Jun 15 2005
BAE Systems has designed, engineered and manufactured what could be one of the most complex pieces of machining ever seen.
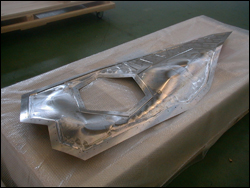
The titanium heatshield for the first F-35 JSF sits on the outside of the aft fuselage near a power pack exhaust. The heatshield protects the aft fuselage's carbon fibre panels from temperatures reaching up to 260°C.
Produced from a solid block of titanium, the heatshield looks like a giant razor blade. It is around 4ft long by 3ft wide but thins to less than 0.010inc (1/10,000 of an inch) at some of its edges – something that has not been achieved by machining techniques before. This is necessary to ensure that the heatshield does not affect the special characteristics of the F-35, particularly the highly important stealth characteristics of the aircraft.
John Duxbury, Head of Manufacturing Development at Samlesbury, said, “The heatshield is effectively an aircraft ‘protective’ panel that has been produced using machining techniques. This was necessary because the heat resistant technologies required could not be achieved using carbon fibre – which the outer surface of the aircraft is primarily made from.”
“Producing this component has been a huge learning curve for everyone involved. We conducted initial discussions with Sheffield University to help us complete feasibility studies to see if something like this could be done utilising machining technology.”
The area where the heatshield is positioned will change for future aircraft, so the component, which could be mistaken for a piece of modern art truly is a one-off.
http://www.baesystems.com/
Posted15th June 2005