Sponsored by XradiaApr 22 2013
Carbon fibers are lightweight materials that have found use in a myriad of applications, ranging from electrical conductors, to airplane wings and structural reinforcements. These advanced materials demonstrate exotic characteristics such as high mechanical strength-to-weight ratio, high flexibility, superior corrosion resistance, and low thermal expansion. Existing challenges in fiber production and relatively high production costs have triggered the requirement for process optimization in order to manufacture homogeneous, quality carbon fibers and composites.
Significance and Challenges of Carbon Fiber Characterization
Three-dimensional (3D) microstructural characterization of carbon fibers provides the key insights for the optimization of production techniques. However, the challenge is that many techniques available such as conventional X-ray micro computed tomography and electron microscopy do not have either the penetration capabilities to investigate buried structures underneath the surface, or contrast and resolution to observe details of single fibers.
Solution from Xradia
The high resolution 3D X-ray microscopes (XRMs) from Xradia, consisting of the VersaXRM family with submicron capabilities and the UltraXRM system with a spatial resolution of down to 50 nm, provide multi-length scale determination of small-scale cracks and large-scale voids in order to perform flexible and comprehensive microstructural characterization of carbon fibers manufactured by different processes. A 3D volume rendering of the exterior of a carbon fiber is shown in Figure 1. It demonstrates the results of the imaging of a carbon fiber at 1 µm resolution utilizing the MicroXCT, a member of the VersaXRM family. This reveals the distribution of many large voids throughout the fiber.
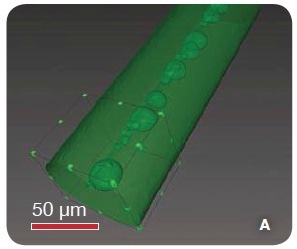
Figure 1. A 3D volume rendering of the exterior of a carbon fiber as imaged with 1 µm resolution using the MicroXCT. The image has been segmented to reveal voids throughout its interior.
The results of the imaging with the UltraXRM are shown in Figure 2, revealing the distribution of sub-micron voids throughout the sample.
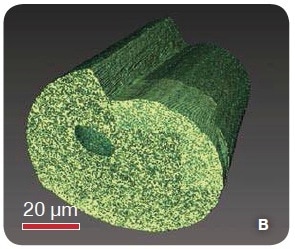
Figure 2. A higher resolution cross-section, imaged using the UltraXRM which reveals many submicron voids distributed throughout the fiber.
The results of the imaging of a 5-µm-diameter fiber with the UltraXRM are shown in Figure 3. A long, thin void was determined (highlighted in red) in the interior of the sample.
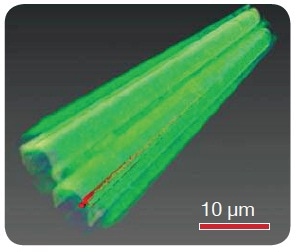
Figure 3. A volume rendering of two bonded carbon fibers is shown here, with a long, thin void labeled with red.
It is also possible to perform detailed characterizations of carbon fiber composites using 3D X-ray microscopes. Virtual cross-section of a carbon fiber composite utilized for airplane wings is shown in Figure 4, which reveals the presence of large voids within bundles of the 5-7 µm carbon fibers and the existence of two phases in the resin. These results will help researchers to gain insight into the impact of different manufacturing techniques on final products. Moreover, characterization with multi-length scale 3D X-ray microscopy provides data on the structure and orientation of carbon fibers and their composites.
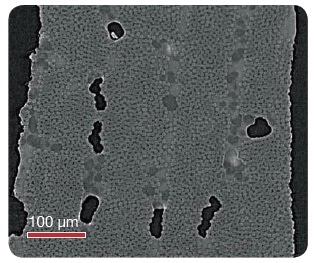
Figure 4. Virtual cross-section of a carbon fiber composite tomography
Conclusion
A high-resolution visualization technique is essential in order to optimize carbon fiber production processes. This requirement can be fulfilled with the Xradia VersaXRM and UltraXRM families of 3D X-ray microscopes, which provide unprecedented resolution and contrast for imaging entire volumes of single fibers. This measurement technique has the innovative capability of determining voids and cracks in 3D, thus providing the key insight required for optimizing the economic viability of carbon fibers.

This information has been sourced, reviewed and adapted from materials provided by Xradia.
For more information on this source, please visit Xradia.