Hardide Coatings Limited, which has developed a revolutionary tungsten carbide-based coating for chrome replacement programmes, has entered into a three year coatings approval test programme with Airbus and has confidence tests being performed at seven further key aerospace industry manufacturers.
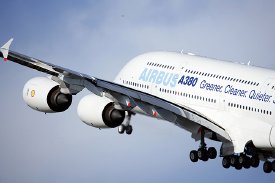
The precision coating, which made its Farnborough debut in 2006, provides excellent wear resistance against abrasion, erosion and corrosion on components made from ferrous and nickel-based alloys. It coats internal surfaces and offers significant technical and environmental advantages over hard chrome and HVOF. Independent ASTM G65 testing has shown that Hardide wears out 40 times slower than abrasion resistant AR-500, 12 times slower than hard chrome and four times slower than thermal spray tungsten carbide.
The current primary market for the coating is the oil and gas exploration and production industry where Hardide-coated components are in widespread use in extreme downhole and drilling applications around the world. The coating is also in service in the valve, power, chemical and food manufacturing industries.
Mr Neill Ricketts, Managing Director of Hardide Coatings Limited said: “Hardide secured BAE Systems approval in 2006 for use on components in the precision locking system of the overhead canopy of the Eurofighter Typhoon. We are delighted to now be in a three year test programme with Airbus, and undergoing confidence testing with other leading players.
“The unique wear properties of Hardide and the precise nature of the coating process, make it ideal for aerospace applications such as airframe, landing gear, positive locking systems, engine components and actuator-related products. It is also a cleaner process with less environmental impact than other coating technologies.”
For more information on tungsten carbide click here.