Systems for ground testing and the development of Spacecraft and Components outside of or inside vacuum chambers.
NASA James Webb Space Telescope (JWST)
The 40 ft diameter, vault-like, 40-ton door of NASA's Johnson Space Center’s historic Chamber A was sealed shut on July 10, 2017.
This signified the start of around 100 days of cryogenic testing for NASA’s James Webb Space Telescope (JWST) in Houston. Behind the heavy door, the process of changing the interior of the chamber to suit the frigid, airless environment of space had started.
It took an estimated ten days to remove the air from the chamber. Then, the Webb telescope’s temperature and its scientific instruments were reduced to the levels needed for testing over one month.
The James Webb Space Telescope is the biggest cryogenic instrument telescope to be produced for space flight.
The last cryogenic test of the Optical Telescope Element (OTE) and Integrated Science Instrument Module (ISIM) as an assembly (OTE + ISIM= OTIS) will be carried out in the biggest and coldest vacuum test chamber of its category internationally: the Chamber A at Johnson Space Center.
Chamber A’s temperature will continue to slowly decrease until it achieves around 20 kelvins (minus 424 degrees Fahrenheit or minus 253 degrees Celsius). It will take longer for the Webb telescope and its instruments to attain equal temperatures to what can be achieved in space.
This ultimate evaluation of OTIS, the cryogenic portion of JWST, will be fundamental in proving the end-to-end performance of JWST.
“The James Webb Space Telescope (JWST) is supported by a set of six custom Minus K vibration isolators that utilize Minus K's new thermal compensator device, a passive mechanical device (patent pending), requiring no air or electricity just like our isolators," states Dr. David Platus, president of Minus K and principal inventor of the patented Negative-Stiffness technology.
He continues, "The compensator will adjust the isolators as the temperature changes throughout the testing at JSC, keeping the JWST in the proper position."
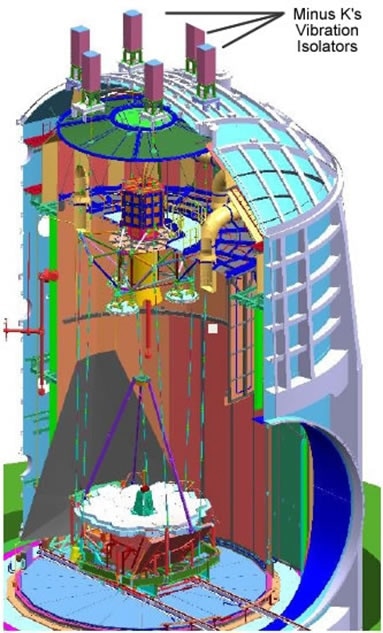
To prepare for cryogenic testing of the Webb telescope, the engineers at Johnson have attached it to the ceiling of the center’s Chamber A. The ‘hammock’ (comprised of six support rods fastened to Minus K Technology's Negative-Stiffness vibration isolators) is not for relaxation. It is designed to isolate the telescope from the vibrations that Chamber A could generate after the door has been closed and testing starts, along with any disturbances that may happen outside the chamber.
The hammock must secure the telescope and its test equipment, including auto-collimating flat mirrors, an interferometer, and a series of photogrammetry ‘precision surveying’ cameras already employed for tests using a surrogate ‘pathfinder’ telescope.
The equipment is in precise relative alignment within the chamber and is isolated from any vibration sources, for example, the rhythmic pulsing of vacuum pumps and the flow of helium and nitrogen inside the shroud plumbing.
“Remember that the system is designed to work in space, where the disturbances are highly controlled and only come from the spacecraft,” explained Gary Matthews, integration and testing engineer at NASA’s Goddard Space Flight Center in Greenbelt, Maryland, responsible for evaluating the Webb telescope while it is at Johnson.
He adds, “On Earth, we have to deal with all the ground-based disturbances, such as the pumps and motors, and even traffic driving by.”
Engineers performed a ‘push test’ with the telescope elevated in the air. The telescope was pushed slightly to record its reaction as a means of ensuring that the suspension system was functioning as optimally as it could, said Matthews.
As the scientific successor to NASA's Hubble Space Telescope, the James Webb Space Telescope will be the most powerful space telescope ever made. JWST’s primary mirror comprises of 18 individual and adjustable segments that will be aligned in space compared to Hubble’s single monolithic primary mirror.
T will launch from Arianespace's ELA-3 launch complex at European Spaceport situated near Kourou, French Guiana, in 2021 aboard an Ariane 5 launch vehicle. Webb is an international project directed by NASA and its partners, the Canadian Space Agency and the European Space Agency.
Heavy Vibration Isolation | Minus K 10,000 lb vibration isolators used on James West Space Telescope
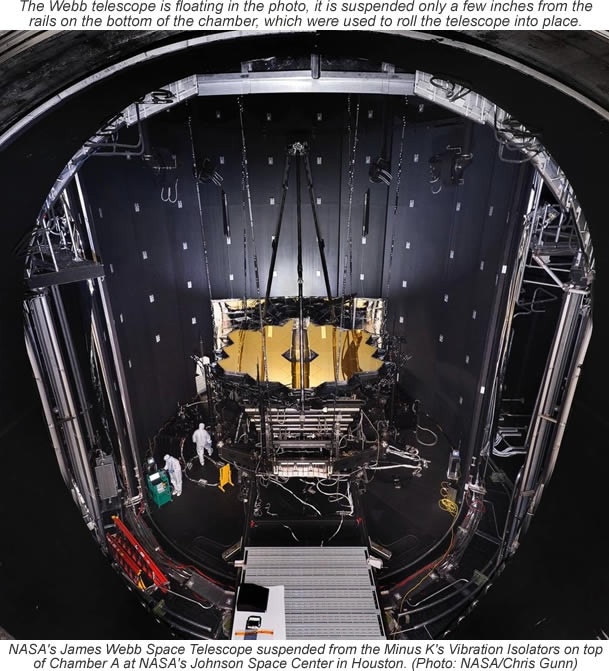
In Chamber A at NASA’s Johnson Space Center in Houston, Texas, the first and second cryogenic optical testing of the Pathfinder was performed along with the testing of the flight hardware in 2017. The Pathfinder is a non-flight model of the Webb telescope’s center section backplane, also called its ‘backbone,’ including the flight spare mirrors.
"Now that the second test is done, it means that all optical test systems have been checked out," described Lee Feinberg, Webb telescope Optical Telescope Element Manager at NASA Goddard.
Dynamics testing will verify that the telescope and science instrument systems will function correctly together in the cold environment of space.
Engineers can continue to observe the Webb while it is undergoing testing. Additional test support equipment such as television cameras, mass spectrometers, and infrared cameras are similarly being supported by the Minus K’s vibration isolators.
The optical test equipment created and installed by Harris (formerly ITT Exelis) in Chamber A in the Johnson Space Center (JSC), is “working out great" said KJ Dziak, Harris Primary Analyst.
He confirmed, “The isolators are down to their 0.5 Hz normal behavior.” Upon recent modifications with the assistance of Minus K, the isolators offered an increase in vibration reduction on the two main mirror segments of the Pathfinder under test.
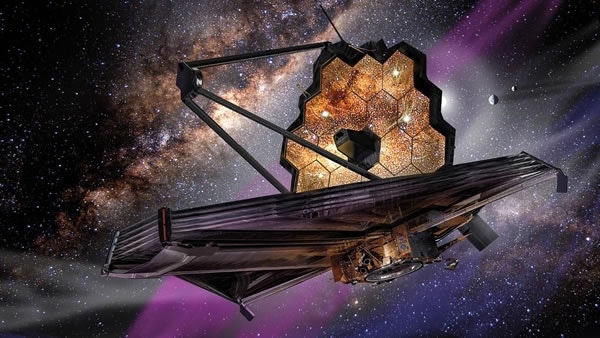
NASA/JPL Space Interferometer Mission System Testbed-3 :
The Space Interferometry Mission (SIM) flight vehicle was designed to be a surveying instrument of the highest precision. It aimed to enable the measurement of stellar positions to a relative accuracy of micro-arc-seconds.
This precision was to be met over a baseline of ten meters between the light-collecting siderostat mirrors. Measuring distances to the target star are required to achieve accuracies on the order of 50 pico-meters.
The SIM System Test Bed 3 (STB3) was created to show that the active optics and vibration isolation systems would function together to meet the goals for dynamic stability.
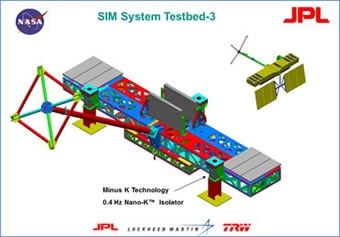
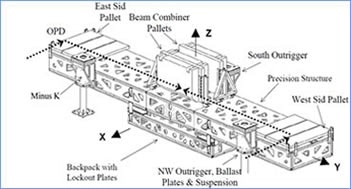
A dual-stage passive isolation approach was suggested, where isolation was used first at the vibration-inducing reaction wheels, and a second isolation layer between the optical payload and the bus portion of the space vehicle, ‘the backpack’.
The dual-stage isolation approach was presented on a 7 m, dynamically feature-rich structural testbed (STB3). A novel passive suspension that excludes ground vibrations over 0.4 Hz had been included in the testbed.
The STB3 suspension employed Minus K's Nano-K mechanical vibration isolators produced by Minus K Technology (previously sold under the trade name Nano-K.)
Three isolators were located underneath outriggers from the structure symmetrically around and slightly above the structure’s mass center in a horizontal plane to provide stability. The natural frequency of the system was 0.4 Hz, horizontally and vertically.
The Minus K isolators employed negative-stiffness mechanisms to alleviate the stiffness of traditional support springs, generating the low vertical stiffness. An optical-mechanical servo system upholds a vertical position within a +/- 0.010-inch deadband by modifying the force on a small control spring.

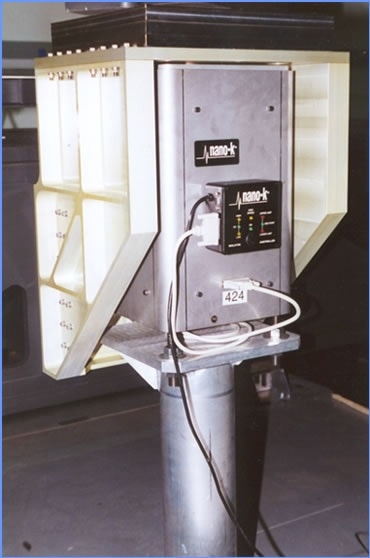
The servo system was created to cope with small changes in load, long-term creep of the support springs, and temperature changes.
Transmissibility measurements were carried out for the complete STB3 structure to establish whether the stability aims are being met. The NASA Inventions and Contributions Board awarded a NASA Tech Brief Award to Minus K for their contribution to "Dual Stage Passive Vibration Isolation for Optical Interferometer Missions."
Ball Aerospace & NASA/JPL Spitzer Space Telescope's Cryogenic Telescope Assembly (CTA) :
Part of NASA's Great Observatories Program, the Spitzer Space Telescope was utilized to investigate objects deep within the Solar System and beyond. It initially launched in 2003 and finished its hot missions in 2009.
The Spitzer Space Telescope employed infrared light to capture spectra and images by detecting the infrared energy, or heat, radiated by space objects between wavelengths of 3 and 180 microns.
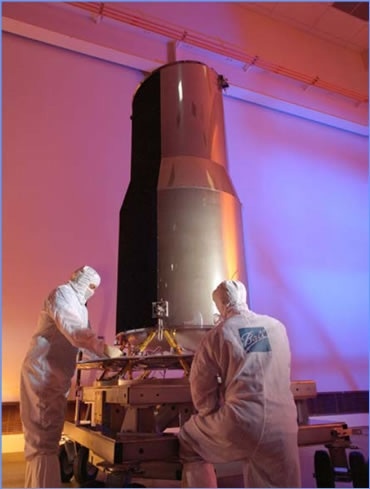
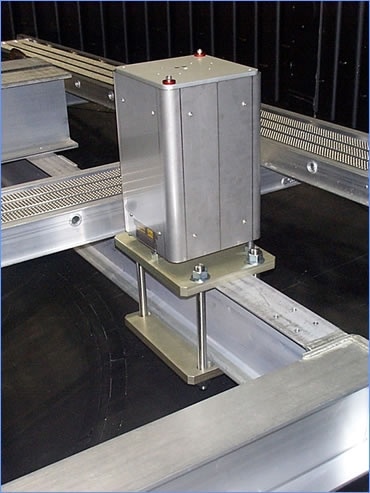
The Spitzer Space Telescope recorded those celestial phenomena and objects that are too faint, cool, or distant to be analyzed by alternative astronomical techniques.
The Spitzer Space Telescope (SST) project decided early in the program that an end-to-end thermal and optical performance test condition under thermal conditions similar to flight would be needed to ensure that the Cryogenic Telescope Assembly (CTA), which contained a superfluid helium cryostat and the telescope, would attain the level-one performance specifications during flight.
The system of end-to-end tests on the CTA during operation at temperatures close to absolute zero were performed at Ball Aerospace's Boulder Colorado large thermal vacuum test chamber called 'Brutus'.
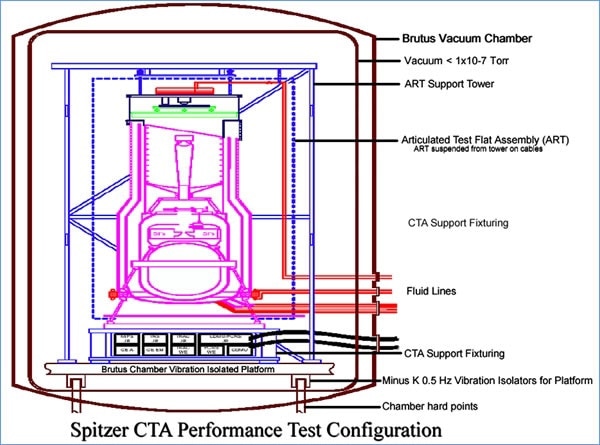
Ball Aerospace chose the 0.5 Hz vacuum-compatible negative-stiffness vibration isolation system from Minus K due to the test chamber's horizontal low-frequency vibrations at around 4.5 Hz.
The Minus K isolation system comprised of three customized 1000 lb-capacity vacuum compatible isolators that offered a horizontal natural frequency of 0.5 Hz.
Materials were chosen to attain a vacuum level of around 10 to 7 torr. To ensure that the isolators did not have to cope with the temperature extremes of the test, they were thermally isolated and heated.
The jitter in the focus mechanism, an essential parameter for the CTA, was shown to be correctly within the requirements with the use of Minus K’s vibration isolators.
NASA/JPL SIM Interferometer Testbed Spectral Calibration Development Unit (SCDU) :
The Spectral Calibration Development Unit (SCDU) was designed to show wavelength calibration stability and accuracy between sources of various polarization and color.
SCDU was employed for the strict astrometric performance standards on NASA's SIM (Space Interferometry Mission)-Lite mission that was derived from the Narrow-Angle (NA) observing scenario. SIM-Lite was a space-borne stellar interferometer able to look for exoplanets similar to Earth in the habitable zones of stars close by.
SCDU was produced to demonstrate the chromatic effect noticed by SIM-Lite, which could be calibrated to the sub-micro arcsecond degree.
SCDU mainly comprised of a white light interferometer with a real-time control system and a metrology system representative of the science interferometer. SCDU came online in 2006 and developed its first results in 2007.
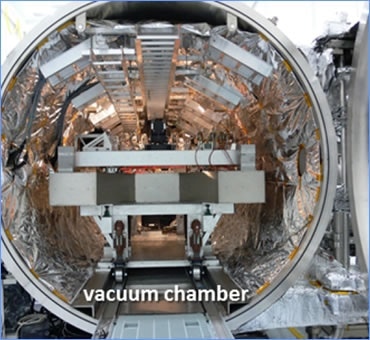
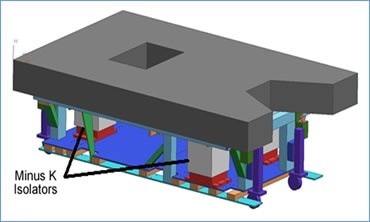
The Spectral Calibration Development Unit (SCDU) SIM Lite performed calculations of the external delay differences between pairs of stars. The differences in spectral energy densities between the two stars pair with the instrument wavefront error and instrument optical dispersion to create a delay error dependent on wavelength.
The differential material dispersion between the optics of the two arms was the source of the instrument optical dispersion, while the instrument wavefront error is a result of the differential wavefront error between the two arms.
SCDU successfully showed the calibration of spectral instrument error to an accuracy of greater than 20 picometers. This performance is in line with the one micro-arc second narrow-angle astrometry.
SCDU calibrated and measured simulated spectral sources in the range of 450 to 950 nm. The light sources have the purpose of simulating the spectral energy differences between F, G and K stars.

For the Space Interferometry Mission (SIM), the SCDU testbed employed wideband white light to simulate starlight. The white light source mount needed an incredibly stable level of pointing accuracy.
This was met with the utilization of Minus K's negative-stiffness vibration isolators beneath the SCDU testbed. The Minus K isolation system comprised of three tailored 1350 lb capacity, vacuum compatible isolators that offered vertical and horizontal natural frequencies of 0.5 Hz.
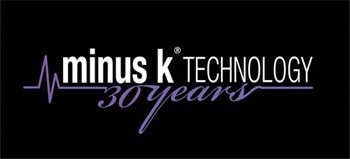
This information has been sourced, reviewed, and adapted from materials provided by Minus K Technology.
For more information on this source, please visit Minus K Technology.