Plastics processors intending to produce high-clarity polypropylene (PP) moldings now have two compelling reasons for using grades containing Milliken's next-generation clarifying agent, Millad NX8000. Not only does Millad NX8000 yield unparalleled transparency in injection- and blow-molded products, but it has also now been proven to allow significant savings in energy consumption through reduced processing temperatures and lower cycle times.
Trials recently carried out by Milliken in collaboration with leading injection molding machine maker Arburg have shown that total energy savings of around 20 percent can be commonly achieved, with some evaluations showing savings as high as 35 percent.
Milliken carried out a series of trials using an all-electric Arburg machine, the Allrounder 520 A, with a clamping force of 1500 kN to produce a utility drawer in two different grades of PP, with melt flow rates of 25 and 60 g/10 min, both containing Millad NX8000. The trials showed that by reducing the processing temperature from 240C to 200C (while leaving the cooling and overall cycle times the same), the total energy consumption of the machine and its auxiliaries was reduced by 9 percent. Since cooling time could be reduced as a result, the cycle time could be improved by several seconds, yielding a total improvement in energy efficiency for the entire machine of 22 percent. Compared to running the machine at 280C (not unusual for these types of resins), the energy savings amounted to 35 percent.
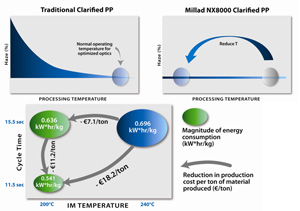
Energy savings achieved through temperature and cycle time reductions far outweighed any increases in energy consumption due to higher screw torque and injection pressures needed because of the higher viscosity of the resin under the new low-temperature conditions.
The trials involved the production of a drawer weighing 42 g. In production runs using a 60-MFR resin, "standard" production conditions at 240C required a cycle time of 15.5 s; for a run consuming one ton of material, the total energy cost was 81.9 euros (USD $114) (based on an average cost for industrial energy of Eu of 0.1177 €/kWh (USD $0.1641/kWh)).
Reducing the temperature to 200C cut the energy cost to 74.6 €/tonne (USD $104/ton), while reducing the temperature and then optimizing the cycle time at 11.5 s brought the figure down to 63.7 €/tonne (USD $88/ton).
"We knew from previous evaluations that conventional clarifiers need a certain minimum level of energy input - which typically equated to temperatures over 220C during processing - to ensure full solubility and hence performance in the final application," says Adam Newberry, technical account manager for Europe and the Middle East. "Millad NX8000 has much better solubility characteristics in PP, and these allow lower processing temperatures to be used."
With PP containing traditional clarifiers, haze increases noticeably at lower processing temperatures. The solubility of Millad NX8000 is much less temperature dependent, so lower processing temperatures can be used.
By using lower processing temperatures, converters have less heat to remove from the final part. This means they can reduce cooling time and hence, overall cycle time, leading to improved productivity. Millad NX8000's broader processing capability leads not only to direct savings in energy, but also to lower machine and labor requirements. Since labor and production costs are major contributors to overall manufacturing costs, any improvement in productivity can lead to significant savings for the converter.
The Allrounder 520 A is ideal for these types of tests. Its Selogica "energy consumption measurement" function allows the machine operator to record and analyze both the average and the periodic power consumption of the running injection molding process. Certain process modifications result in changes to the corresponding power consumption values. This data allows real-time optimization of the machine's power consumption and reduction in the energy consumption per part.
"All-electric machines are inherently low energy consumers and so the Allrounder 520 A provided the lowest baseline for our trials," says Newberry. "Reducing temperatures on this machine has a more significant percentage effect on the total energy consumption than on a hydraulic machine because the heating requirements for all-electric machines comprise a greater percentage of the total energy consumption. But in terms of absolute values for energy reduction and productivity improvements, results across all machine types are likely to be very similar."
Creating a New Standard in Processing Conditions
Milliken sees significant potential for Millad NX8000 to provide for a shift in "standard" operating conditions for customers who want to optimize energy savings without compromising product quality. "Some processors may specify a minimum processing temperature across all machines in their production facilities because they are aware of the temperature sensitivity of clarifiers they have been using until now," says Newberry. "If the melt doesn't reach a certain temperature, the final part can appear hazy and not reach its full optical potential. This has led numerous production facilities to run at below optimum conditions."
"But now Millad NX8000 is shifting the paradigm. By switching to resins containing the additive, and so removing this temperature dependency, companies can now concentrate on optimizing their processes for minimum temperature and cycle time, in the full knowledge that they will still be able to produce parts with the optical properties previously only achievable with high temperature operations."
"We think this development is a sign of the times," Newberry concludes. "All around the world now, interest is increasing in energy saving, from machine makers like Arburg with their highly configurable hybrid and all-electric injection molding machines, to processors and end users who want to increase the sustainability of their operations and finished products. Millad NX8000 provides the latest means to meet their objectives."
Milliken is now working directly with processors to help them maximize the potential of the new additive in reducing their energy bills while making the clearest PP parts ever. In subsequent field trials, using different machine types and part designs, converters have seen energy saving and cycle time successes that confirm the results achieved during the initial collaborative work with Arburg.