Mass spectrometry is a powerful tool for process automation. Fast and accurate gas analysis allows for high-precision reactor control and better production efficiency.
Based on advanced quadrupole mass spectrometer technology, the MAX300-RTGTM enables continuous online gas monitoring for industrial process control. The instrument has the speed needed to study the total composition of a sample in a fraction of seconds, and can be fully automated to determine a number of points in a process, or multiple production lines, with just a single analyzer.
Industrial Process Gas Analyzer Features
- Control parameters reported in real-time
- Automated online analysis and data delivery
- High accuracy and precision for excellent process control
- Complete quantitative stream composition
- Low maintenance, calibration, and utilities needed
- Multiport sample systems for up to 160+ sample streams
- Complete method scale-up - Lab, Pilot, Production
An ionizer is used by the mass spectrometer to break sample molecules into charged fragment ions. These ions are subsequently separated depending on their mass-to-charge ratio as they travel through the electric fields produced by the quadrupole mass filter. The ions then register a current at the detector, generating a set of peaks known as mass spectrum. Each compound possesses a unique spectrum, making mass spectrometry a flexible and highly selective technique.
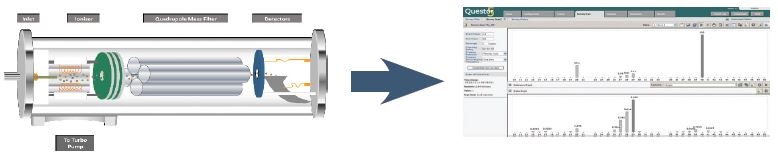
Image Credit: Extrel
The MAX300’s industry-leading 19 mm quadrupole mass filter, coupled with advanced electronics, provides users with an extraordinary list of Extrel advantages:
- Uniform resolution across the entire mass range for ultra-high sensitivity to all compounds
- Near-zero mass scale drift for unparalleled measurement precision and stability
- Performance specifications that surpass those common to other mass spectrometers and process technologies
- Excellent resistance to contamination and corrosion for continuous, long-term, low-maintenance operation
Reliable Data, Durable Performance
Extrel has more than 40 years of excellence in industrial automation, with thousands of global installations to its credit. The company’s process mass spectrometers provide the ease-of-use and rugged stability required for nonstop operation in challenging manufacturing environments.
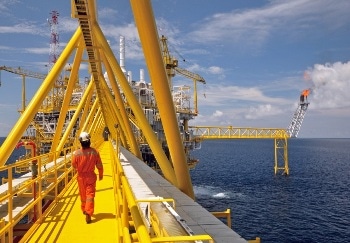 |
Hydrocarbon Processing
- Polyethylene
- Ethylene Cracker Control
- Ethylene Oxide
- Fuel Gas BTU
- LNG
- Benzene
- PVC and EDC
|
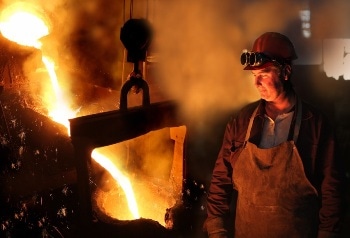 |
Metals Manufacturing
- Blast Furnace Off Gas
- Steel Carbon Content
- EAF Monitoring
- Coke Making
|
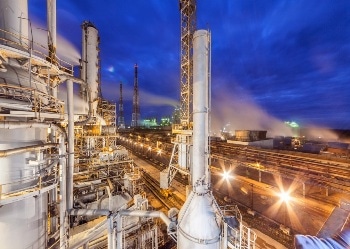 |
Syngas Manufacturing
- Methanol
- Ammonia
- Gasification
- Hydrogen
- Low-Sulfur Diesel
- Acetic Acid
|
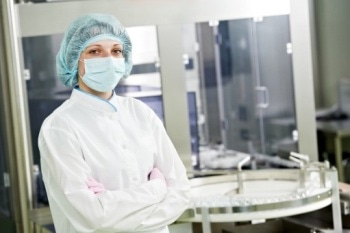 |
Gas Purity
- Pharmaceutical Solvents
- Trace Contamination
- Semiconductor Manufacturing
- Food and Beverage Gas
- Scrubber Efficiency
|
Rapid Online Analysis to Maximize Your Production
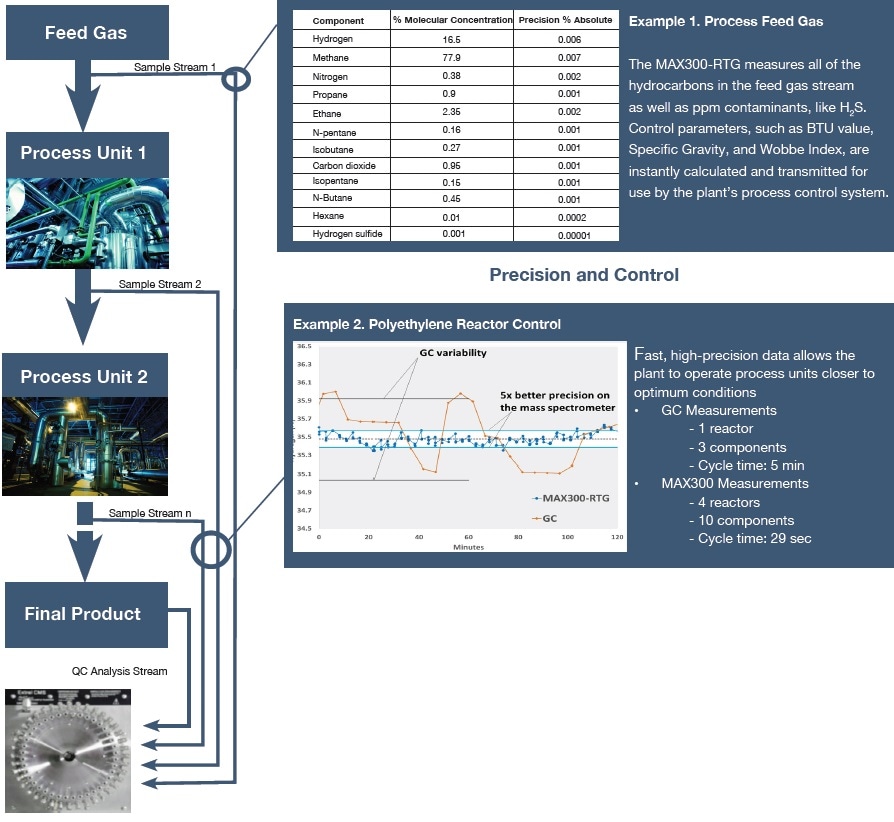
Image Credit: Extrel
The 80 Port FASTvalve Sample Selector
MAX300-RTG’s inlet system can be configured with any number of zero-dead-volume sample selector options.
Consistent Ongoing ROI
- Fast online gas analysis for better manufacturing efficiency, equipment uptime, and product yield
- Reduced operation costs due to low maintenance and utility requirements
- Lower capital cost compared to other technologies
- The full stream composition offers extra information required for Advanced Process Control
- By monitoring the operation of a number of process units, the MAX300-RTG is generally used to substitute multiple gas chromotograph (GC) systems
System Specifications:
- Detectable compounds: Any gas or vapor sample
- Detection range:
- Faraday detector: 100% - 5 ppm
- Electron multiplier: 100% - 5 ppb*
- Membrane inlet: 100% - 10 ppt*
- Number of sample streams: 16, 31, 40, 80, 120, 160+
- Analysis rate: 0.1 - 16 seconds per component
- Number of components: Unlimited
- Number of analysis routines: Unlimited
- Number of user configurable data tags: Unlimited
- Precision: <0.05% RSD over 24 hours**
- Stability: <0.5% RSD over 30 days**
- Filaments: Two, one active and one spare with automatic switchover
- Analyzer maintenance: 1-3 years†
- Roughing pump: 6-12 months†
- Manual or fully automated calibration and validation
- 3-12 month calibration intervals
- Mass range options: 1-250, 300, 500 amu
* Matrix dependent. Documented on trace air components and benzene.
** Based on the analysis of 1% argon, scan speed 1 second per analysis.
†Application dependent.
Low Maintenance, Easy to Use
The Questor5 control software that powers the MAX300-RTG system measures all sample points in a fully customizable sequence for automated, site-specific production control. With the intuitive web-based interface, users can review data, check instrument status, or run a validation sequence from anywhere on the plant network, and at the same time can maintain industry and government security standards for login and electronic record keeping (21 CFR 11).
The MAX300-RTG is a 24-7 online gas analyzer with a documented uptime >99%.
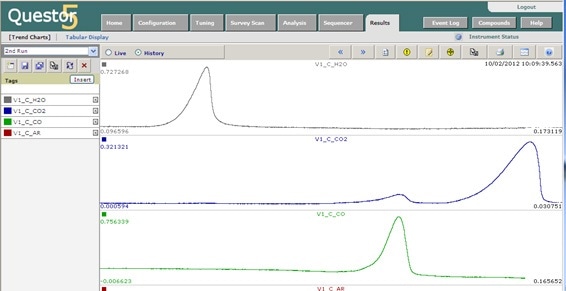
Image Credit: Extrel
Using the user-friendly Questor5 control software, users can simultaneously trend high precision measurements of bulk components and ppm-level contaminants.
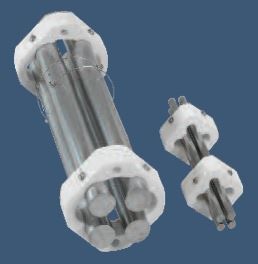
Image Credit: Extrel
Extrel’s 19 mm quadrupole is seen next to a common 6 mm filter. The larger device offers greater ion transmission for unmatched sensitivity and signal stability.
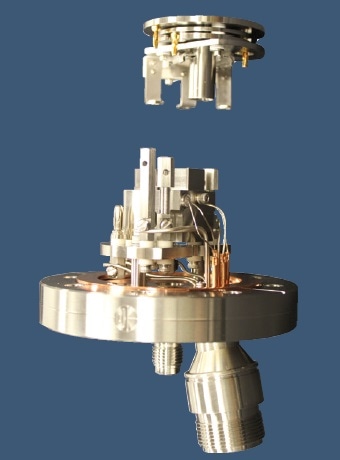
Image Credit: Extrel
The MAX300 disposable, plug-and-play ionizer contains dual filaments — one active and one spare, and eliminates the cleaning requirement.
MAX300-RTG System Specifications
Power Supply Options:
- 110 VAC, 50/60 Hz, Two 15 Amp circuits
- 230 VAC, 50/60 Hz, One 20 Amp circuit
Power Consumption:
- Nominal 2740 Watts
- Heat Load: 2700 Watts (9215 BTU/h)
Weight:
- Standard Enclosure: 450 lbs (205 kg)
- Optional cart: 40 lbs (18 kg)
Ambient Requirements:
- Temperature: -4 °F to 120 °F (-20 °C to 49 °C)
- With A/C, cold start =54 °F (12 °C)
- Area Classification Options:
- General Purpose
- Class 1, Division 1 or 2, Groups B, C, D, T4
- IEC/ATEX, Zone 1 or 2, Group IIC or IIB +H2*, T4
Additional Utilities:
- Purge gas (for hazardous area installations)
- Base calibration requirement: 2 gas bottles
Data System and Communications:
- System control interface options: Ethernet, RS-422 4-wire
- Login security levels: Administrator, User, Viewer
- External communications:
- Ethernet, Modbus serial, digital I/O, analog I/O, OPC
* Configuration dependent
![MAX300-RTG enclosure with A/C, Cart and X Purge Options. Dimensions shown in inches [mm]](https://d12oja0ew7x0i8.cloudfront.net/image-handler/picture/2017/4/PPP-1f2.jpg)
MAX300-RTG enclosure with A/C, Cart and X Purge Options. Dimensions shown in inches [mm]. Image Credit: Extrel
Exceptional Worldwide Service and Support: For more than five decades, Extrel has been providing the highest quality support services for infinite number of instruments deployed across the world. Certified and factory trained personnel at Extrel provide industry-leading support to customers at all stages of process development and manufacturing.