Oct 11 2001
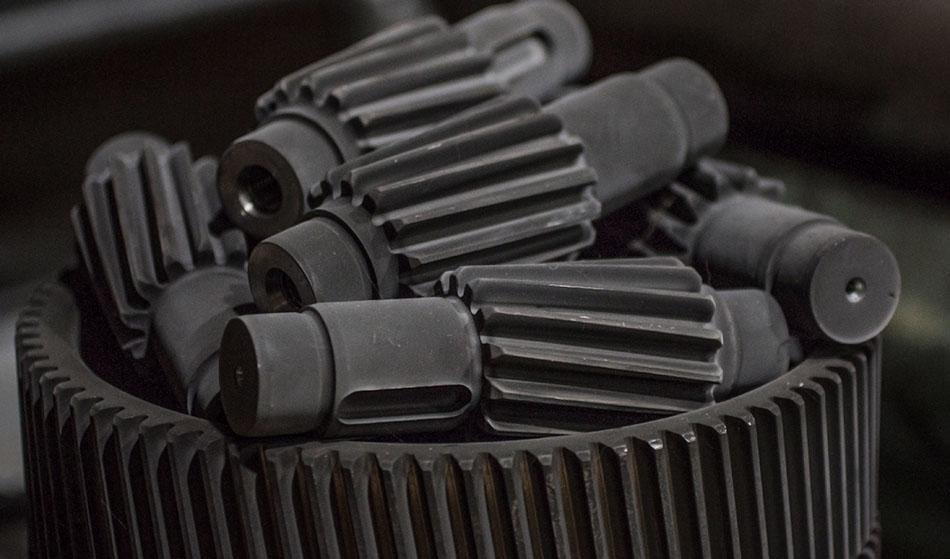
SergeyMarina / Shutterstock
There are several surface coating technologies available for tool steels. Some of them are discussed in this article. These surface coatings are used in applications such as drills, taps, reamers, shank cutters, bore cutters, dies, and milling tools.
Steam Tempering
Steam tempering offers a strongly adhering blue oxide surface, which helps to retain cutting fluid and stop chipping of tool welding, thus preventing built-up edge formation. Steam tempering can be performed on any bright tool but is mainly on taps and drills.
Bronze Finish
A bronze finish is a thin oxide layer coated on the surface of a tool. It is applied mainly to cobalt high-speed steels.
Nitriding
The process of nitriding is used to boost the wear resistance and hardness of the tool surface. It is specifically ideal for taps used on abrasive materials such as bakelite, castings, etc. Nitriding is performed on twist drills when it is necessary to improve the wear resistance and strength of the cylindrical lands.
Hard Chromium Plating
Under particular conditions, hard chromium plating boosts the surface hardness considerably, realizing values of up to 68 Rc. It is particularly useful when tapping structural grade steels, copper, carbon steels, brass, etc.
Titanium Nitride Coating
Titanium nitride (TiN) is a gold-colored ceramic coating applied using physical vapor deposition (PVD). High hardness integrated with low friction properties guarantees significantly longer service life or alternatively improved cutting performance from tools that have been coated with TiN. TiN coatings are used mostly for taps and drills.
Titanium Carbonitride Coating
Titanium carbonitride (TiCN), which is a ceramic coating applied using PVD coating technology, has a lower coefficient of friction and is harder than TiN. Apart from good wear resistance, its toughness and hardness have enabled its wide usage in the field of milling to improve the performance of milling cutters.
Titanium Aluminum Nitride Coating
Titanium aluminum nitride (TiAlN), also referred to as aluminum titanium nitride, is a multilayer ceramic coating applied using PVD coating technology. It has high oxidation stability and toughness, which make it suitable for higher speeds and feed while simultaneously enhancing tool life. TiAlN is ideal for tapping and drilling. TiAlN is recommended for use during dry machining.
TiAlN–X
TiAlN–X is a titanium aluminum nitride coating that combines the most recent developments in the area of surface coating technology. The coating’s high aluminum content in combination with nanometer layering methods guarantees a unique mixture of hardness, high-temperature resistance, and toughness. This coating can be used on milling cutters that are meant to work without coolant and when milling materials have high hardness.
Chromium Nitride Coating
Chromium nitride (CrN) coating is a highly optimal coating for low-alloyed steel materials and aluminum alloys. CrN can also be used as a substitute to nickel and titanium alloys. This coating has a low propensity to form built-up edges. The typical hardness value of this coating is 1750 HV.
Super-R Coating
Super R is a coating meant for use in milling operations. It has high toughness, low internal stress, and high resistance to wear. Due to its high oxidation temperature, the coating also exhibits superior oxidation resistance.
Zirconium Nitride Coating
Zirconium nitride (ZrN) is a ceramic coating applied using PVD coating technology. It features a mixture of properties, making it the most sought after when tapping aluminum and its alloys.
Dialub
Dialub (diamond-like coating) is an amorphous diamond coating with high hardness and a very low coefficient of friction. This coating is particularly made for tapping aluminum alloys with low silicon (Si) content.