Scantron Industrial Products announce the latest in their line of laser gauges for measuring thermal expansion more accurtely than ever.
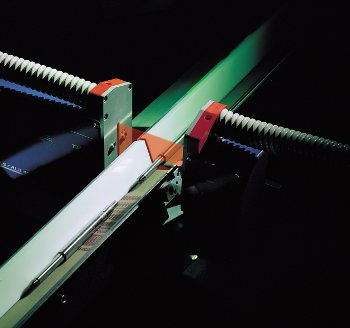
Laser measurement of product diameter has always been highly accurate. However, in non-thermally controlled environments, such as a workshop or on-line, there was always the chance of incorrect readings due to thermal expansion. Small fluctuations in the ambient temperature could affect both the laser gauge and the part, and therefore the measurement.
Now, thanks to the NO-VAR (No-VARiation) technology, this is a thing of the past, even in non-thermally controlled environments. The thermal co-efficient of the gauge and the part are determined and then stored in the instrument's memory. Sensors installed in the gauge then measure the ambient temperature and smart software compensates for temperature changes and adjusts the reading accordingly.
With high precision manufacturing requiring very tight tolerances, gauge repeatability and reproducibility (R&R) to a tenth of the tolerances or better is a requirement when demonstrating process capability (Cpk). A 10mm diameter steel part will change by in excess of a tenth of a micron per degree change in temperature of the part (Thermal Expansion Coefficient of Steel is ~12 microns per meter per degree C). The 40mm high speed Xactum gauge offers R&R of ±0.1 microns (±3σ over 1 second) and, with a resolution of 10 nanometers, can accurately measure changes in diameter of this order.
Operations, such as machining, can alter the temperature of parts. In this situation, the diameter of the part is simply measured immediately after machining and after it has returned to room temperature. An offset value is then programmed into the gauge, so it can compensate for this size variation with temperature.
To find out more about this next generation of high-accuracy laser micrometers, contact Scantron Industrial Products Ltd to discuss your application.