Mar 8 2013
Table of Contents
Introduction
Scratch Analysis
Local vs. Apparent Friction Coefficients
Scratch Damage of Coating
Conclusion
About CSM Instruments
Introduction
In contact mechanics analysis, a major issue is to change the rigidness predicted from load contact versus contact radius behaviours as well as depth versus load behaviours into a stress-strain relationship.
Normally, when the load is recorded from the load cell, the exact depth and the exact contact radius depend on a model, which in turn depends on the type of behaviour, like plastic, elastic and elastic-plastic. However, this issue is not a major problem in the case of steel. In contrast, there are no models that consider the viscoplastic and viscoelastic behaviour of the material.
A new apparatus was developed in order to examine this issue. This apparatus was capable of controlling the velocity of the tip over a wide range of temperatures. An optical microscope was fitted on the apparatus in order to enable in-situ control and measurement of the contact area and the furrow left on the surface. The model of this apparatus is now available as an alternative for all CSM Instruments Indentation and Scratch Testers.
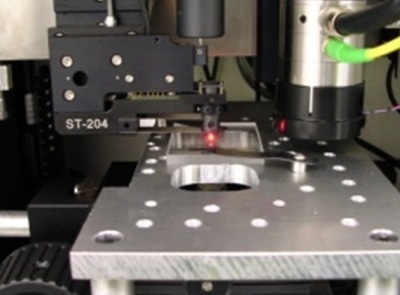
Figure 1. CSM Instruments Nanoscratch Nanoindentation tester including the in-situ vision set-up.
The prototype Mirau interferometer displayed in the above figure is equipped with a CSM Instruments Open Platform, which is positioned in a vacuum chamber.
This device can be moved either under the Nanoindentation Tester Module or under the Nanoscratch Module. This application note will outline the latest results acquired through this set-up.
Scratch Analysis
The analysis of the scratch behavior is enhanced through in-situ observation of the contact area, and hence models are not required to estimate the surface behavior like in the case of a blind test. Moreover, in-situ observations offer critical data about the properties of bulk materials.
During the scratching process, the local strain rate can be assumed as the tip speed separated by the contact radius, and the entire experimental measurements of the mean contact pressure can possibly be plotted as a function of this strain rate.
The scratch hardness, which denotes contact pressure in case of plastic contact, thus seems to be temperature and time activated processes property similar to other mechanical characteristics for this type of material.
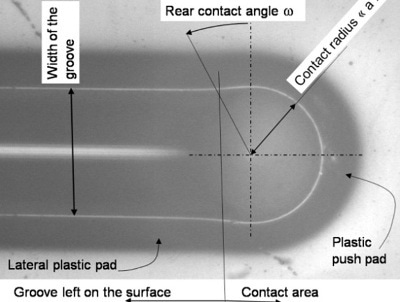
Figure 2. Typical image of the contact area during the scratching of a polymethylmetharylate (PMMA) surface.
The above figure shows a typical image of the contact area and the shape of the groove left on the surface. It can be seen clearly that the contact area’s diameter is larger than the groove’s width.
This is because of the elastic unloading soon after contact. Research on various polymeric surfaces has demonstrated that imposed elastic-plastic strain controls the scratch tests with respect to size and value, as well as its localization through depth below the moving tip.
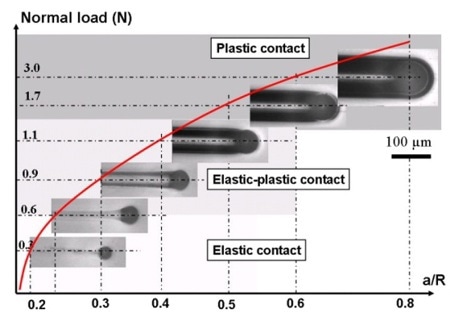
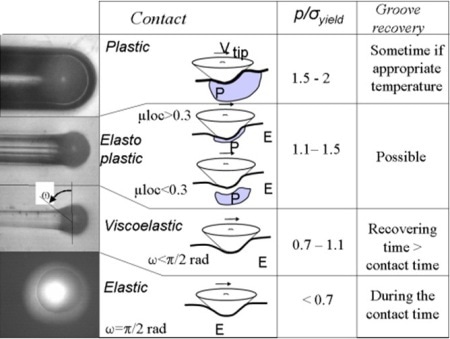
Figure 3. Mechanical transitions from elastic sliding to fully plastic scratching observed during experiments with increasing the applied normal load for PMMA (local friction coefficient was estimated at 0.2).
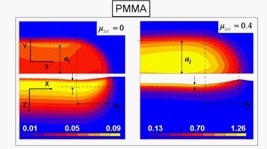
Figure 4. Equivalent plastic strain maps as computed by simulation for a/R=0.2 with µloc=0 and µloc=0.4 for PMMA.
Local vs. Apparent Friction Coefficients
When a stiff sphere glides on a soft polymer, the tip pierces into the material and produces a phenomenon called ploughing wave, wherein a huge amount of energy is scattered. This effect is added in the apparent friction coefficient µapp, which is defined as the ratio of the calculated tangential force over the applied normal load.
To consider this phenomenon and agree to a more local friction coefficient µloc, which denotes the ratio between the local contact pressure and the local shear stress, a model was utilized to examine the relationship between the mean contact pressure and the local friction coefficient, the structural recovery of the surface or the yielding of the surface.
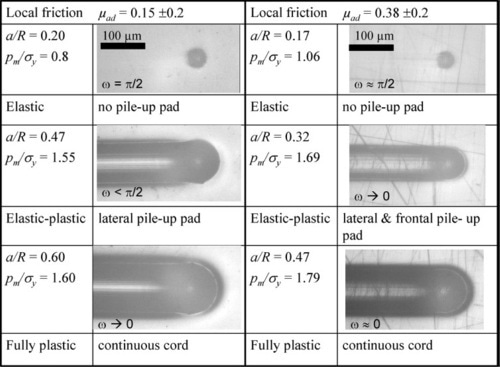
Figure 5. Experimental in situ observation of the contact geometry and the residual groove throughout the scratch tests (top view) as a function of the local friction coefficient and the mean geometrical strain a/R.
Thus, the actual contact area is the sum of a front and rear areas. The complication is to consider this rear contact so as to relate the actual and ploughing frictions to the calculated apparent friction.
Using four integrals A, B, C, and D, the true friction coefficient was linked to the apparent friction coefficient. The integrals are the elementary action integrals of the local shear and pressure, on the normal z-axis and on the sliding x-axis as illustrated in the figure below.
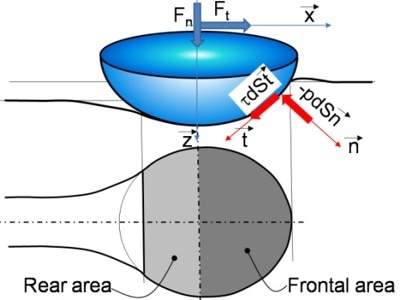
Figure 6. Rigid sphere sliding on a viscoelastic polymer showing the ploughing effect and the corresponding contact area.
Scratch Damage of Coating
The critical load, which causes the initial damage in a scratch test, represents a coating’s behavior. The second aspect of the durability of coatings is their adhesion with the substrate.
The analysis of comparable films with varied thicknesses showed that some confinement effect takes place and hence leads to an analysis of the results with respect to the probe characteristics such as roughness and size.
Conclusion
In-situ observation is important for analyzing the damage mechanisms such as spalling and blistering, which occur during scratching. Post mortem observation will not provide similar data because after unloading, the shearing stress and compressive fields vanish following the contact time.
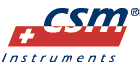
This information has been sourced, reviewed and adapted from materials provided by CSM Instruments.
For more information on this source, please visit CSM Instruments.