In addition to the traditional processing of pourable thermosets, complex components for the automotive and electronics industry in particular are also manufactured from BMC moist polyester materials. The characteristics of this material are very similar to those of metals like aluminium, permitting this material to be used as a substitute for these more costly materials. Its good mechanical strength, thermal resistance, efficient insulation and low shrinkage values have made BMC an ideal material for thermoset processing. Through its recent developments, Arburg is making an important contribution to further automating the series production of BMC moulded parts.
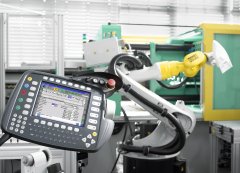
Arburg is resolutely pressing ahead with research and development in this field. This is frequently giving rise to innovations that will enable thermosets and moist polyesters, in particular, to be processed more efficiently. For example, in recent years the 'classic' injester piston feeder device has been supplemented by a version with a conveying screw. The company is also using a demo system for the automated manufacture of an insulating rail for domestic irons to show how the production process of BMC items can be automated practically.
Injester screw feeder device
To convey BMC moulding compounds, Arburg has developed a screw feeder device that forces the fibre-filled material through a conveying screw with a diameter of 300 millimetres in parallel with the dosing process in the plasticising cylinder. The conveying screw is regulated and driven by a servo motor.
The stuffing pressure is measured in the cylinder's material inlet, programmed by means of the Selogica machine control system on the Allrounder and regulated via the screw rotation speed so that the material is conveyed to the cylinder under constant pressure, regardless of the filling level.
The maximum screw rotation speed is 5 rpm. As a result, the material is always transported carefully to the cylinder without damaging the fibre.
The filling level of the material reservoir is monitored. The need to refill the material reservoir is indicated by a signal lamp and an additional message in the control system, although material can be added to the reservoir at any time.
Using this new version of the injester, the BMC material can be fed to the processing stage with even greater care and convenience. The processing stage is made transparent and easy to manage through the programming and monitoring of the tamping device via the Selogica machine control system.
A consistently high standard of product quality is ensured by measuring the stuffing pressure in the feed chamber of the plasticising screw. This makes dosing extremely accurate and very constant and this is borne out by the only slight variations in dosage times.
Examples of automation: BMC production cell for manufacturing insulating rails for irons
The automated production of BMC items by integrating production steps upstream and downstream of the injection moulding process in one production cell will be visually demonstrated by a project in which insulating rails for irons will be manufactured in series production. The production unit combines an Allrounder 570 S as well as a six-axis robotic system that performs not only the part removal sequence but also all the downstream processing steps.
The standard injection-moulding machine is fitted with a "thermoset package" for processing thermosets, which provides all the necessary hardware and software components as standard. For control purposes, the Selogica system operates using a thermoset program that has extended functions, such as venting or closing the mould at the specified temperature. Also available are special cylinder modules and screws equipped with a flightless non-return valve for low-shear material processing. The BMC compound is continuously fed to the injection unit by means of the screw injester. The parts are manufactured in an electrically heated, single-cavity mould at a mould temperature of 140°C in a cycle time of 60 seconds. The mould is fully insulated to efficiently prevent heat from being emitted into the environment. The entire post-processing of the moulded parts takes place within the cycle time and this maintains a high level of productivity.
The flashes on the finished parts are removed using a brush station with suction. To achieve a correspondingly high level of part quality, the items must first be cooled down to room temperature. This is achieved using a cooling station for ten finished parts, which ensures the required dwell time. A check for flashes is performed visually using an image processing system. At the end, the finished parts are placed on a set-down system with work-piece carriers which have a space-saving arrangement and can be changed without interrupting production. The production cell is therefore designed for unmanned production.
The parts handling tasks are carried out in their entirety by the flexible six-axis robotic system, which is easy to operate thanks to the tried and tested Selogica user interface integrated into its control system. The complex handling tasks are programmed according to the same principles as those used for the Selogica machine control system. This means that no specialised knowledge is required for programming. The machine installation technician is able to program all movements of the six-axis robotic system using the proven graphic sequence programming within his familiar injection moulding environment, without any outside assistance.
The exact sequence for transporting the finished parts with the six-axis robotic system is as follows: First the items are removed and set down on the cooling station. These parts are then exchanged with suitably cooled moulded parts. The transfer of finished parts is based on the principle of 'first in, first out'. By guiding the contours of the insulating rails accurately along the brush station - a movement sequence that can only be performed in this manner using a six-axis robotic system - the burrs are completely removed. The six-axis robotic system then places the items in front of the optical inspection station. Following this inspection, the system decides whether the moulded part is 'good' or to be rejected. Based on the inspection result, the good parts are transferred to the work-piece carriers whereas the rejected parts land in a rejects crate. The good parts are set down upright with the corresponding care and in a space-saving layout matching the contours of the work-piece carrier.
Advantages of automation
Besides the integration of all downstream processing steps, the production process is extremely economical, particularly through its use of the flexible six-axis robotic system. As with the cooling of finished parts based on the principle of 'first in, first out', the post-processing with contour precision, the reliable separation of reject parts and the careful set-down all result in optimum product quality. The finished parts are inspected 100% and the items can be carefully set down in work-piece carriers in an arrangement that saves space. With this production unit it is possible to achieve production requiring little manpower as well as a much simpler logistics process.
Complete process monitoring with Selogica
The entire process sequence is extremely transparent and easy to monitor as the six-axis robotic system is incorporated into the Selogica machine control system using the Euromap interface and another special data interface. Furthermore, the operating philosophy of the machine control system has been carried over to the six-axis robotic system in order to efficiently simplify the previously complex programming that used to require specialised knowledge.
Arburg offers the Sel