The question of whether to machine or die-cast during production usually comes down to cost, especially as advancements in die-casting technology now mean there’s little to separate the two disciplines. Engineering has developed to the point that tight-tolerance features no longer require multiple machining operations, which can therefore reduce the manufacturing costs of metal components.
Cutting production costs should never sacrifice on the component’s quality though and below, Dynacast offers some top tips for maintaining quality whilst reducing costs.
Reducing Production Steps with Die-Casting
Die-casting isn’t suitable for every type of component, especially if you are only producing a low volume of parts or if you are looking to cast with an unusual metal.
Many parts can be die-cast though, for example, if a company requires a two-piece design which would need three machining steps, then die-casting this product instead can uphold the two-piece design without the need for machining prior to assembly. Reducing the amount of machining steps through die-casting can cut manufacturing costs.
Die-Casting Surface Details
Many components feature detailing on the surface, in many cases this is to improve grip such as with hand tools, razors and weight training equipment or to add decoration, for example company logos or even vital information such as part numbers.
Often this detailing has to be machined on separately through knurling or engraving for example. However, in many cases, these details can be die-cast onto the metal’s surface which greatly reduces production time and cost as it eliminates an entire step in the production process.
Costs of Die-Cast Tooling
Die-cast tooling is often regarded as the biggest cost, and consequently the biggest drawback, of the die-casting process. In many circumstances though, the increase in production and the robustness of today’s moulds can mean that the cost of tooling can soon be recovered.
This is especially true when you consider that many machined parts might require jigs or fixtures which can be expensive, plus there’s the costs of labour associated with the handling and set up of machined parts to take into account.
Through a rigorous planning and testing process, it’s simple to see if die-casting would be a cost and time effective solution to your manufacturing process.
Author Bio
Mike Brettell is Managing Director at Dynacast UK, die-casting experts and global manufacturers of metal components.
About Dynacast
Dynacast International is a global manufacturer of small, engineered metal components. Utilizing proprietary die cast and metal injection molding technologies, they offer robust solutions to companies in automotive, consumer electronics, healthcare, hardware, computers and peripherals and many other industries.
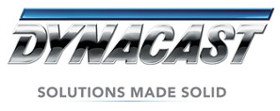
This information has been sourced, reviewed and adapted from materials provided by Dynacast UK Ltd.
For more information on this source, please visit Dynacast.