DSM's new compounding facility in Ranjangeon/India, situated not far from the city of Pune, has now been equipped with ZSK MEGAcompounder PLUS compounding extruders from Coperion GmbH, Stuttgart. Mainly serving the Indian market, this largest compounding facility in India produces the polyamide compounds Akulon (PA 6) and Stanyl (PA 4.6) as well as a range of PBT / PET compounds. In addition to the abovementioned extruders, Coperion has also equipped DSM with a laboratory extruder of the ZSK MEGAcompounder series with downstream pelletizer for the production of relatively small batches and sample quantities and for product optimizing applications.
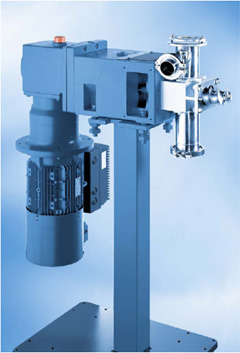
The compounders have been in operation since the end of 2008 and are working to the customer's fullest satisfaction. The new DSM greenfield facility, which tripled capacity for the production of DSM's engineering plastics compounds in India, produces materials for manufacturing moulded components for the automotive, electrical and electronics and consumer goods industries. It was officially opened at the beginning of March 2009. In less than a decade, DSM has achieved market leadership position in relevant markets in India. Among others, DSM have been approved for more than 20 parts in under the bonnet components and parts for transmission for the Tata Nano car, which was launched in March.
What decided DSM in Pune in favour of Coperion were - besides its excellent experience with previous generations of ZSK extruders - the innovations introduced by Coperion in recent years for output improvement. These innovations are, in particular, Coperion's ZSK MEGAcompounder PLUS technology and its new ZS-EG twin-screw side venting unit, the latter being important precisely for the production of polyamide compounds. The starting point for output improvement is the specific torque on the screw shafts, which has been increased by 20% to 13.6 Nm/cm³, permitting a higher filling rate in the extruder barrel and a higher screw speed. And since a high filling rate can adversely affect the efficiency of a normal vent through deposits of material, especially when processing polyamides, the above-mentioned ZS-EG twinscrew side venting unit is the ideal solution, for it features a large cross-section vent without allowing egress of the polymer melt from the extruder barrel, while vapour and/or gas are reliably extracted via the axially open screw channels.
Within the few months of their trial period prior to the official opening of the compounding facility, the large compounding extruders had already proved their ability to achieve their promised output rates. Moreover, thanks to the twin-screw side venting units, they will be able to maintain these rates in continuous, long-term operation. Nitin Kothari, Managing Director DSM Engineering Plastics at the new DSM compounding facility, puts things in a nutshell: "In actual practice we have come to appreciate the easy, trouble-free operation of the ZSK MEGAcompounder PLUS, its high output, its reliability and its flexibility when it comes to changing over from one formulation or product to another."