Feb 12 2009
Linde Gases, a division of The Linde Group, today announced its agreement with POSCO in South Korea for the installation of its REBOX® Direct Flame Impingement (DFI) technology. POSCO is the world’s fourth largest steel producer, and the installation, scheduled for October this year, is for improvements to one of the company’s continuous annealing lines at their large integrated steel mill in Pohang.
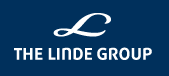
The main benefits of Linde’s patented DFI technology, where oxyfuel flames directly heat the moving metal, include significantly higher heat transfer rates which result in increased capacity and reduced fuel consumption. The technology also delivers the capability to influence surface properties and allows for easy retrofits due to the unit’s compactness.
Benefits of the installation to POSCO will be increased production capacity. Linde’s REBOX DFI unit provides a guaranteed level of preheating which will be capable of achieving approximately 15% higher capacity in the annealing furnace. The natural gas fired DFI unit will consist of 4 oxyfuel burner row units with a combined capacity of close to 6 MW.
“This is a prestigious contract for Linde,” said Dr Joachim von Schéele, Marketing Manager of Metals and Glass at Linde. “POSCO is not only one of the most important international steel producers, but is recognised for employing the best technologies. This is our second technology contract with POSCO, having previously supplied our DST technology for stainless wire annealing. POSCO’s decision to also install our REBOX DFI technology is further verification of Linde’s status as a world-leading gas technology supplier”.
REBOX oxyfuel solutions are employed in over 100 reheating and annealing furnaces worldwide. Compared to air-fuel solutions, oxyfuel can boost production throughput by up to 50%, reduce fuel consumption and CO2 emissions by the same amount, in addition to also reducing NOX output. The added DFI solution provides further advantages over inductive heating. REBOX DFI has previously been employed by Outokumpu for stainless steel annealing in Sweden and at ThyssenKrupp Steel’s galvanizing facilities in Germany.