Tribology, the science and engineering of interacting surfaces in relative motion, is used to study the effects of different types of lubricants on friction and wear. A typical tribosystem includes a lubricant, opposing surfaces, different speeds and loads, and the application environment. Choosing a lubricant for effective performance begins with the specific lubrication or friction regime involved.
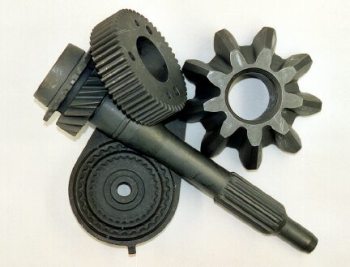
Lubrication or friction regimes
Different lubrication or friction regimes require different types of lubrication (tribological films):
- Hydrodynamic – Fluid lubricants are forced between opposing surfaces in response to relative motion (speed) and applied force (load). Dynamic pressure keeps the surfaces separated.
- Elastohydrodynamic – As speeds and loads increase dynamic pressure, the lubricating fluid is compressed to act like a solid. This causes elastic deformation of the component surfaces.
- Boundary – Surface-active materials form a lubricating film on and between the opposing surfaces. Effective boundary films require adhesion and cohesion of the active materials.
A mixed regime can occur when both hydrodynamic and boundary friction are possible. During start-up and shutdown or in transient events like shock loads, the relative motion or distance between opposing surfaces may converge toward zero. Partial hydrodynamic and boundary films may be required.
Effective lubrication
Oils and greases rely on fluid (base oil) to form effective hydrodynamic and elastohydrodynamic lubricating films. Relative motion must be present, and other factors have an impact.
- Fluid viscosity changes with temperature and pressure, affecting the lubricant film thickness.
- Oxidation, evaporation and gravity can inhibit the ability of lubricating fluids to stay in place.
- Oils and greases may be unable to maintain effective lubricating films under static loads or high loads or at low speeds, and they can be affected by extreme cold (stiffening) or heat (thinning).
Solid lubricants that make up the dominant portion of anti-seize pastes and anti-friction coatings are relatively unaffected by factors that can impact the lubricating ability of oils and greases.
- As temperatures and pressures increase or decrease, boundary films formed by solid lubricants maintain steady thickness.
- Solid lubricants are not subject to evaporation; oxidation temperatures exceed 399°C (750°F).
- Particle size and adhesive/cohesive properties help keep solid lubricants in place.
- Relative surface speeds are not required to form effective lubricating films, and loads have little or no effect on film thickness.
Anti-seize pastes and anti-friction coatings (AFCs)
Produced as fine-particle powders, solid lubricants fill in, smooth and cover surface asperity peaks and valleys. The lubricating particles adhere to the substrate and also cohere to each other to form protective layers to control friction and reduce surface wear. They are applied in two forms:
- Anti-Seize Pastes – These contain 40 to 60% solid lubricants in a mineral or synthetic oil that carries the solids to where lubrication is needed. Some are used as assembly pastes to help prevent galling and cold welding and to provide nondestructive disassembly. Others are suited for preventing fretting corrosion caused by micro-vibrations, aiding threaded connection assembly, or providing long-term lubrication or enhanced protection against rust and corrosion.
- Anti-Friction Coatings – These paintlike materials contain about 30% solid lubricants blended with a solvent carrier, resin binder and special additives. Cured AFCs are dry, work well in the presence of dust and dirt, and are not susceptible to aging or evaporation. They are effective in low-speed and high-load applications, when abrasive contaminants are present, where vibration can cause fretting corrosion, in start-up and run-in operations to reduce premature machine wear, to replace heavy metal coatings for corrosion protection, and to support oils and greases.
Anti-seize pastes and anti-friction coatings, fortified with high levels of lubricant solids, can go beyond traditional oils and greases to optimize friction; reduce wear; and provide long-lasting, effective lubrication in extreme environmental conditions.