A first-of-its-kind polypropylene-based, high-clarity copolymer for potential use in extrusion and injection blow molding applications is the latest addition to LyondellBasell's innovative family of metallocene-based resins.
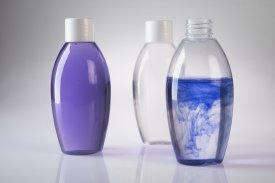
Produced using the company's proprietary single-site catalyst, the Metocene RM2231 resin combines excellent transparency with the typical attributes of polypropylene-based copolymers, such as flowability, thermal and impact resistance, and recyclability. "The Metocene RM2231 resin addresses cosmetics packaging requirements for glass-like clarity and gloss." said Jean-Pierre Bideau, application development manager for metallocene-based resins at LyondellBasell.
One of the highest-clarity polypropylene-based resins
One millimeter injection molded plaques produced using Metocene RM2231 resins showed only four percent haze, exceeding the values of previous benchmarks which showed six to 10 percent haze. "Compared to competitive standard polypropylene, the new grade is currently one of the highest-clarity polypropylene-based materials available on the market," added Bideau. With a high level of transparency and a melt-flow rate of 3.5 g/10minutes, the new Metocene resin can be considered as a replacement for amorphous, transparent polymers used in cosmetics applications, which are traditionally the domain of injection blow molded PET. The grade also offers a low density that can translate into weight and material savings.
"We were able to combine the clarity and gloss of PET with the density and recyclability advantages of polypropylene," said Bernd Schütz, marketing manager for Metocene resins at LyondellBasell. "Customers have begun replacing PET applications produced using injection blow molded technology with Metocene RM2231 resins processed on extrusion blow molded equipment, as they have found the new grade to be a more cost-effective solution."
Compared to conventional polypropylene materials, the new resin also provides improved surface characteristics in non-transparent applications using aesthetic pigments. In addition, the Metocene RM2231 resin does not require pre-drying and the high processing temperatures associated with other resins such as PET allow converters to save time and energy costs, thereby improving the overall economics of the process. The use of proprietary single-site catalysts to produce the resin translates into products with excellent aesthetics, surface gloss and purity. The high purity enhances the resin's resistance to discoloration; it also helps to improve product economics with regrind material when used with polyamides or EVOH in multilayer barrier bottles and film.
The new Metocene RM2231 resin is produced in Europe and is commercially available worldwide.