As engineering plastics replace metals in many applications, engineers are having to come to grips with a whole new lexicon of performance parameters to ensure they specify the right material for the job.
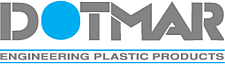
This is happening as an expanding range of engineers now understands broadly that today’s families of super plastics can be engineered to provide outstanding impact resistance, wear resistance, light weight, great strength, great cleanliness and self-lubricating properties (attributes invaluable in applications as diverse as gears, sheaves, conveyors, pump components, wear surfaces and non-slip bin and hopper designs).
Even one of the Grandfathers of modern engineering thermoplastics, Ertalon - commonly recognised as nylon - can be engineered to suit multitudinous applications requiring different qualities (including high mechanical strength, stiffness, hardness and toughness, fatigue resistance, high mechanical damping ability, good sliding properties, noise damping, electrical insulating, dielectric properties and excellent wear resistance).
The latest engineering thermoplastics can provide even more superlative qualities, including some thought next to impossible just a few years ago: eg, Nylatron®703 XL, which features ‘Zero Slip-Stick’ performance for precise and efficient motion control of machinery components including wear pads, bearing blocks, wear guides and linear bearings.
But before the enterprising engineer sets foot in this fascinating new world of high performance plastics, it is critical to become familiar with some of the key measures and limits of thermoplastic performance. These will aid understanding of which materials are best for particular jobs and which are not. Here we look at a number of key measures all of which interrelate to help determine an engineering plastic’s suitability for the job in hand.
Tensile Strength, which is a major measure of strength (although strength can also refer to compression strength). The ability of a material to resist breaking under tensile stress is one of the most important and widely measured properties of materials used in structural applications. The force per unit area (MPa or psi) required to break a material in such a manner is the ultimate tensile strength.
A common engineering thermoplastic such as Ertalon 6PLA has a tensile strength of 85MPa, which is lower than commonly used metals, but with a density of only 1.15g/cm3, its strength-to-weight ratio is far better than the metal equivalent. Material such as Celazole has a tensile strength of 140MPa, for those applications where extreme strengths are required.
Compression Strength, is the stress that a material can withstand under compression (squash). With plastics, there generally is no ultimate or yield compressive strength, because the material slowly deforms rather than suddenly failing. This strength is normally measured by 1, 2, 5 or 10% strains (squash or deformation). This is an area where engineering thermoplastics are normally very suitable, ie wear pads, bushes and sheaves. One particular application that an engineering thermoplastic is often used is rollers or wheels. Because of the elastic nature of plastics compared to metals, when a plastic roller is loaded, the contact area between the roller and the counter face is larger than that compared to metals. As a result, the stress experienced by the plastic is lower than that of a metal roller under the same conditions.
Flexural Strength and Torsional strength. Other measures of strength required less often include torsional and flexural strength. Flexural strength represents the strength of a material when a beam of it is subjected to bending. The material in the top of the beam is in compression (squeezed together), while the bottom of the beam is in tension (stretched). Somewhere in between the stretching and squeezing there is a place with no stress and it is called the neutral plane. A simple beam supported at each end and loaded in the middle is used to determine the flexural modulus given in properties tables. Skis, a fishing pole, a pole vault pole, and a diving board are examples of parts needing high flexural strength. Torsional strength represents the strength of a material when a shape is subjected to twisting. An example of a part with a torsion load is a screw as it is being screwed in. The drive shaft on a car also requires high torsional strength. This is an area where plastic materials generally are not suitable, as the stiffness of plastics tends to be very much lower than alternative engineering materials such as metals.
Temperature: referring to the max continuous (5000hrs) allowable operating temperature. This temperature is derived by noting when the tensile strength of the material is 50 per cent of that when at normal room temp (23 deg C). (Materials can operate above this temperature, but the mechanical properties are significantly reduced).
Engineering thermoplastic materials normally can operate at continuous temperatures of 100-120 C0 , with short term (few hours) allowable operating temperatures up to 240 C0 . But, if required, there are engineering thermoplastic materials that can operate up to 310 C0 continuously, and 500 C0 for short periods.
Thermal expansion refers to the amount of expansion (and contraction) of materials with change in temperature. These numbers are higher than those of metals (ie not as good), but the important fact is to design in accordance to these properties, eg: for long wear strips, incorporate scarf cuts (45 deg cut) to allow for thermal expansion; or for bearings design a running clearance that allows for thermal expansion, ie add a small additional gap between the ID of a bush and the shaft. This can be calculated by engineers such as those in our national network, or using CAMSAD (Computer Aided Material Selection And Design), which is a program designed to help design sleeve bearings, thrust washers and wear pads.
Source: Dotmar EPP