Thin Film Deposition is a vacuum process to apply coatings of pure materials over the surface of many different objects. The coatings or films typically have a thickness range of microns and angstroms and can be of single material or multiple materials in a layered structure. This article covers the basic principles involved in controlling the thickness and rate of Thin Film Deposition by means of quartz crystal monitoring, especially discussing co-deposition and multi-crystal systems for PVD by evaporation.
Quartz Crystal Monitoring
The key concept of this type of measurement and control involves mounting of an oscillator crystal within a vacuum chamber in order to receive deposition in real time and the crystal is affected by the deposition in a measurable way. There will be a drop in the oscillation frequency when there is an increase in the mass of the crystal caused by the material being deposited onto this material.
The changes in the oscillation frequency is continuously recorded by an electronic instrument, which then converts the frequency data into Thin Film Deposition thickness data by performing appropriate mathematical functions. The data includes both instantaneous rate and cumulated thickness.
Such sensors and devices are readily available in the market, including many different integrated models which not only monitor and display the thickness and rate data, but also give outputs for control functions of Thin Film Deposition systems. Although features differ model by model, most of the systems are capable of handling multiple independent crystal oscillators and some are also capable of controlling multiple simultaneous sources.
A majority of the Thin Film Deposition systems feature only a single source operating at a time, even though such things like multi-pocket E Beam sources are capable of having many different materials available for sequential selection and usage to create a multi-layer film. Nevertheless, multiple crystal sensors can be positioned around the chamber to average their signals for better control.
Advantages of Having Multiple Crystals over Single Crystal
The problem with the use of a single crystal is that when it assumes the proper thickness has been reached, it will stop the Thin Film Deposition process by closing the shutter. Hence, the chance of achieving the same average thickness across the substrate is very limited.
To handle this problem, several crystals can be mounted in locations to acquire signals from all locations and average them out for the control function. This can be performed by controller models.
Even a single crystal has details to address, such as calibrating its thickness readings. Nevertheless, it can monitor only the Thin Film Deposition that lands directly on itself. However, this is not actually what a user wants to understand or to control.
What is on the substrates is the subject of interest to users. Hence, it is necessary to perform physical measurements to compare to the crystal reading and to calculate and program a calibration factor (generally called ‘tooling’ factor) into the instrument for subsequent verification. With multiple crystals, this becomes a requirement to be performed for each of them, providing the option of ‘weighting’ them so that one sensor is relied on more heavily than the other.
Co-Deposition Control
It is possible to carry out co-deposition by simultaneously operating two sources to form a blended layer of two materials. There are undoubtedly some changes being made in such a system.
For instance, two E Beam guns in a chamber cannot share the same physical space and cannot both be in the perfect position in the center of the chamber - a design consideration for Thin Film Deposition equipment. However, for co-deposition control, each source must have its own crystal sensor, and preferably, neither sensor must be able to ‘see’ the other source to avoid cross talk between them, which leads to loss of control accuracy.
Hence, it is necessary to include physical shielding to the sensor mounting to have a clear view of its intended source but no line of view to the other source. Generally, some shielding is probably required to prevent cross contamination of materials and to avoid magnetic interference in the case of E Beams. After addressing all these problems, an appropriate crystal control system with the right capability and an appropriate chamber with two sources, co-deposition has some key concerns in terms of film programming.
There is a possibility that the pre-conditioning phase, and ramp and soak settings for the two materials will be different. Nevertheless, the total time must be the same otherwise one shutter will open prior to the other, causing the film to begin in single material mode instead of co-deposition.
The crystal controller is generally all thickness based. Hence, if mass is required instead then it should be take into consideration. Moreover, it is necessary to maintain the same rate ratio right through the process as the final thickness ratio; otherwise the closing of the shutters will not take place at the same time at the end, resulting in the ceasing of the co-deposition when one closes.
Irrespective of process type, whether single layer, multi-layer, or co-deposition, there is always a possibility for a crystal failure in the event of a Thin Film Deposition run. The sensor head of some models can hold one or more spare crystals, which allows them to automatically change over to a new crystal in the event of a crystal failure if the function is also supported by the controller.
The controller would consider the last known data point of power drive level, deposition rate and cumulated thickness at the event of a crystal failure and blindly maintain the same power drive and assume the same constant deposition rate to achieve the preset final thickness and then trigger shutter closing.
Conclusion
Various other factors need to be considered in the event of scrapping all substrates. In that situation, it might be better to take a chance on ‘time-power’ to rescue them. There are many more features of quartz crystal monitoring and control of Thin Film Deposition and any additional information can be obtained from instrument user manuals. By all means, quartz crystal control is a very useful PVD technology.
About Semicore Equipment
Semicore is a manufacturer and worldwide supplier for the electronics, optical, solar energy, medical, automotive, military and related high technology industries.
Our high-performance production or R&D vacuum sputtering and thin film evaporation systems provide coatings on a variety of materials including plastic films, glass, ceramics, metals and hybrid substrates.
Whether you want to take advantage of our proven industrial solutions for vacuum system automation, process control and supervisory monitoring applications or need to develop some unique new application of your own design you will find Semicore’s staff and facilities to be competent, open-minded and eager to help.
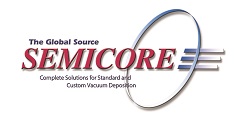
This information has been sourced, reviewed and adapted from materials provided by Semicore Equipment.
For more information on this source, please visit Semicore Equipment.