What is an engineering thermoplastic? Such a definition is difficult to arrive at and is very subjective, but, for the purposes of this review article, any thermoplastic that can be formed into a load-bearing shape that might otherwise be formed from, for example, steel or wood will be classed as an engineering thermoplastic. This review is restricted to unreinforced and short fibre reinforced thermoplastics where the reinforcing fibre (usually glass or carbon) is typically less than 2-3 mm in length.
Thermoplastics offer many advantages over traditional materials, including: low density; low energy for manufacture; low processing costs; and the ability to make complex shapes relatively easily.
Thermoplastic Characteristics
Thermoplastic materials generally fall within two classes of molecular arrangement, amorphous and semi-crystalline (see figure 1).
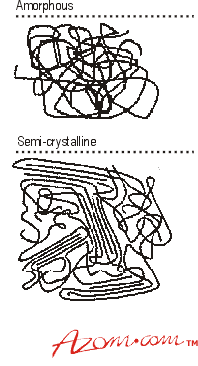
|
Figure 1. Molecular Arrangement of Polymer Chains
|
Table 1 lists a selection of amorphous and semi-crystalline polymers.
Table 1. Amorphous and semi-crystalline polymers.
Amorphous
|
Polyamideimide
|
Polyetheretherketone
|
Polyethersulphone
|
Polytetrafluoroethylene
|
Polyetherimide
|
Polyamide 6,6
|
Polyarylate
|
Polyamide 11
|
Polysulphone
|
Polyphenylene sulphide
|
Polyamide (amorphous)
|
Polyethylene terephthalate
|
Polymethylmethacrylate
|
Polyoxymethylene
|
Polyvinylchloride
|
Polypropylene
|
Acrylonitrile butadiene styrene
|
High Density Polyethylene
|
Polystyrene
|
Low Density Polyethylene
|
Amorphous Polymers
Generally, fully amorphous polymers are stiff, brittle and clear in the virgin state. The temperature and stress state have a profound effect on the molecular arrangement and hence the properties of a polymer. Under the action of sufficient stress, the polymer chains can uncoil and align over a period of time. At elevated temperatures, polymer chains have enough energy to rotate and coil up further.
Figure 2 shows schematically the effect of temperature on the elastic modulus of an amorphous and a semi-crystalline polymer. Below a temperature known as the glass transition temperature, Tg, the structure of amorphous polymers is termed 'glassy', with a random arrangement of the polymer chains, similar to the random molecular arrangement found in glass. As the temperature increases to Tg, the polymer chains have sufficient thermal energy to rotate, resulting in a drop in modulus. One definition of Tg is the temperature at which molecular rotation about single bonds becomes favourable as the temperature increases. At temperatures above Tg but below the melting temperature, Tm, there is a 'rubbery region', where the material can exhibit large elongations under relatively low load. Amorphous thermoplastics are generally used at temperatures below their Tg, where they can be brittle, just like glass. There are, however, certain exceptions. Polycarbonate (PC) is amorphous yet it is considered tough at temperatures well below its Tg. When it does fracture below its Tg, it does so in a brittle manner, but this requires a large amount of energy and so PC is considered tough, finding use in applications requiring impact resistance, e.g. safety helmets and bullet proof glazing. This behaviour is due to the chemical bonds in polycarbonate rather than the arrangement of the polymer chains.
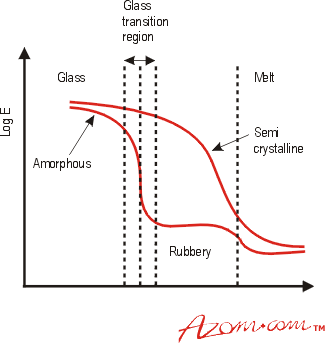
|
Figure 2. The effect of temperature on the Elastic Modulus (assuming both types of polymer have the same Tg and Tm)
|
Semi-Crystalline Polymers
Semi-crystalline materials such as polyamides do not exhibit a clear Tg or 'rubbery' region, although one is often quoted as the amorphous parts of the structure will undergo some transition. For these polymers the main transition occurs at Tm when the crystalline regions break down (see Fig. 2). Some chain rotation in the amorphous regions will occur below Tm, giving some impact resistance at these temperatures. Values of Tg and Tm for a number of polymers are given in Table 2.
Table 2. Glass transition and melting temperatures for a range of thermoplastics.
Polymer
|
Tm (°C)
|
High density polyethylene (HDPE)
|
-
|
135
|
Polypropylene (PP)
|
-10
|
175
|
Polystyrene (PS)
|
100
|
-
|
Polymethylmethacrylate (PMMA)
|
105
|
-
|
Polyvinylchloride (PVC)
|
65
|
-
|
Natural rubber (NR)
|
-75
|
25
|
Polydimethyl siloxane (PDMS)
|
-125
|
-55
|
Polyoxymethylene (POM)
|
-30
|
175
|
Polycarbonate (PC)
|
150
|
-
|
Polyethylene terephthalate (PET)
|
70
|
265
|
Polyetheretherketone (PEEK)
|
145
|
335
|
Nylon 6 (PA6)
|
50
|
215
|
Polyamideimide (PAI)
|
295
|
-
|
Polysulphone (PSul)
|
195
|
-
|
Polyphenylene sulphide (PPS)
|
90
|
285
|
Polyethersulphone (PES)
|
230
|
-
|
Polyetherimide (PEI)
|
218
|
-
|
Polytetrafluoroethylene (PTFE)
|
20
|
325
|
Liquid crystal polymer (LCP)
|
-
|
420
|
Table 2. Values of Tg and Tm for selected polymers
|