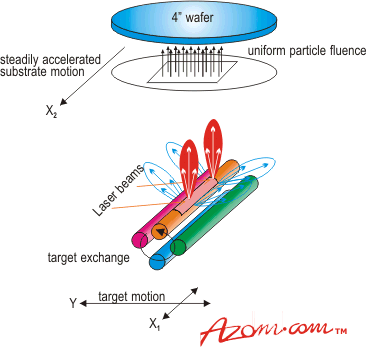 | Figure 2. Schematic diagram of target/substrate handling in large area PLD. | Scanning the laser beam across the surface of cylindrical targets causes these motions as the symmetry axis of expansion almost coincides with the surface normal of the surface element that the plume emerges from. Applications Various types of X-ray mirrors, particularly Gobel mirrors for Cu(Kα) and Mo(Kα) radiation - are prepared for analytical applications in Bruker-AXS diffractometers, IUT TXRF systems and for individual research institutions. |