TempCHEK is mostly used to confirm the reproducibility and thermal uniformity of heat work produced by a specific heating profile. By measuring the final TempCHEK dimension with a digital micrometer and putting the measurement into the TempCHEK Trakker software, which converts the final dimension into a temperature equivalent, TempCHEKs offer a simple way to digitize and record the firing process.
In addition to being widely employed in the investment casting and structural clay industries, TempCHEKs are also useful in the advanced ceramics, refractories, grinding wheel, whiteware, and dental implant sintering industries. The carefully manipulated ceramic materials used to create TempCHEKs shrink over a significant temperature range. After being exposed to the fire process, they are measured, and their dimensions are used.
A TempCHEK’s value lies in its ability to confirm that the kiln is producing the desired amount of heat work each time a particular heating profile is applied.
With the use of software, users can have up to nine locations’ process temperatures automatically tracked by only entering the TempCHEK dimensions from each location following each firing. Air temperatures are developed with a 60-minute hold period and a ramp rate of 1 degree Celsius per minute up to the setpoint. For hold times longer than sixty minutes, a corrective graph is offered.
As ceramic materials are heated in a kiln, they undergo significant modifications that are essential for the development of particular qualities. Control of the heating cycle is believed to be a vital variable in creating important product qualities for the production of a high-quality product.
Temperature control alone is ineffective for creating high-quality products. The temperature and the duration of temperature exposure have an impact on ceramic materials. Controlling requires keeping an accurate eye on the temperature and the time. TempCHEK measures the energy input into the firing process, also called heat-work, which is the result of the combined influence of temperature and time.
The materials used to make TempCHEK are comparable to those used to make ceramic goods.
As a result, the TempCHEK and the ware respond to heat work in the same way. Densification, which is demonstrated by shrinkage, is a crucial thermal response that ceramic materials experience. To precisely monitor the heat work within the process through shrinkage, Orton created the TempCHEK to undergo a high degree of shrinkage.
When translated to a heat-work temperature, the shrinkage measurement can indicate whether or not the intended fired property was achieved.
The following temperature ranges are covered by the four versions of TempCHEK that Orton produces:
850 °C - 1100 °C (1560 °F - 2010 °F)
950 °C - 1100 °C (1740 °F - 2010 °F)
1075 °C - 1420 °C (1970 °F - 2580 °F)
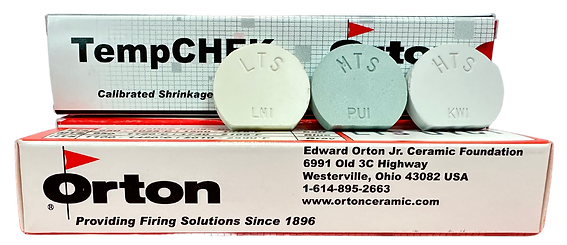
Image Credit: Orton Ceramic Foundation
Why Use Tempchek and When Are They Used?
- To enhance the process
- To keep an eye on process control
- For preventative upkeep
A thermocouple’s measurement of the actual temperature within a kiln does not accurately reflect the amount of heat absorbed by the product inside the kiln. A thermocouple can only record the temperature at one specific spot, which is often in the kiln’s sidewall or roof. Users can put TempCHEK anywhere in the kiln to determine how much heat is produced there.
The quantity of energy absorbed over time by radiation, convection, and conduction inside the ware setting is reported by the TempCHEK. The process’s uniformity and repeatability can be observed and enhanced using heat-work measurements.
Although they are reliable instruments, thermocouples and electronic devices operating kilns can malfunction. Over their useful lives, thermocouples can deteriorate and break suddenly.
Electronic controllers require calibration and tend to deviate from specified values over time, resulting in an inaccurate temperature reading. TempCHEK can be trusted to report fundamental process changes since they are not susceptible to degradation. They can be utilized regularly to identify trends and take action before they negatively impact the product.
Can They be Used for Statistical Process Control?
Up to nine places within a kiln can be monitored using the Orton TempTracker software to determine the kiln’s homogeneity and the process’s repeatability. The software generates a control chart that monitors reflected changes to gas burners or power outputs, dampers, ware setting patterns, and air flows.
It is possible to fine-tune more until a steady state is reached. All of Orton’s clients are eligible for free access to the TempTracker program.
How are they Measured?
After the firing cycle, gather the TempCHEK and use the Orton Desktop gauge to measure the fired diameter. A high-temperature marker, scribe, or nail tip can etch some identification onto each TempCHEK before it is used. Placing the TempCHEK as close to the same spot each time is best practice. In the TempTracker software, enter the measurement and track the outcomes.
How is the Shrinkage Transferred to Temperature?
To gather information for the shrinkage conversion tables they include with every batch of TempCHEK, Orton runs many firings in a closely monitored kiln. Orton engineers do calibration firings using a predetermined thermal profile. The profile calls for a final heating rate of 60 °C per hour, followed by a peak temperature hold of one hour.
More data is available to modify the heat-work temperature for hold lengths longer or shorter than the typical one-hour hold time. The temperature on TempCHEK represents the quantity of heat-work absorbed. Real temperature is not represented by the temperature linked to the shrinkage value.
If the user wants even more control, Orton can create firing data tailored to the thermal profile, make a batch of TempCHEK and reserve it for a long time, or set up blanket product releases to spread out the expense.
Each batch has tables that allow the fired dimension to be converted into an equivalent temperature.
Product Features and Benefits
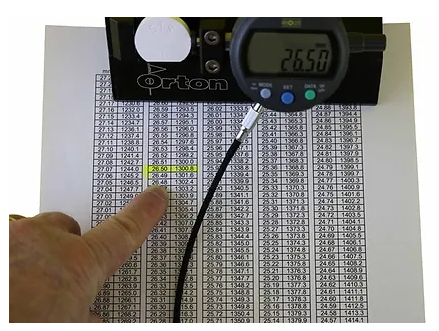
Image Credit: Orton Ceramic Foundation
- Verifies process temperature independently
- Able to quickly check the load's temperature
- High susceptibility to modifications in the process
- The recorded temperatures do not change over time
- Economical
- Easy to employ
- Stable on shelves
- No-cost software
- Product labeling on every component
- Extremely precise gauge that can be used with software
- Orton’s technical assistance