Gustav Wahler GmbH & Co. KG of Esslingen (Germany) uses bushings made of DuPont Vespel TP polyimide to position and guide the cylindrical operating rods of EGR slip-in valves (EGR = Exhaust Gas Recirculation). These valves are used in four and six cylinder stratified-charged petrol engines. Located behind the precatalytic converter and operating at temperatures of up to 220 °C, they regulate the quantity of exhaust gases recirculated into the combustion air to reduce NOx emissions.
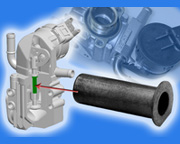
It is during this process that the bushings, made of Vespel TP polyimide, which combines excellent friction and wear performance with a very low thermal expansion coefficient, support the consistently smooth operation of the valves, including their fast and precise opening and closing.
Compared to equivalent components made of metal, the injection moulded Vespel parts provide significant long-term benefits. They are chemically inert to the residues contained within exhaust gases, whilst no contact corrosion can occur because polyimide is not electrically conductive. Additional benefits include their significantly lower weight - in part a consequence of the high performance polymer's considerably lower density than brass or steel. Also the high stiffness and tensile strength of Vespel TP, combined with its high level of formability by injection moulding, allows reduced wall thicknesses for additional design freedom.
Wahler worked closely with DuPont Performance Polymes (DuPont) from early on in the design phase for these valves, versions of which are also used in numerous engines from other OEMs. "The mutual development work with DuPont proved to be very efficient, because in this case the material producer is also the supplier of the moulded parts," comments Martin Barth, Development Engineer for petrol EGR in the valve business unit at Wahler. "Because the optimisation of material and design was conducted in collaboration, we were able to fulfil our requirements for the bushing very quickly. Moreover, DuPont took over simulation of the relatively long but thin-walled moulded part's behaviour when under servicing loads as well as across a broad temperature range from a cold start to full throttle. This helped us to optimise material usage to such an extent that we only require very little installation space, and considerably less than that required for a metal bearing."
Wahler worked with DuPont in specifying Vespel TP, principally because this material enables the cost-efficient and precise injection moulding of the bushings in a single shot, without the need for post-machining. "Despite its thermoplastic properties, Vespel TP offers the required levels of temperature resistance and dimensional stability," adds Barth. "As a result, tight tolerances are retained across a range of operating conditions and even after more than 3.6 million closing and opening procedures. It provides good acoustic attenuation properties, helping to reduce noise emission from the valves. The low levels of friction on the surface help prevent the formation of grime deposits."
Vespel TP polymers are processable as a thermoplastic and are supplied by DuPont as a finished part. They offer a high degree of design freedom, making them highly suitable for the production of moulded parts with enhanced functionality. Vespel TP polymers exhibit high levels of wear, chemical and temperature resistance, making them suitable for the replacement of metal or ceramic parts. The broad portfolio of TP grades means that a wide range of application specific requirements can be met. The TP grade specified by Wahler for the EGR valve guides is characterised by its very good mechanical properties, its high creep resistance at elevated temperatures and its particularly high impact resistance, which facilitates their press fitting in the bushing carrier.