The need of highly accurate wavelength measurements necessitates calibration and long-term stability in the measuring instrument. For precise, continuous wavelength measurement, a continuous reference is required and as seen in the article there is a considerable difference between the kind of reference used in different optical measurement solutions.
There are different measuring principles for performing wavelength measurements. Spectrometers, grating-based spectrum analysers and échelle spectrometers all deliver good wavelength measurement results, with accuracies down to 10 ppm.
This level of accuracy is based on a separate calibration process carried before or after the measurements. This implies that the measurement needs high-stability environmental conditions that have to be maintained during both calibration and measurement to achieve the specified accuracy.
In most cases, the calibration is done by the instrument manufacturer under environmental conditions that are completely different from those encountered in the real test environment. This may result in unexpected accuracies especially those due to temperature effects.
Users performing calibration with absorption cells like the SRM2517 need to consider these deviations caused by temperature differences. This kind of calibration is used on grating-based spectrum analysers, and is performed using between one and three reference wavelengths which form the base for a total wavelength correction value.
Applications of New Wavelength Meters
New developments in wavelength meters as shown in Figure 1 now allow multi-wavelength measurements to be carried out with accuracies of 0.2 parts in 106; actual results include 0.3 pm accuracy at 1550 nm (Yokogawa AQ6151) or 1 pm at 1550nm (Yokogawa AQ6150).
.bmp)
Figure 1. The latest generation of optical wavelength meters (Yokogawa AQ6150/6151)
These high accuracies are suitable for a range of applications. In the dense wavelength division multiplexing (DWDM) sector (figure 2), wavelength meters have been used for years.
.bmp)
Figure 2. 100GHz spacing DWDM signal.
Other areas that need the highly stable and accurate wavelength measurements provided by the new generation of wavelength meters include lasers used for spectroscopy, coherence tomography and LIDAR applications, as well as tunable lasers and tunable laser array development and production.
There is a demand for either high bandwidths or reduced channel spacing in the telecommunication area especially in long-distance and metro networks.
Precise laser adjustments that include both the DFB transceivers and transmitter are carried out using wavelength-meter measurements during the tuning process.
Another application for these wavelength meters is in WDM wavelength division multiplexing systems, which in the mid-term are expected to be introduced into the passive optical access network (PON) systems used in FTTH (fibre to the home) and related systems to satisfy the required data rates.
Monochrometer Versus Interferometer
In situations where wavelength accuracy and measurement speed are a high priority, either highly stable environmental conditions are required or a continuous reference measurement is needed during the tests. Michelson-based interferometry offers several benefits as a classic grid-based monochrometer cannot handle a continuous reference simultaneously with the measurement.
A Michelson interferometer-based wavelength meter includes two detectors:
- One to evaluate the reference light
- The other to capture the test signal.
For the test signal, the Yokogawa AQ6150/51 wavelength meters are equipped with InGaAs based photodiodes. The beam splitter and two optical paths as well as a HeNe based reference laser along with the detector.
Both light beams pass through the beam splitter. From there, both signals are diverted into two directions and pass along both optical paths: that of the fixed mirror and that of the movable mirror. The light beams reflected by the mirror will be diverted to the beam splitter again and reflected from there to the photodetectors.
.bmp)
Figure 3. Fabry Perot Laser measurement completed by AQ6151.
An interference signal is created at the detectors which is based on the phase difference between the optical paths that include the fixed mirror and movable mirror.
There is maximum light at the photo detector in case the source has a single wavelength of the phase difference. There is no light at the detector if the signal is out of phase. For the reference photodetector, there is only the HeNe signal. While continuously changing the path differences, the signal is sinusoidal, alternately high and low.
The signal at the reference photodetector is hence used for evaluation of the changing path lengths. A path change of double the reference length wavelength represents one cycle.
This data represents the time information later used to execute the Fourier transformation that is caused by the test signal at the signal photodetector. The benefit of this principle is that the stable reference laser always supports the measurement actively.
Any temperature change that may have an influence on the path lengths is the same for the reference and for the test signal, hence any possible change is automatically compensated. Potential air pressure changes are compensated by mathematical correction using barometer result.
Conclusions
The difference between traditional interferometer designs and the new instruments is that there is no fixed mirror. A mechanical change of one path directly changes the length of the other path in the opposite direction. If one path gets longer, the other gets shorter and vice versa. Using this principle, a much higher sweep speed can be achieved, leading to a full wavelength sweep within 0.3 seconds. This is a uniquely short measurement time achieved by Yokogawa test and measuring instruments.
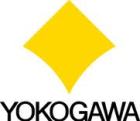
This information has been sourced, reviewed and adapted from materials provided by Yokogawa.
For more information on this source, please visit Yokogawa.