Kingspan Access Floors, the UK's leading manufacturer of access flooring systems has recently introduced a pioneering recycling plan to help reduce the amount of waste generated by the installation of its floors that ends up in landfill.
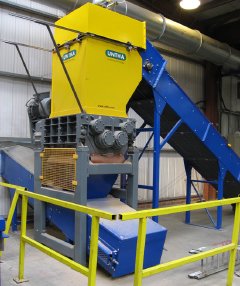
Though relatively little waste is generated in the manufacturing of Kingspan floor panels, during site installation, approximately 2.5-5% of the net floor area results in off cuts. Under their new programme, Kingspan are offering to receive site returns of off-cut panels from their customers, which they then separate at their plant in Hull in a shredding machine, before being recycled.
After being separated in the shredding machine, the steel is recycled and the chipboard is returned to Sonae, to be put back into the manufacturing process. This has the benefit of preventing site waste from ending up in landfill.
Danielle Clayton, Sales and Market Coordinator of Kingspan Access Floors explains:
"At Kingspan, we are always looking for ways to make our manufacturing processes more environmentally friendly. As a UK manufacturer, we are able to take advantage of vehicles returning from site to collect these materials for our recycling programme. This part of the process is much more difficult for European and Chinese manufacturers as the fuel consumed in returning the off cuts would be so wasteful it would completely defeat the objective - which is to reduce energy consumption and recycle waste!"
Apart from this pioneering recycling programme, Kingspan are also accredited to ISO 14001: 2004 Environmental Management, purchase their electricity exclusively from renewable sources and use steel containing 20% recycled material in the manufacture of their floor panels. All the floor panels are manufactured in the UK from FSC (Forestry Stewardship Council) approved timber, thereby reducing carbon footprint to a minimum.