Jan 28 2009
Custom-fit is a European funded project which has developed a new and cost effective way to manufacture fully customised products, individually designed starting from body geometries and putting together rapid manufacturing, information technologies and material science.
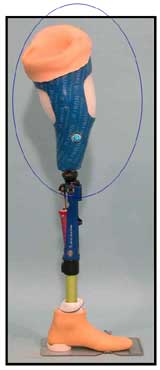
This is in short the Custom-Fit idea: geometrical characteristics are captured using 3D scans, then these data are used to adapt product shape with specialized CAD (Computer Aided Design) and finally products are made with Rapid Manufacturing technologies, the so called additive techniques which print in layers, avoiding the need of expensive moulds.
The production of prosthesis is one of the demo-case chosen to try out this new manufacturing concept, specifically the transfemoral prosthesis socket, that is the interface between the residual limb and the artificial leg (cf. Fig). Its main functions are to contain and protect the residual limb and to transfer forces from the residual limb to the prosthesis in all the patient’s activities (walking, standing, etc). It must be comfortable, wearable and durable. And to obtain all this, it needs to be perfectly shaped to the patient’s residual limb, so it is a perfect Custom-Fit test bench product.
Inail Centro Protesi, in Italy, has been involved in the Custom-Fit project so as to test the new technology. Manual work is dominant in the traditional manufacturing process. A 1st male cast is used to thermo-form the 1st socket (called 'check' socket); then this socket is tested by the patient and modified according to patient feedback. After this, a second male cast is made in order to manufacture the definitive socket, composed by an inner soft thermo-formable layer and an outer composite structure.
So, a 2 step process, requiring 2 male casts.
This is instead what happens with Custom-Fit technology
A 1st socket design is generated by a specialized 3D CAD starting from a specific set of measurements taken directly from the stump. Then the check socket is manufactured with an additive technique (Stereo Lithography Apparatus - SLA) without the need to produce the 1st male cast.
After the Check Socket has been tested, the modified shape is scanned by a specific probe scanner which generates the inner surface, from which the definitive socket is designed, with an automated CAD tool developed by project partner Materialise. The Definitive Socket is finally produced with a brand new Rapid Manufacturing technique, called Plastic Powder Printing (PPP), developed by Custom-fit partner De Monfort University.
So, thanks to 3D scanning and Rapid Manufacturing techniques which build parts layer by layer directly from 3D CAD file, the use of male casts is avoided. This leads to time savings, shortening the delivery time of the socket from when the patient first comes to the hospital to when he/she is discharged.
Moreover, Rapid Manufacturing allows to control thickness of the socket, having more intelligent structure, reinforced where strength is needed and lightened where it is not.
In most European countries there is constant pressure on budget reductions for public health institutions. Being able to reduce timescales while delivering a solution that is even better and of a higher quality would be very interesting for these parties, not to mention the satisfaction of the patient who will undergo less time hospitalised. Currently, on average, a complete rehabilitation program for a transfemoral amputee lasts 25 days: Custom-Fit technology could reduce this by 30%, about 7 days, that at an average cost per day of around 330€ means a saving of more than 2,000 € for each patient.
Custom-Fit does not want to stop at this stage. Partners in the project, like Politecnico di Milano, are working to develop a technology that will enable us to get the right fit first time, avoiding the need for the Intermediate Socket testing.
This will be possible with a Virtual Simulation tool that can make a complete modelling of a patient’s stump, including the dynamic behaviour of muscle and bone. Not science fiction, but basic research: it’s just a matter of time…