Considerable support is needed when streamlining, developing and accelerating the evolution of successful process designs. With on-line particle size analysis as an example, this article considers the rationale for investment in real-time measurement for pilot scale work.
Real-time process analysis systems are often used within the manufacturing environment, and operational variability and its related inefficiencies are considerably reduced by automating analysis and control. Automation can pay considerable dividends by improving product quality and at the same time reducing the production cost. Installation costs are offset by these savings, strengthening the economic argument in favor of an investment.
It may be less easy to make the financial case for automation at the pilot scale. In this case potential benefits may not be obvious immediately and may be more difficult to quantify, but are nonetheless considerable. The scope for highly consistent operation and the effective correlation of cause and effect, accelerates and improves product and process development alike, enabling faster and more efficient commercialization.
Pilot Plant Trials
When a product passes from early stage research to commercialization, a robust process needs to be developed that will secure profitable, consistent production over the long term.
Often pilot scale trials play a significant role. Operating small scale units that replicate part or all of an existing or proposed full-scale plant is a relatively inexpensive way to experiment with the best processing solution.
Pilot scale trials are actually a significant expenditure, but when compared to a proposed full scale plant it is relatively cheap. They are also an upfront investment, rather than immediate reward.
While considering the contribution that can be made by real-time analysis, it is worth examining the goals of a pilot scale study, which might include:
- Identification of the most cost-effective process design
- Proving the feasibility of a new technology
- Preparing representative samples for product testing
- Defining the process operating envelope; the range of conditions that will result in product that meets the defined specification
- Developing an effective control strategy
The pilot scale may follow from basic lab work developed to prove the viability of a product. One may not know much about the feasibility of several manufacturing options and it is important to learn fast.
The Role of Real-Time Measurement
Pilot plant control is eased by the real-time measurement of key process or product parameters leading to increased experimental efficiency. Let us consider an example of a trial developed for the establishment of optimal milling conditions. While milling, the particle size is a defining characteristic of the product, hence it is beneficial to examine what happens while using periodic particle size measurement compared with applying real-time analysis.
Off-line periodic analysis offers a snapshot of the process every time a sample is taken. Material is extracted from the plant, analyzed and the results are provided after some time. The time lag between sample extraction and the return of results cannot be avoided.
Returning to Milling
Consider the following example: a mill parameter is changed and there is an instant impact on exiting particle size. The sample is taken from the work stream, worked up and the results are observed an hour later. Assessment of the impact of the initial change is enabled by careful correlation.
It may prove essential to take several samples to accurately quantify the result. Also, in the case the mill does not operate smoothly, it may be difficult to differentiate the effect of the change from baseline steady state variability.
There are several advantages of continuously monitoring the particle size of the exiting material instead, which are outlined below:
- Since the operator is able to observe how the plant is running, it can be operated with greater smoothness, establishing an improved baseline for experimentation.
- Consistent steady state operation makes it easy to provide representative material for product testing.
- As soon as a change is made the results are immediately obvious.
- Cause and effect can be quantified rapidly in a statistically relevant way and the experimentation rate is solely limited by the dynamics of the process, by how long it takes changes to filter through the plant.
- It is possible to move the unit swiftly and efficiently from one experimental condition to another, and the results of each experiment are captured rapidly and completely.
Conclusion
This capability of real-time measurement to offer steadier pilot plant operation, and accurately capture even the subtle effects of a process change, can accelerate and improve work, and also enhance confidence in the resulting solution.
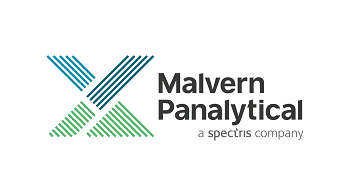
This information has been sourced, reviewed and adapted from materials provided by Malvern Panalytical.
For more information on this source, please visit Malvern Panalytical.