Sponsored by XradiaApr 22 2013
There is a growing interest in the mineral processing industry as it is possible to achieve submicron resolution with high contrast on most mineral phases within mining ores. This tomographic technique enables rich statistics on grain sizes and particle damage. It offers basic mineralogy discrimination, opening a wide range of application possibilities.
The opportunities of providing improved analytical information span much of a mining site's lifetime, from rapid 3D characterization of ores for geometallurgical composition during exploration, inspection of plant feeds in comminution and floatation circuits, to liberation analysis of precious metals in tailing and heap leaching operations. Since this tomographic technique is performed with an X-ray microscope, it is non-destructive and also does not require complex preparation of polished sections typical of SEM-EDS techniques (such as MLA and QEMSCAN). It complements existing techniques by providing 3D information of these multi-phase particles: texture, size, distribution and mineralogy, using significantly larger sample volume statistics within a much shorter turnaround time.
Advantages of XRM in Mineral Processing
The advantages of XRM in mineral processing are:
- Minimal sample preparation
- Large volume statistics for high resolution characterization of tailings (PGMs, Au, Ag, Cu)
- Particle damage assessment during comminution
- Porosity and flow modeling of heap leaching
- Rapid 3D mineralogy and liberation analysis
- Coal washability analysis
- Precious metal identification in drill core
- Correlation to MLA/QEMSCAN
Precious Metals, Base Metals, Industrial Minerals, Rare Earth and Coal
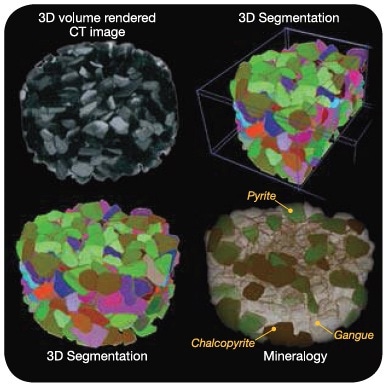
Figure 1. 3D segmentation and characterization of Cu ore. Samples scanned in a packed particle bed, 5 mm in diameter. >30,000 multiphase particles can be analyzed rapidly
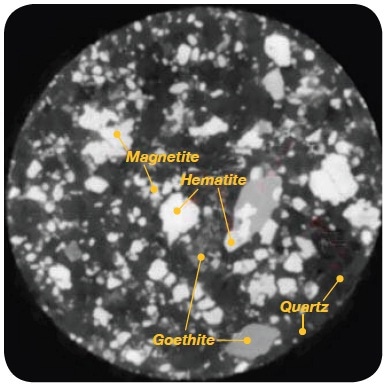
Figure 2. Low grade Iron ore, CT slice showing discrimination of valuable metal ore (Fe2O3/Fe3O4) versus Goethite (FeO(OH)) and Quartz (SiO2) (Particle size range - 0.3 mm + 0.1 mm, image Field of View: 5 mm)
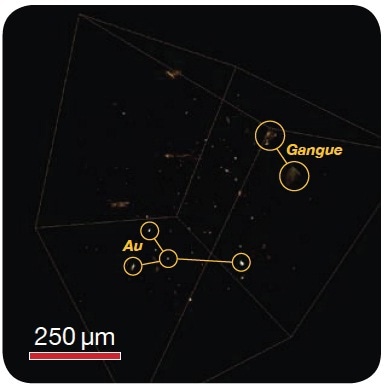
Figure 3. Rapid detection of gold, silver, or platinum group metals (PGMs), feed, concentrates or tailings. Large number of particles can be scanned in 3D to detect valuable phases. Image: Scanning for Au particles (bright particles) in 3D at 1 μm voxel within a 3 mm packed bed tube
VersaXRM-500 3D X-ray Microscope for Mineralogy
The Xradia VersaXRM-500 3D X-ray microscope works on the principle of computed tomography, just like those used in medicine for human body scanning, by taking X-ray radiographs of a sample at a number of rotational angles. However, unlike conventional medical CT, industrial CT or desktop microCT, which use a simple geometric magnification principle to achieve resolution, the VersaXRM depends on an architecture that is derived from technology originally developed for XRM used in synchrotron radiation facilities. It features a unique two-stage magnification imaging technique based on its proprietary detector and optics that enables it to achieve <0.7 µm spatial resolution (<150 nm voxel) on relatively large samples.
Furthermore, the VersaXRM-500 optics employ advanced contrast mechanisms that uniquely allow for the discrimination of valuable mineral phases from the gangue materials within a class of ores, including the ability to differentiate minerals with similar X-ray attenuation, such as platinum and galena (in PGMs) and chalcopyrite and magnetite (in certain Cu ores). The high contrast features also enable difficult to image internal fracture networks within particles required to optimize the comminution process. The resulting high resolution and high contrast volumetric dataset enables large numbers of particles in 3D to be characterized rapidly using Xradia's specialized software for Mineral Liberation of Multiphase Particles, Exposure Analysis in floatation, Damage Assessment in comminution and Porosity and Flow Modeling in heap leaching experimentation and mine planning set up. The system complements existing SEM-EDS techniques for mineral processing and is especially beneficial for large volume, rapid detection of precious metals (Au, Ag, PGMs) during the various processing steps and especially in tailings.
Comminution and Particle Damage Assessment
By studying fracture networks within particles, it is possible to determine the energy required for comminution and predict the efficacy of liberation techniques, as fracture networks provide pathways for leachants and flotation chemicals to reach interior locked particles. With high resolution X-ray microscopy, detailed 3D analysis of fracture networks can be performed before and after comminution to establish fracture mechanisms such as transgranular random breakage or preferential breakage.
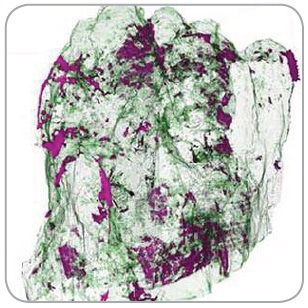
Figure 4. Communition
Exposure Analysis in 3D for Mineral Liberation
With XRM and software, 3D analysis enables the determination of Size Fraction vs Locking Class over a large number of particles
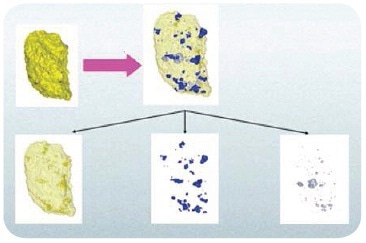
Figure 5. Floatation
In Situ Observation of Particle Dissolution
Due to the non-destructive nature of X-rays, particles within a mini leaching cell can be continuously monitored over time and under environmental conditions as to their dissolution behaviors during leaching.
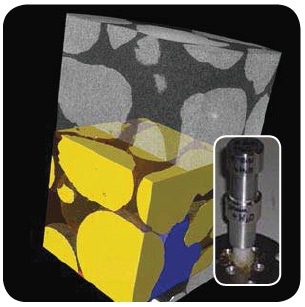
Figure 6. Leaching
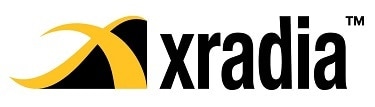
This information has been sourced, reviewed and adapted from materials provided by Xradia.
For more information on this source, please visit Xradia.