Coperion GmbH, Stuttgart/Germany, has not only improved its range of WRG waterring pelletizers for the pelletizing of polystyrene (PS) and polyoxymethylene (POM) but also extended it by the addition of new sizes of machine. One of these pelletizers, a WRG 320 for the pelletizing of PS with an output of 5,000 kg/hr, has already been giving satisfactory service for the past two years. A larger pelletizer, a WRG 400 rated for 9,000 kg/hr, was recently delivered to the same customer. Several waterring pelletizers of similar design for the pelletizing of POM at output rates of up to 6,000 kg/hr are being used by various companies in the Far East and are likewise giving very satisfactory service.
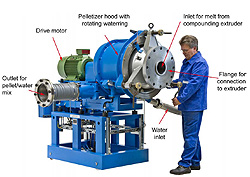
The advantage of these watering pelletizers is that the cooling and conveying medium, water, does not come into direct contact with the die plate. The rotating knives cut the extruded strands of melt into pellets. The still hot pellets are catapulted by the centrifugal action of the knives into the rotating waterring, which then cools them and conveys them out of the pelletizer hood. Thus it is that waterring pelletizers feature an extremely compact design and are distinguished both by low investment and operating costs and by a very simple start-up process. A decisive factor are the relatively negligible investment costs of the die plate, which is of simple design, as it is not exposed to any high temperature gradients between the polymer melt and the cooling water. Only a very short passage of melt is required in the melt nozzles, which in turn not only reduces the pressure acting on the die plate but also makes for a more gentle treatment of the melt. Moreover, the geometry of the nozzles can be adapted within wide limits to the specific requirements dictated by the desired shape and size of pellet. The favourable operating costs result from:
- the low energy requirement for the die plate and the rotor drive,
- the negligible wear on the knives and the die plate (the design of the system prevents cavitation erosion of the die plate) and
- the simple start-up process, which requires a minimum of time and therefore saves costs, especially in cases where changeover from one product to another occurs frequently.
As the die plate does not come into contact with the cooling medium, its temperature remains constant during operation. The melt does not freeze in the flow channels, not even in cases where the output rate is very low. Consequently, these waterring pelletizers give reliable operation within a wide output range. Under normal operating conditions, the pellets are extremely uniform, which means that they can be easily handled downstream, exactly metered either by weight or by volume and, when processed by an extruder or an injection moulding machine, readily conveyed and plasticized in the barrel or cylinder.