In the industries involving pumping mechanics, such as chemical, oil, gas and hydrogen, magnetic couplers are a crucial component in cutting-edge sealing systems. The main component, in this case, is containment shells composed of zirconia advanced ceramics. Ceramic materials possess unique non-magnetic properties combined with corrosive resistance and high bending strength under high pressure both in high and low temperatures.
The Kyocera sales and engineering team has deep technical knowledge and collaborates closely with its customers to design customized solutions that meet their specific requirements.
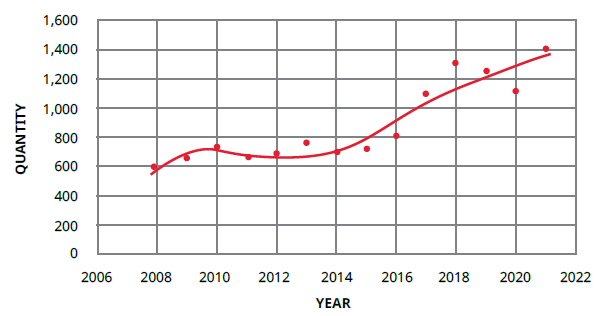
Development of unit sales ceramic containment shells. Image Credit: Kyocera International, Inc.
Technical Ceramics from Kyocera
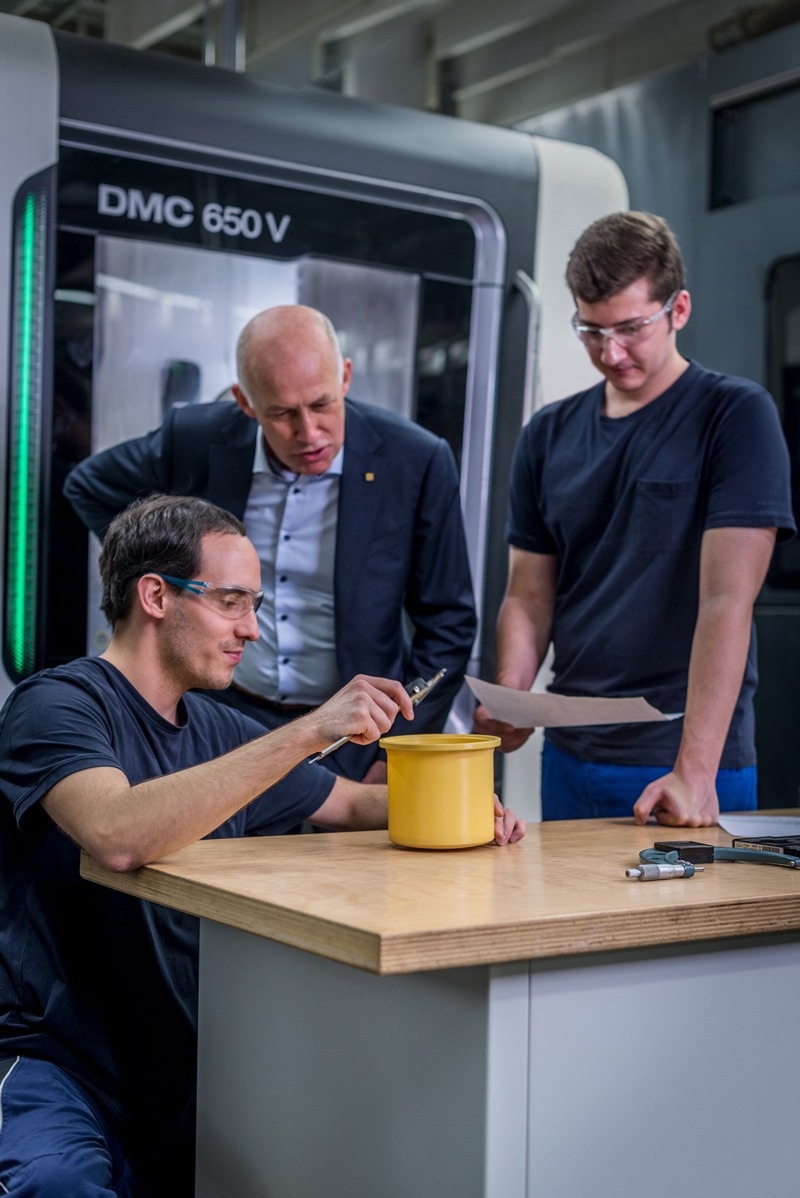
Image Credit: Kyocera International, Inc.
Magnetically coupled centrifugal pumps and permanent magnet motors require non-magnetic components that can withstand high mechanical forces and do not heat up in rapidly rotating magnetic fields. Furthermore, these components must be corrosion-resistant when exposed to aggressive media. High-performance ceramics are the optimal choice for meeting this unique set of requirements.
Magnetic couplers guarantee a hermetic seal between the pump impeller and the drive, ensuring a leakage-free operation with minimal maintenance needs. This feature not only prevents any environmental impact caused by spilt pumping media, but also enhances the overall efficiency and reliability of the system.
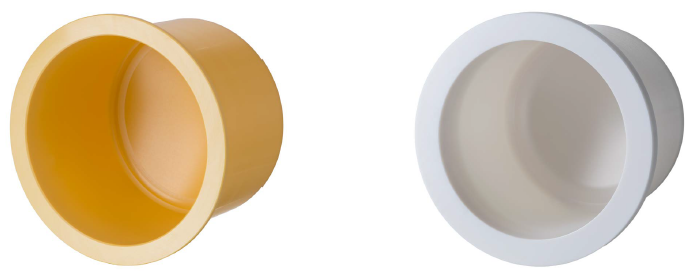
Image Credit: Kyocera International, Inc.
High-performance ceramic containment shells offer several advantages over traditional materials such as metal or plastic.
- Zirconia's non-conductive properties help to prevent eddy currents, leading to increased energy efficiency. This can result in a reduction of electrical drive power by 10% to 15%. Additionally, the avoidance of eddy current losses can prevent up to 20 kW of excess heat from being generated, which could pose a risk by heating sensitive pumped medium and interfering with bearing lubrication. It is crucial to avoid adding heat to substances that are close to boiling or are explosive. By utilizing ceramics, the potential for boiling, dry runs, or deflagrations can be minimized.
- Zirconia offers high mechanical stability, allowing for pressure settings up to PN 63 bar at temperatures ranging from -200 °C to 450 °C and beyond, depending on the diameter size.
- Zirconia’s corrosion resistance makes it suitable for use with a wide range of acids and bases.
A relatively small elastic modulus guarantees a specific amount of elastic deformation capacity.
To minimize the magnetic split, the wall thickness in the cylindrical section of the containment shell varies between 1.5 mm and 3 mm, only – again, depending on the inner diameter.
The relatively small elastic modulus of zirconia ensures a specific amount of elastic deformation capacity, which is crucial for working in higher pressures and providing high impact resistance necessary for handling and assembly. In order to minimize magnetic split, the wall thickness in the cylindrical section of the containment shell varies between 1.5 mm and 3 mm, depending on the inner diameter.
Thanks to these characteristics, containment shells made from advanced ceramics for magnetically coupled pumps are ideal for a wide range of applications in the chemical, oil and gas, as well as hydrogen industries. The design of the containment shell can also be customized to fit the specific pump type.
The optimal design of transitions and radii in containment shells, leading to the dished end and flange base, allows for a reduction in wall thickness. This results in a more cost-effective selection of magnets used in the system.
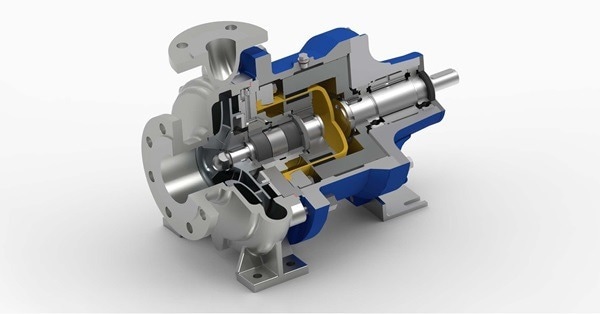
Image Credit: Klaus Union
Zirconia FZM and FZM+
FZM ceramics is now recognized as an excellent ceramic material known for its exceptional resistance to wear, high corrosion resistance, and impressive fracture toughness. In addition to these qualities, FZM ceramics also boasts low thermal conductivity, thermal shock resistance, and outstanding thermal expansion properties comparable to cast iron.
The potential applications of this material can be further broadened through the ongoing development of the new zirconia material, FZM+. This advanced material is characterized by its improved flexural strength, excellent fracture toughness, and new white color. These features allow for testing pressures of up to 95 bar (pressure rating PN 63) within a temperature range spanning from -200 °C to over 450 °C.
As a result, FZM+ is suitable for use in cryogenic applications and external pressure applications, particularly in containers where gas is utilized as the medium.
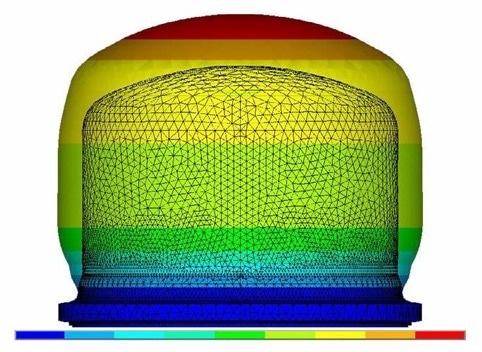
Global deformation (50-fold stilted presentation). Pressure: inner pressure 36 bar, inner temperature 250 °C. Image Credit: Kyocera International, Inc
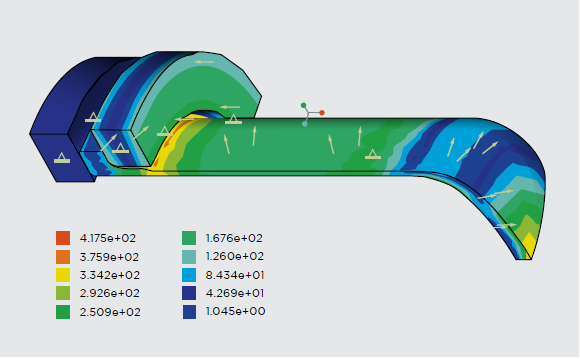
FE evaluation assembly. Image Credit: Kyocera International, Inc.
The data indicated on this table are in line with the introductory German Industrial Standard DIN 60672-2 and relate to test specimens from which they were obtained. They are not unconditionally applicable to other forms of the same material. The data must be regarded
as indicative only. All data refer to a temperature of 20 °C unless otherwise specified. The material is extremely resistant to corrosion. We would be pleased to send you brochures about the corrosion resistance of oxide ceramics. Source: Kyocera International, Inc.
Material properties |
|
Unit |
FZM |
FZM+ |
Main components |
|
- |
ZrO2, MgO |
ZrO2, MgO |
Purity |
|
wt-% |
> 99.7 |
> 99.9 |
Density |
|
g/cm³ |
≥ 5.7 |
≥ 5.75 |
Open porosity |
|
Vol. % |
0 |
0 |
Average crystal size |
|
μm |
50 |
25 |
Hardness |
HV1 |
|
1,220 |
1,200 |
Compressive strength |
|
MPa |
2,000 |
2,000 |
Bending strength σm |
DIN EN 843-1 |
MPa |
500 |
650 |
Young's modulus |
static |
GPa |
185 |
215 |
Weibull's modulus |
|
- |
> 15 |
> 20 |
Poisson ratio |
|
- |
0.3 |
0.32 |
Fracture toughness KIc |
SEVNB |
MPa*m0.5 |
6.3 |
8.7 |
Max. operating temperature |
|
°C |
900 |
900 |
Specific heat |
20 °C |
J/(kg*K) |
400 |
490 |
Thermal conductivity |
20 °C
500 °C
900 °C |
W/(m*K) |
3
2.3
2 |
3.75
-
- |
Thermal expansion coefficient |
20 - 100 °C
20 - 500 °C
20 - 900 °C |
10-6/K |
9.3
10.4
10.6 |
9.3
10.3
- |
Specific electrical resistance |
20 °C
900 °C |
Ω•cm |
1010
84 |
1010
- |
Typical color |
|
- |
yellow |
white |
Energy Efficiency
In Germany, electric drives used in industry and commerce account for over two-fifths of total power use. Their respective shares of electricity consumption in these two sectors are nearly 80%. For instance, the Federal Environment Agency estimates that just using energy-efficient pumps may result in electricity savings of almost 5 billion kWh.1
According to the Federal Environment Agency’s most recent climate balance, this translates to about 401 kt of CO2 in 2019. Assuming an electricity price of 15 ct/kWh, the affected companies could also experience a reduction in energy expenses of approximately EUR 750 million.
In light of this, magnetic drive pumps featuring metallic containment shells are gaining greater attention and consideration. The power loss generated within these systems adversely impacts the efficiency of the pumps and contributes significantly to the overall energy expenses.
Ceramic containment shells differ from their metallic counterparts in that they cannot be magnetized. This characteristic helps to avoid the formation of eddy currents that can impede performance, leading to a notable enhancement in energy efficiency. As a result, the power required to operate a pump can be decreased by as much as 15%.
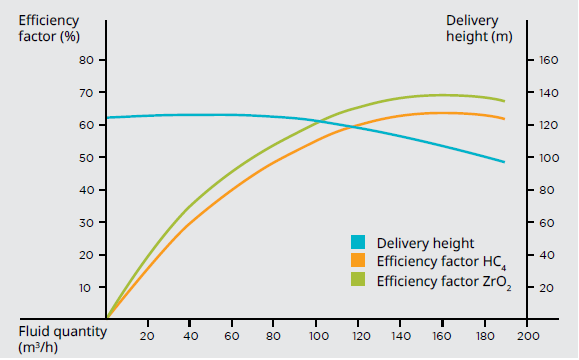
Comparison of efficiency ceramics/steel. Image Credit: Klaus Union
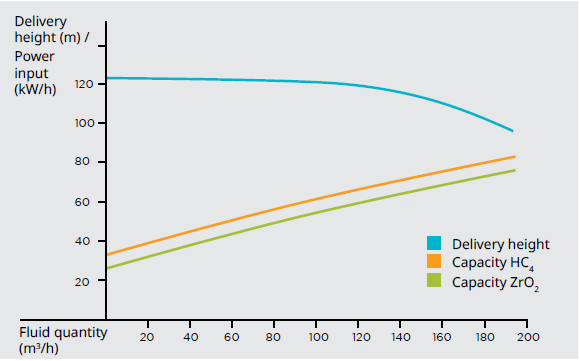
Comparison of power input ceramics/steel. Image Credit: Klaus Union
Magnetic coupling with metal containment shell. Source: Kyocera International, Inc.
. |
. |
. |
Revolutions per minute [rpm] |
1,500 |
3,000 |
Power loss [kWh] |
20,000 |
100,000 |
Cost loss at 12 ct/kWh [Euro] |
2,600 |
13,000 |
Cost loss at 15 ct/kWh [Euro] |
3,300 |
16,000 |
Cost loss at 18 ct/kWh [Euro] |
4,000 |
20,000 |
Cost loss at 3 ct/kWh [Euro] |
650 |
3,300 |
CO2 reduction [kg] |
13,400 |
68,000 |
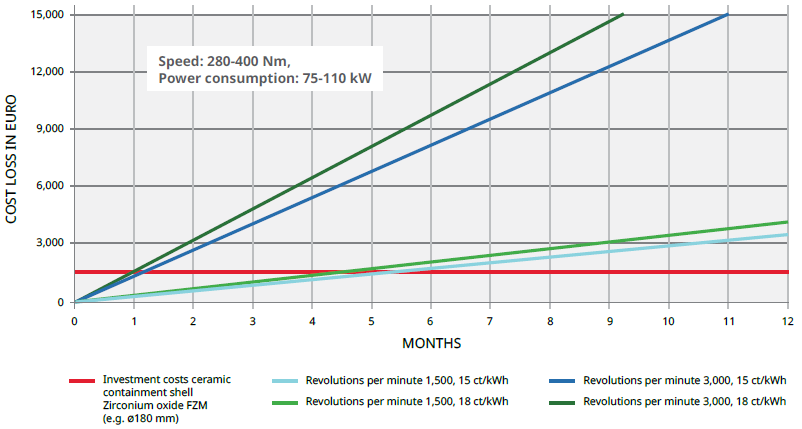
Costs due to eddy current loss with metallic containment shells. Image Credit: Kyocera International, Inc.
Conceived for Aggressive Pumping Media
Zirconia containment shells are used to pump a wide range of media, including particularly aggressive media. These can be, e.g. heat transfer oils that are pumped up to temperatures of 350 °C or heavy oils that are pumped up to 160 °C.
Other chemicals such as methanol, acrylamide, propane, ethylene oxide, nitric acid, phenol, etc. are pumped at temperatures between -30 °C and 250 °C.
To safeguard the ceramic material from the highly corrosive nature of hydrofluoric acid (HF), the inner surface of the containment shell can be treated with a chemically resistant and pore-free coating.
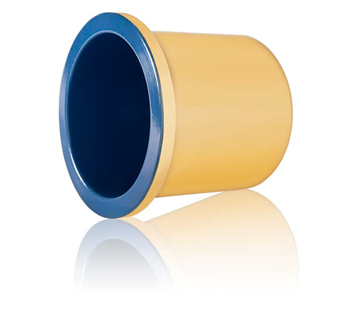
Image Credit: Kyocera International, Inc.
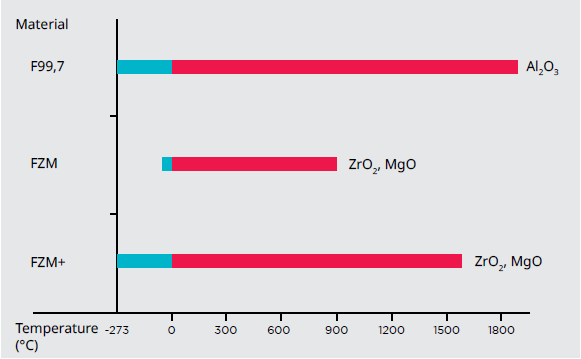
Operating temperature of oxide ceramic materials applied. Image Credit: Kyocera International, Inc.
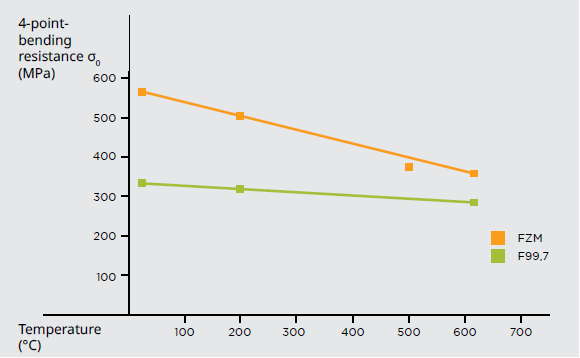
Bending resistance in relation to temperature in an oxidizing atmosphere. Image Credit: Kyocera International, Inc.
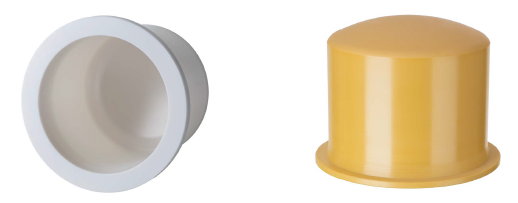
Image Credit: Kyocera International, Inc.
Corrosion Resistance List. Source: Kyocera International, Inc.
Agent |
Chemical formula |
Concentration (%) |
Temperature (°C) |
F99.7 |
FZM / FZM+ |
Methanol |
CH3OH |
all |
Rt |
A |
A |
Phenol |
C6H5OH |
pure |
Rt |
A |
A |
Nitric acid |
HNO3 |
7 |
Rt |
A |
A |
Hydrochloric acid |
HCI |
0.5 |
Rt |
A |
A |
Sulfuric acid |
H2SO4 |
2 |
Rt |
A |
A |
Excerpt. The full list is available on Kyocera's website.
A resistant
Rt room temperature
Explosion Proofness
Directive 94/9/EC, which addresses equipment and protective systems for use in potentially explosive environments (ATEX), does not impose restrictions on incorporating ceramic containment shells into Group II Category 2 devices for use in Zone 1 areas.
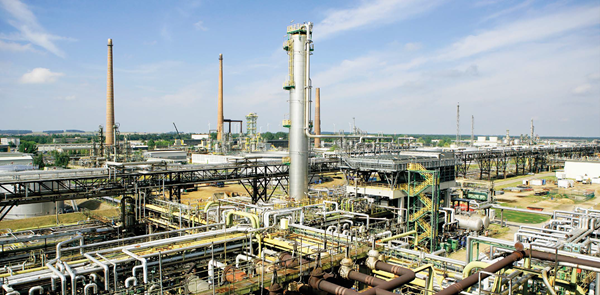
Image Credit: Kyocera International, Inc.
Extensive tests were undertaken in partnership with the National Metrology Institute of Germany (Physikalisch-Technische Bundesanstalt) in Braunschweig to assess antistatic discharge capability according to IEC 60093 and IEC 60167 standards.
Eventually, it was determined that implementing an extra external layer could significantly surpass the thresholds for surface resistivity and discharge resistance (RA < 106 Ω). As a result, a modified ceramic containment shell can be operated in contact with all inflammable media and in any explosive, hazardous or highly volatile atmosphere.
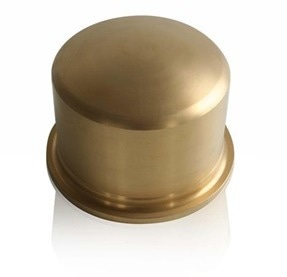
Image Credit: Kyocera International, Inc.
Coating Example. Source: Kyocera International, Inc.
Properties |
Unit |
Specific value |
Coating thickness |
μm |
approx. 3 |
Service temperature |
°C |
< 450 |
Microhardness |
HV 0.05 |
2,300 ± 400 |
Density |
g/cm-3 |
5.2 |
Thermal conductivity |
Wm-1K-1 |
30 |
Electrical resistance |
μΩ*cm |
25 |
Color |
- |
gold |