The in-line multi-channel liquid particle measuring system from FlowVIEW Tek fully maintains the data precision of micro-particles, optimally improves the process yield, and considerably reduces the costs related to quality control.
- The multiple channels can be automatically switched based on a customized recipe
- Microparticles and nanoparticles can be monitored in real time and a continuous flow (size and volume)
- Smart assembly line with quality record tracking
- Modifiable scheduling and alarm system
Applications
- Inline monitoring water purification system and wafer cleaning process—estimates yield by examining the micro-particle and nanoparticle counts resulting from the front-end and back-end processes
- Recording efficiency of the purifier and computing the lifetime of filter element—waste and residue of the cleaning chamber can be tracked. Filter element replacement schedule can be revised based on particle size and contamination level of the process.
- Can be applied to chemical liquid or deionized water—effectively ensure maintenance scheduling, such as chamber cleaning, consumable replacement, etc., to improve yield and cleanliness
Features
FlowVIEW Tek is well aware of the fact that the purity of chemical liquid and deionized water is crucial to the wafer cleaning procedure. Customers can seek the company’s help to stay on top of the most accurate micro-particle data.
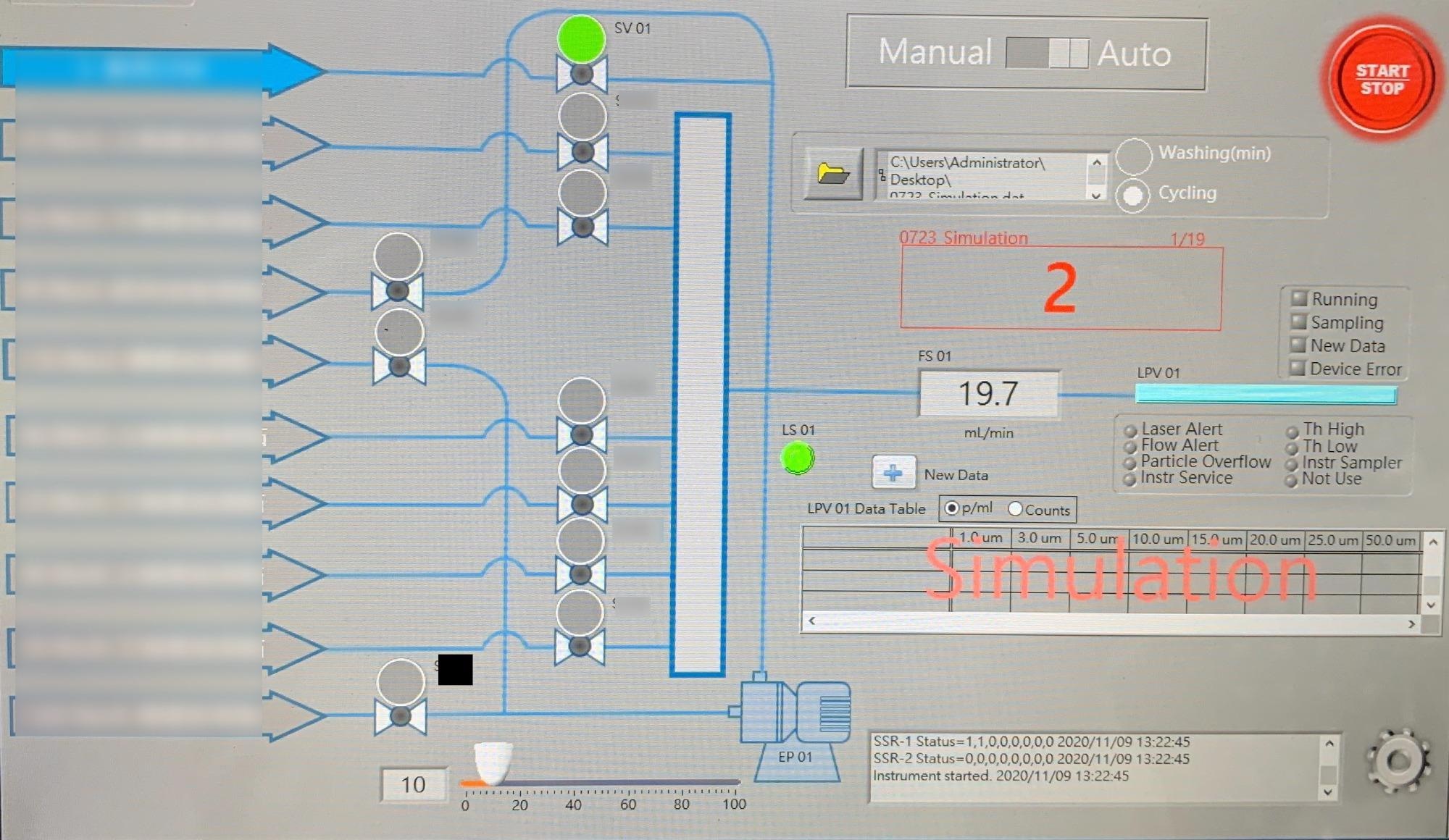
Particle Counting Program. Image Credit: FlowVIEW Tek
With the precision multi-channel and advanced laser induction technology, FlowVIEW has designed the multi-channel liquid particle measuring system that can fulfill the needs of wet processes in semiconductor industries.
The novel technology can be incorporated into an online machine and numerous sampling points. It can examine chemical liquids and deionized water 24 hours per day, but without causing any kind of disruption to return real-time data.
Users can now effortlessly understand the variations of micro-particle counts and effectively track the water quality and treatment tank, and most significantly, considerably increase the efficiency of component cleaning procedure.
Source: FlowVIEW Tek
. |
. |
Measuring Range |
0.03 µ.m~50 µ.m |
Tolerance in Measurement |
5% Coincidence Error |
Calibration |
NIST-Traceable |
Communication mode |
RS485/Modbus, 4~20 mA |
Materials of Outer Box/Tube/Sampling Interface |
Stainless Steel/ PFA/ Quartz |
LED Signals |
Power/Error/System Normal/ Problem Detected |
Sampling Temperature/Pressure |
0-70 °C / 150 PSI |
Size/Weight |
50 (L) x 42 (W) x 104 (H) CM / 60 KG |