Nov 12 2008
Corus has employed its unique expertise in the use of strain measurement systems by using its new analysis tool ‘Argus’ to help Volvo Car Corporation optimise its press shop tooling at the company’s Torslanda manufacturing plant in Sweden, in support of the new XC60 crossover vehicle launch. Argus is the latest strain analysis system deployed by Corus to help carmakers ensure consistent quality of complex formed body panels at the vehicle development phase for high confidence volume production.
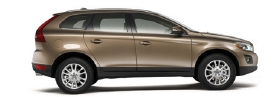
Corus will supply Volvo with steel for the bodyside panels - one of the most complex and challenging components to manufacture due to surface quality finish and formability requirements - for the new XC60 crossover model.
As part of the company’s commitment to offer added value services to its customers, Corus engineers from the company’s Product Application Centre (PAC) in IJmuiden worked closely with Volvo during the critical tool buy-off and home line tryout stage for the XC60 bodyside panels to help Volvo better understand how the steel performed during press shop processes.
Using the new Argus system, Corus was able to suggest improvements to the tooling set up to help significantly reduce press shop set-up lead times.
As with previous Corus strain analysis systems, Argus combines expertise in 3D measurement technology with materials knowledge to help OEMs confidently process today’s modern automotive steels.
Using Argus, Corus engineers measured bodyside panels to check the robustness of the pressing and fed back the first results to Volvo engineers, critically within hours as opposed to days, significantly reducing the time and resource required for successful tool tryout.
In addition, the information gathered by Corus’ engineers using the Argus system can now be used by Volvo to assess any future potential changes which may be required in the production of the bodyside panels, for example if new grades of steel are considered for introduction during the XC60’s current life cycle.
Another key benefit of the Argus system over more traditional methods of strain measurement is that it is easily portable and can be deployed and used on site in the Volvo production press shop.
Jamie Howles, Support Engineer, Corus Strip Products IJmuiden said: “With the growing use of high-tech steels in today’s automotive press shops, it is increasingly important for carmakers to better understand how steel blanks will deform and flow as they are pressed. This is particularly important for large and complex components such as bodysides.”
Mr Howles continues: “OEMs are also increasingly under pressure to find the right balance between quality and time. Through the use of unique strain analysis systems like Argus, which combines accurate measurement of 3D geometry with the latest forming analysis techniques and materials expertise, Corus is able to offer carmakers the ability to reduce lead-times during the tryout stages resulting in a ‘right first time’ approach in the production of critical stamped parts. We are delighted to support key customers like Volvo to offer this added value service.”
Corus has successfully deployed on-site strain measurement systems with other automotive customers including working at NedCar’s assembly plant in the Netherlands, to help optimise final press tooling for the manufacture of the Mitsubishi Colt, as well as working at Ford’s Genk plant in Belgium to help the carmaker save valuable time, cut costs and ensure consistency in quality.