For generations, steel has traditionally been used in automotive applications because of its flexibility which allows it meet the diverse requirements of ever-changing vehicle design.
Moreover, thinner grades of advanced high-strength steels (AHSS) exhibit high strength and good formability for intricate shapes, making them competitive to meet the challenges of better fuel economy as well as more complex and intriguing aesthetic and aerodynamic design elements.
As a result, automotive manufacturers are boasting mass reductions achieved by projects such as FSV, ULSAB-AVC, and ULSAB, which showed the far-reaching use of AHSS in light-weighting automotive applications.
Correlation Between Automotive Fuel Economy and Mass Reduction
An fka study, titled ‘Determination of Weight Elasticity of Fuel Economy for Conventional ICE Vehicles, Hybrid Vehicles and Fuel Cell Vehicles,’ analyzed mass savings vs. fuel consumption by taking into account the influence for various vehicle classes, powertrains and driving cycles. The most ideal results are for ICE vehicles.
The result values include a reduction in fuel consumption in the range of 4.5% to 6% per 10% weight saving and a reduction in fuel consumption in the range of 0.15 l/100 km to 0.7 l/100 km per weight saving of 100 kg respectively. These results are obtained from papers which include those presented by the aluminum, steel and automobile industries.
The boundary conditions of statements or measurements are not well defined in the majority of the literature sources. One very useful source was found in a paper by H Wallentowitz. Utilizing a simulation method, the vehicle weight reduction was estimated by taking into account primary and secondary weight saving effects.
The simulations were performed for vehicles with reduced weight, for vehicles with base weight, and for vehicles with reduced weight and re-sized powertrains. All simulations were performed for two driving cycles, five propulsion systems and three vehicles classes using Matlab/Simulink software.
According to a common statistic in the media, a reduction in fuel consumption of 6% to 8% can be achieved by reducing the mass by 10%. The study results conclude that there is a variation in elasticity values between 1.9% and 8.2% based on vehicle size, driving cycle, and choice of powertrains, and whether or not the powertrain is modified for equivalent acceleration for the decreased weight vehicle.
It is possible to obtain weight elasticity values of 6% to 8% by resizing the powertrain for equivalent acceleration utilizing traditional gasoline powertrains. Powertrain resizing has more impact on fuel savings when compared to mass reduction, particularly for urban driving cycles. The following are the reasons for not achieving the impressive fuel economy gains of 6% to 8% in actual vehicle designs:
- Adequate options of engine and powertrain systems are not available with automakers for applying to every incremental step in vehicle weight.
- Data garnered by the European Automobile Manufacturers Association and by the U.S. National Highway and Traffic Safety Administration in its ‘2004 Automotive Fuel Economy Update confirms the significant improvement in engine technology over the past twenty years, but with focus on vehicle acceleration performance instead of fuel economy.
- Instead of powertrain resizing to equivalent performance, acceleration performance is significantly increased due to market forces.
Conclusion
The fka analysis concludes that the applicable value for weight/fuel consumption is in the range of 2% to 4% if the resizing of engine and powertrain system is not achieved. The fka study also takes into account sophisticated powertrains, including fuel cell and hybrid vehicles. According to the study results, the variation in weight/fuel consumption elasticity of these sophisticated powertrains, which leverage regenerative braking, is minimal with powertrain resizing when compared to conventional internal combustion engines. Traditionally, the more commonly stated weight elasticity value of 8% has not been realized. Such a high reduction in fuel consumption has become unachievable due to increasing adoption of hybrid and fuel cell powertrains.
About WorldAutoSteel
WorldAutoSteel, the automotive group of the World Steel Association, is comprised of seventeen major global steel producers from around the world.
WorldAutoSteel's mission is to advance and communicate steel’s unique ability to meet the automotive industry’s needs and challenges in a sustainable and environmentally responsible way. We are committed to a low carbon future, the principles of which are embedded in our continuous research, manufacturing processes, and ultimately, in the advancement of automotive steel products, for the benefit of society and future generations.
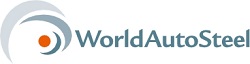
This information has been sourced, reviewed and adapted from materials provided by WorldAutoSteel.
For more information on this source, please visit WorldAutoSteel.