Imatek have recently installed a 30,000J DWT40-30, Drop Weight Tear Tester (DWTT) at Ural Steel in Novotroitsk, Russia.
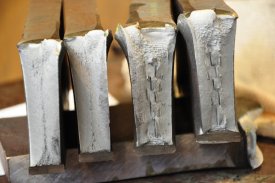
The DWT40-30 replaces an older machine and will be used to test the fracture properties of steel used in the manufacture of large diameter pipe for the oil and gas industries.
This is a significant installation for Imatek as it represents the company's first sale into Russia following the appointment of new distributor, Uralsibpromservice (USPS) based in Chelyabinsk.
Ural Steel is a subsidiary of the holding company Metalloinvest and is the largest enterprise in the South Ural region and one of the eight leading metallurgical integrated works in Russia.
The Company was founded in 1955. Today, Ural Steel is a significant niche steel producer, holding the top market position in production of strips, tube billets, bridge steel, machinery construction steel and billets for exports.
The products of Ural Steel are highly demanded in Russia and the CIS as well as on the international markets. Customers include leading enterprises from such countries as Russia, Germany, UK, Italy, Spain, Belgium, Norway, Denmark, Turkey, Iran, China, Korea, Vietnam, Taiwan and Thailand.
The use of higher grade steels in the oil, gas and manufacturing industries is creating the need for a new generation of specialist Impact Testers. Imatek offer a range of DWTT systems for measuring the fracture characteristics of steel specimens according to API recommended practice 5L3, EN 10274 and ASTM-E 436. Steel grades of X120 and specimens of up to 50mm can be accommodated.
A major feature of the Imatek range is the high-quality instrumentation and analysis software that provides detailed information, both graphical and tabular, for the specimen failure. Whereas historically the DWTT test method has not required instrumentation, more recent research indicates that it is of significant benefit when testing the tougher X-steels. Instrumentation enables crack initiation, and most importantly crack propagation energies, for the specimen to be determined which is considered a better measure of 'in-use' performance for these steels than visual assessment of the fracture surface.