Updated 15/06/23 by Reginald Davey
Autofrettage is a metal fabrication method, similar to shot blasting, with a wide range of applications, from the manufacture of gun barrels on battleships and tanks to fuel injection systems for diesel engines.
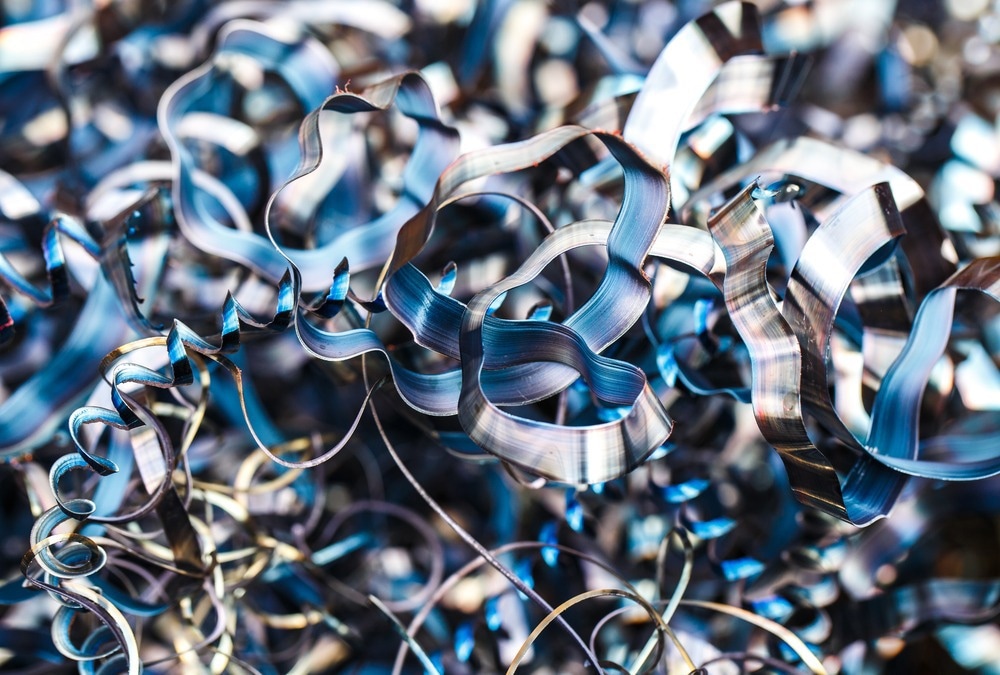
Image Credit: David Tadevosian/Shutterstock.com
During metal fabrication, a pressure vessel is subjected to immense pressure, which causes the internal parts of the vessel to yield, thus resulting in internal compressive residual stresses. The purpose of using autofrettage is to enhance the durability of the final product and also increase its resistance to stress corrosion cracking.
How Does Autofrettage Work?
A single steel tube with internal diameter lesser than the resultant diameter is used for performing the autofrettage method. Pressure, otherwise known as autofrettage pressure, is used on the tube to expand the bore and to stretch the inner layers of the metal beyond their elastic limit such that the metal can no longer return to its original shape.
Autofrettage pressure is much greater than working pressure. Despite the extreme internal pressure, the outer layers are not stretched beyond their elastic limit. This is because the stress distribution via the walls of the tube is non-uniform.
The change only occurs to the metal adjacent to the source of pressure. As the outer layers are still in their elastic state, they tend to return to their original shape, but this is prevented by the permanently stretched internal layers.
The stretched internal layers are subjected to low temperature heat treatment causing the elastic limit to be further increased.
If autofrettage pressure is needed for a bent pipe, autofrettage needs to be performed after bending. Similarly, if an object has cross cutting, care should be taken while applying autofrettage pressure as stress concentrations around the drill hole can cause cracking.
In this case, the crack only develops to a certain length and stops due to the internal stresses that are inside the wall which press the crack together. In order to optimize internal stress, autofrettage pressure must be held for a short period.
Two common autofrettage processes are:
- Peening of the surface with metallic or ceramic spheres
- Forcibly inserting a mandrel that is larger than the hole, thus straining the inner material layers.
Autofrettage Applications and Products
Autofrettage is widely used in various industries. It is used to increase operating pressures for advanced industrial, automotive, aerospace and defence systems and improve component fatigue life.
Autofrettage is also used for strengthening cannon barrels. Similarly, the process is applied in the expansion of pipes for oil and gas wells. Meta, a Norway-based oil service company, uses it to connect concentric tubular components with optimal sealing and strength properties.
More specifically, autofrettage is used in numerous engineering applications to change the inner surface of a container by inducing permanent compression to its inner layers. It is fairly similar to pre-stressing concrete for building bridges.
Autofrettage Benefits
Autofrettage provides the following benefits:
- Autofrettage increases the working pressure components can operate at without failing. In the case of pipework, working pressure can be increased by up to 1.8 times, and in components with cross boring this figure can be 2.5 times higher.
- The spreading of the resultant pressure changing numbers in the time solidity area of the “Wöhler line” decreases
- In tests, autofrettage components have a spreading of T<=1,1, while non-autofrettage parts in general have a spreading of T=1,3.
- Notch sensitivity is greatly reduced.
The following improvements are achieved due to the collective benefits of autofrettage:
- The working pressure remains the same - the thickness of component wall is reduced.
- When working pressure remains the same, inexpensive material can be used.
- Working pressure can be increased overall
- Borings and surface finishings can be eliminated.
- At a corresponding working pressure, the service life of a component can be increased.
In Summary
Autofrettage pressure helps to improve a component’s working pressure before failure. Autofrettage is a vital and relatively straightforward process in many industries and can be used to produce many different products with improved strength and key material properties.
More from AZoM: What are the Key Components of an Internal Combustion Engine and How Do They Work?
Sources and Further Reading
Poppe + Potthoff (website) Autofrettage [online] autofrettage-machine.com. Available at:
https://www.autofrettage-machine.com/
https://maximator-test.com/
Disclaimer: The views expressed here are those of the author expressed in their private capacity and do not necessarily represent the views of AZoM.com Limited T/A AZoNetwork the owner and operator of this website. This disclaimer forms part of the Terms and conditions of use of this website.